In 2002, Dr. Michael Grieves of the National Institute for Standards and Technology (NIST) introduced the “digital twin” concept to describe a numerical representation of a physical object or system. NASA developed the first practical definition of a digital twin in an attempt to improve physical-model simulation of spacecraft in 2010. Since then, digital twin technology has emerged as a disruptive and exciting new approach to traditional engineering practices.
Digital twins are not just facsimiles of their physical counterparts in terms of their geometry or function. Digital twins are immersive virtual models driven by both data and algorithms, which give decision-makers in the physical world access to the nearly infinite exploratory space of the digital world. Advances in digital twin technology follow multiple innovations in engineering coalescing with an exponential boom in modern technologies. These innovations — including smart sensors, machine learning, high-throughput computing, data analytics and advanced simulation capabilities — enable digital twins to dynamically link the digital and physical world. The technology can be used to understand the past with historical data, the present with real-time data and the future with simulations. While testing in the physical world is limited by time, cost, material availability, testing feasibility, etc., digital models are limited only by the data available and computing resources. And smart-sensor technology and other innovative methods are steadily improving data collection while computing power and efficiency continue their exponential growth. Digital twin technology has helped drive the latest phase of the Industrial Revolution, referred to as Industry 4.0.
An exciting and promising application uses digital twin concepts to develop detailed, high-fidelity, physics-based digital twins of the human body. Using a digital representation of a human body, engineers can simulate how the body responds to highly dangerous situations that would be impossible to replicate with live subjects. For example, the technology could characterize how a body would physically respond when faced with a potentially dangerous situation, such as a car crash or pilot ejection from an aircraft. With valid simulations of the physical response of the human body, designers and engineers can improve systems to reduce injuries.
Southwest Research Institute has been developing and applying advanced, high-fidelity digital models of the human body for over 30 years to better understand the risk of injury under extreme conditions, design medical devices and understand how musculoskeletal diseases develop and progress. These digital twins uncover mechanical signals that drive biological tissue adaptation, allowing engineers to optimize protective equipment and safety systems and inform medical advances to ultimately optimize the performance of the human system.
HUMAN DIGITAL TWIN
The human body is a highly complex, sophisticated system. In some respects, it is a typical engineering structure required to resist external loads without failure and protect vital internal organs. This viewpoint allows engineers to apply standard, mature, engineering modeling and simulation techniques to understand how the structure will respond to external and internal forces. Early applications of human body modeling and simulation used medical images such as CT or MRI scans from a single individual selected to represent an average individual for the population. SwRI and other researchers around the country and the world have used these models with great success in applications ranging from predicting injury in a car crash to designing joint replacements to understanding cardiovascular disease development. While these early models and applications were highly successful, they represent how a single, average individual may respond and do not account for considerable variability within and between populations. Every human is unique, and differences in anatomical size and shape can have a substantial effect on how the body responds to an external load.
In addition, biological materials making up anatomical structures are highly complex and vary between individuals. For example, bones are externally rigid, fluid-filled composite materials that have different physical properties when measured in different directions. Their shape and density change based on loading. The soft tissues that connect skeletal tissues are fluid-filled composite polymers exhibiting a range of properties. Furthermore, the shapes of human anatomical structures are highly complex and cannot be accurately described using traditional design and analysis concepts, such as straight lines, analytical curvatures, and so on. Finally, no two human bodies are the same. From the overall size and shape down to the mechanical behavior of individual tissues, a tremendous amount of variability exists between individuals and within groups, for example, males and females. To complicate things further, the human system changes and adapts over time in response to external forces, disease and aging.
