Today, travelers board commercial aircraft routinely and confidently, knowing that they are extremely safe despite the inherent risks of air travel. On very rare occasions, a crack can initiate and grow in a critical component after repeated loading, and this can lead to costly failures in aerospace and other industries. Advanced technology helps ensure the integrity of these highly stressed structural components during the design and certification process. Ultimately, this technology may allow space tourism aboard commercial spacecraft with the same confidence.

The NASGRO fatigue crack growth and fracture software is a key safety technology helping prevent component failure. Developed jointly by Southwest Research Institute and NASA Johnson Space Center (JSC) since 2001, the NASGRO tool performs the essential calculations necessary to establish confidence in structural performance for flight vehicles and other critical mechanical
components around the world.
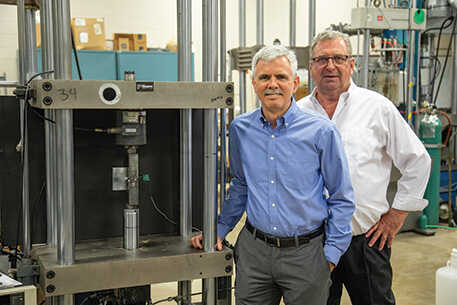
ABOUT THE AUTHORS:
Dr. Craig McClung is a senior program director in Materials Engineering with nearly 40 years of research and program management experience in fatigue and fracture, focusing on the structural reliability of components. Joe Cardinal is a program director in Structural Engineering with over 40 years of experience performing and managing structural integrity projects in a wide range of applications, including structural, stress, fatigue and fracture mechanics analyses. Both engineers work in SwRI’s Mechanical Engineering Division.
NASGRO began as the NASA/FLAGRO computer program, developed by NASA and its contractors in the 1980s for fracture control of the Space Shuttle, the world’s first fleet of reusable spacecraft. Royce Forman and Dr. V. Shivakumar led the development of these early versions. Following the tragic Aloha Airlines accident in 1988, caused by extensive fatigue cracking of the metal fuselage, NASA began extending the software to address aircraft structures. Initially NASA released the resulting NASGRO Version 3 in 1999 as a free download, but the agency soon recognized that users would need support to realize the benefits. NASA asked SwRI about joining forces to take advantage of the Institute’s world-class expertise in fracture mechanics, fatigue and damage tolerance analysis as well as a long-standing relationship with JSC.
In 2000, SwRI and NASA signed a Space Act Agreement, and SwRI took over industrial distribution and support of NASGRO, providing royalty-free software licenses to NASA and its contractors. Through this agreement and subsequent renewals, SwRI and NASA have worked together to develop and implement new NASGRO technology. A small team of fracture mechanics specialists and software engineers at Jacobs Technology in Houston also support NASGRO as contractors for NASA and SwRI.
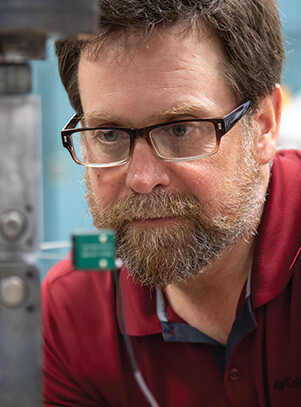
(Left) Staff Engineer Jim Feiger studies how a crack in a material sample changes over time, under cyclic loading — important data to inform NASGRO software.
(Right) Engineers verify NASGRO solutions for predicting fatigue crack growth and fracture using finite element analyses, which show the stress that created and continues to affect a crack at an aircraft fastener hole.
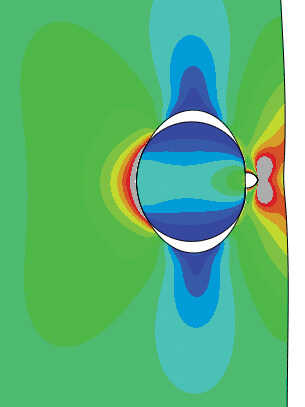
Consortium Launch
The worldwide aerospace community immediately recognized and embraced the unique capabilities of NASGRO. In 2001, SwRI organized a NASGRO consortium that included companies in nine countries, joining forces to develop the next generation of the software.
DETAIL
NASGRO’s NASMAT database contains 9,000 sets of data for various materials, including more than 3,000 sets of fatigue crack growth data and more than 6,000 fracture toughness data points.
In 2003, NASGRO 4.0 — the first version released by SwRI — received an R&D100 Award, recognizing it as one of the 100 most technologically significant new products of the year. NASA also recognized it with its Software of the Year Award. Despite this auspicious start, SwRI’s NASGRO story was just beginning. The NASGRO industrial consortium drives software advances and updates. Organized in renewable three-year cycles, the consortium has tripled in overall size during the past 20 years. Participants now include 24 companies working in more than 15 countries, designing, building and supporting spacecraft, aircraft, rotorcraft and gas turbine engines for aircraft propulsion or power generation. The unique legal framework governing consortia allows these companies — some of which are direct competitors — to work together collaboratively on precompetitive technology that supports improved safety.
The consortium participants provide expert guidance to the SwRI developers, identifying the future NASGRO enhancements most needed. This arrangement ensures that developers tackle the most important challenges and develop practical solutions for immediate application. Participants receive site licenses or corporate licenses for the resulting NASGRO versions. Companies working on different product applications have some unique needs, of course, and so NASGRO has evolved over time to become a much more powerful tool serving multiple industries.
This strategic collaboration also includes NASA and the European Space Agency (ESA), organizations that not only help identify development priorities but also help fulfill them. ESA has regularly provided in-kind contributions of new technology developed specifically for NASGRO under ESA contracts, and ESA and its contractors receive royalty-free NASGRO licenses for use on ESA projects. NASA applications of NASGRO are not limited to spacecraft. For the past 10 years, NASA has provided supplementary funding to SwRI to develop NASGRO enhancements needed to perform fitness-for-service (FFS) analyses of safety-critical ground-based steel pressure vessels. With these enhancements, NASGRO supports FFS analyses to ASME and API pressure vessel standards and expands applications to industries beyond its initial aerospace focus.
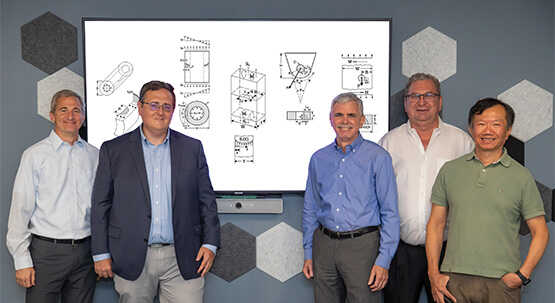
NASGRO has been growing and flourishing at SwRI for more than 20 years. The original NASGRO leaders at SwRI (from right) — Dr. Yi-Der Lee, Joe Cardinal and Dr. Craig McClung have identified and are mentoring the next generation of NASGRO leadership. Dr. James Sobotka specializes in computational fracture mechanics and joined SwRI in 2014 to support NASGRO. Luciano “Lucky” Smith has more than 20 years of practical experience at SwRI performing and leading damage tolerance analyses of aircraft structures.
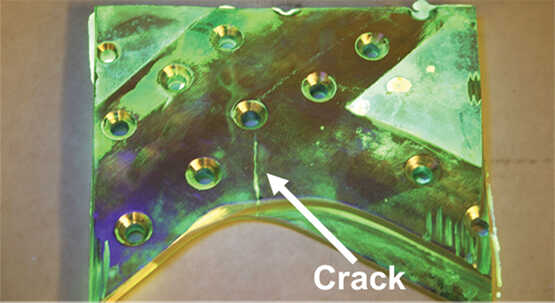
NASGRO integrates real-world data to continuously improve modeling.
Crack Growth Calculations
NASGRO performs mathematical simulations of a fatigue crack growing in a metal component. Crack models calculate the effect of the applied cyclic and residual stresses, as well as the size and shape of the crack, on the driving force for crack growth. Using material properties characterized by standardized experiments, the NASGRO crack growth equation predicts how fast a crack grows and assesses the onset of fracture, establishing the safe service life of a component. These life predictions guide inspection methods and intervals for safe operation of a component.
Crack models must be exceptionally fast to facilitate millions of calculations at many potential crack locations in a complex structure. These rapid crack models are based on idealized geometries — for example, a semi-elliptical crack in a rectangular plate — and must accommodate a wide variety of geometric shapes, dimensions and applied stress distributions while still providing highly accurate results when used as surrogates for actual components. The NASGRO team has developed many unique crack models. SwRI’s Dr. Yi-Der Lee and Dr. James Sobotka have pioneered computational methods to develop and calibrate advanced crack models for various scenarios, including complex stress gradients acting on the crack plane. These specialized configurations include tapered lugs with oblique contact loads, multiple curved cracks at rows of holes and cracks in pressurized cylinders or spheres. Powerful new computational methods verify the accuracy of new crack models by statistically comparing their results with hundreds or thousands of high-fidelity three-dimensional finite element analyses.
NASGRO v3 included 40 crack models, a number that was state of the art in 1999. The current tool, NASGRO v10.2, includes 115 crack models, far more than any other available fracture assessment software. About half of the original v3 crack models have been revised or replaced/supplemented with corresponding new crack models.
The other distinguishing feature of NASGRO is its large library of material properties for fatigue crack growth and fracture. NASGRO contains properties for more than 500 metals and alloys tested under various conditions, a number that continues to grow as new data and materials are added to its database. The NASMAT module included with NASGRO also contains the original test data used to generate the properties and can calculate properties from new user data.
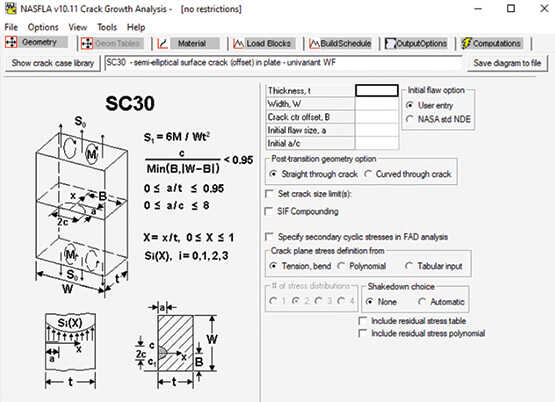
NASGRO is a suite of different computer programs for different types of fatigue and fracture mechanics analyses, including the main module NASFLA (shown), which calculates fatigue crack growth lifetimes.
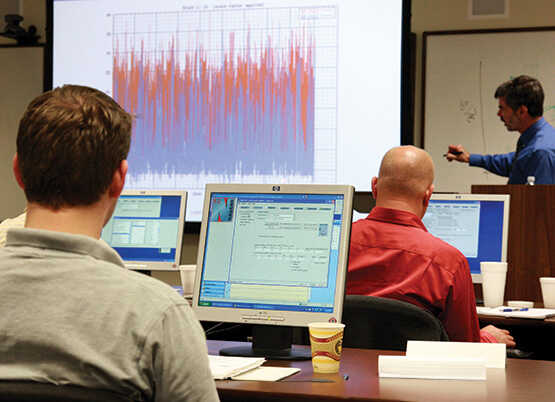
Since 2006, SwRI has conducted more than 90 NASGRO courses, teaching more than 1,800 users about fatigue crack growth theory as well as basic and advanced NASGRO capabilities.
Emerging Applications

NASGRO and SwRI’s Dr. Craig McClung and Joe Cardinal were inducted into the Space Technology Hall of Fame this year. These awards recognize life-changing technologies emerging from global space programs, increasing public awareness of the benefits of space exploration.
In addition to providing NASGRO licenses to consortium participants, NASA and ESA, SwRI also licenses individual versions of NASGRO to other users in industry and government worldwide. Over 1,000 single-seat licenses and more than 60 site licenses have been purchased since 2002. About half of these users are outside the United States. Commercial licensing extends NASGRO use to many other companies and universities for a range of applications, including railroad tank cars, ship structures, submersibles, marine structures and more.
In the past few years, NASGRO has seen significant growth in several major emerging markets. For example, NASGRO is the preeminent tool used by the burgeoning commercial space industry. SpaceX, Blue Origin, Sierra Space and United Launch Alliance are all consortium participants, and many other commercial space companies are NASGRO licensees. NASGRO is also attracting substantial attention from the rapidly expanding advanced air mobility industry. Developers of eVTOL (electric vertical take-off and landing) air vehicles as well as electrified conventional aircraft are using NASGRO to design and certify products for safe operation.
NASGRO’s exceptional technical capabilities, which include extensive libraries of crack models and material properties, put the tool in a class by itself. NASGRO is a suite of eight complementary programs used to analyze fracture and fatigue crack growth. These integrated modules include user-friendly graphical interfaces that facilitate the calculation of stress intensity factors, critical crack size, fatigue crack growth life and material properties.
Responding to requests from NASGRO users within NASA and the consortium, SwRI developed a 20-hour NASGRO training curriculum in 2006. The curriculum covers basic fatigue crack growth theory as well as basic and advanced NASGRO capabilities. The team taught in-person NASGRO short courses at SwRI at least two times each year through 2019. In this time frame, instructors also taught nearly 40 courses at client sites — industrial users, NASA or ESA — including 14 courses in Europe. When the COVID-19 pandemic hit, the team pivoted to a live virtual delivery method, and the training volume nearly doubled: 22 courses taught in less than three years. To date, SwRI has presented the NASGRO short course 90 times to almost 1,800 students.
In 2023, the Space Foundation inducted NASGRO into the Space Technology Hall of Fame, recognizing its broad and profound impact — the second SwRI technology recognized. Created in 1988, the Hall of Fame recognizes the life-changing technologies emerging from global space programs, increasing public awareness of the benefits of space exploration and encouraging further innovation by recognizing individuals, organizations and companies that adapt technologies originally developed for space to improve the quality of life for all humanity.
SwRI has released 20 production versions of NASGRO since 2001, with version 11.0 under development. It is the most widely used fatigue crack growth and fracture software in the world with many thousands of users. If you have flown on a commercial transport aircraft or rotorcraft in the past 20 years, then it is highly likely that NASGRO made it safer. And if you fly on an air taxi or a commercial spacecraft in the next 20 years, it is almost certain that NASGRO enabled the new technology to take flight.
Questions about NASGRO? Go to the NASGRO website, listen to the “Fracture Control with NASGRO” podcast, or contact Craig McClung at +1 210 522 2422 or Joe Cardinal at +1 210 522 3323.