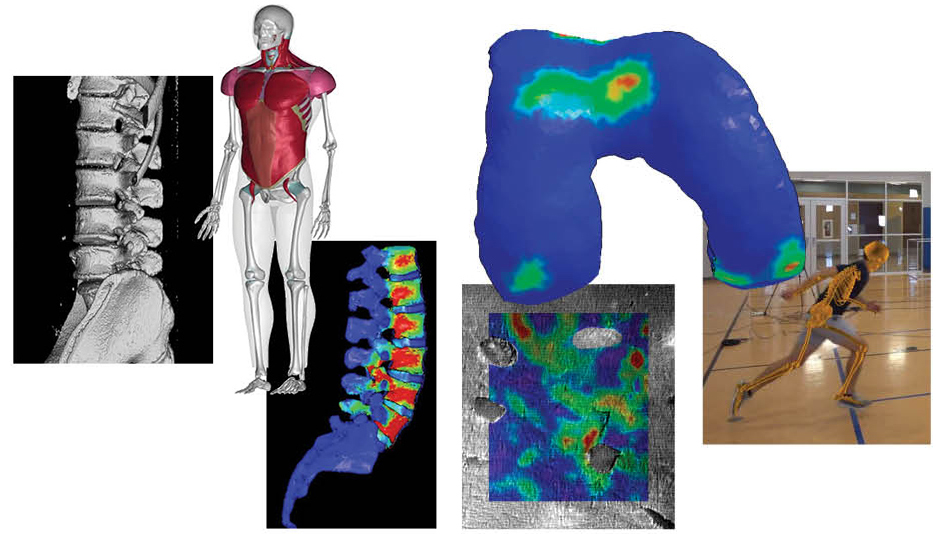
SwRI has developed a suite of advanced modeling and simulation techniques for human digital twins. Advanced uncertainty quantification methods address the variability and uncertainty in biological tissue mechanical properties and responses. Additional techniques efficiently describe the diversity in anatomical structures by parameters such as size, shape and material variation within a group. This variability is directly quantified from medical image databases representing real population-level variability.
To address these challenges, the Institute has developed, adopted and implemented a suite of advanced modeling and simulation techniques. First, advanced uncertainty quantification methods address the variability and uncertainty in the mechanical properties and responses of biological tissue. The technique treats important tissue properties such as the strength of bone tissue or the stiffness of a ligament as random variables, using values derived from experimental data to characterize how uncertainty and variability affect model predictions, such as injury risk. When the properties of a specific biological tissue such as bone are fairly well characterized, engineers calculate how the variability affects model predictions to help design robust safety systems for the target population. When physical properties of biological tissues or structures are not well enough understood for accurate model predictions, SwRI determines how sensitive our model predictions, say for risk of injury, are to this uncertainty. This sensitivity information is used to better direct resources to improve the understanding of the tissues that most significantly affect model predictions.
Second, advanced techniques efficiently describe the diversity in anatomical structures by parameters such as size, shape and material variation within a group. This variability is directly quantified from medical image databases representing real population-level differences. Treating parameters in human anatomy as random variables better characterizes how morphological differences affect predictions. Using this technique, SwRI designs systems to robustly protect diverse populations from injury rather than protecting the average individual. Individual differences in anatomical morphology can significantly affect a person’s injury risk or chance of developing a debilitating disease. For example, the size, shape and properties of bone tissue within an individual’s femur will significantly affect their risk of fracturing their hip. Similarly, we showed that shape of the bones in the knee joint significantly affects the risk of developing arthritis. For the military, the models show how the shape of the bones in the lower leg can contribute to bone fractures associated with under-vehicle blast loading, such as those caused by improvised explosive devices or IEDs.
CYBER SOLDIER
The U.S. Navy funded the Incapacitation Prediction for Readiness in Expeditionary Domains: an Integrated Computational Tool (I-PREDICT) program to apply these techniques to create a digital twin of a warfighter. SwRI is working with Elemance LLC, the Medical College of Wisconsin, Duke University and the University of Virginia to develop, verify and validate a computational human body model to predict the risk of injury and functional degradation associated with battleground experiences. The validated I-PREDICT digital twin will guide mitigation strategies for both highly dynamic and long-duration, chronic exposures, which are difficult to replicate experimentally. I‑PREDICT digital twin technology will facilitate human-in-the-loop design and analysis to develop protective equipment that balances warfighter functionality with mitigating the risk of traumatic and chronic injuries. The goal is to protect personnel and improve military readiness.
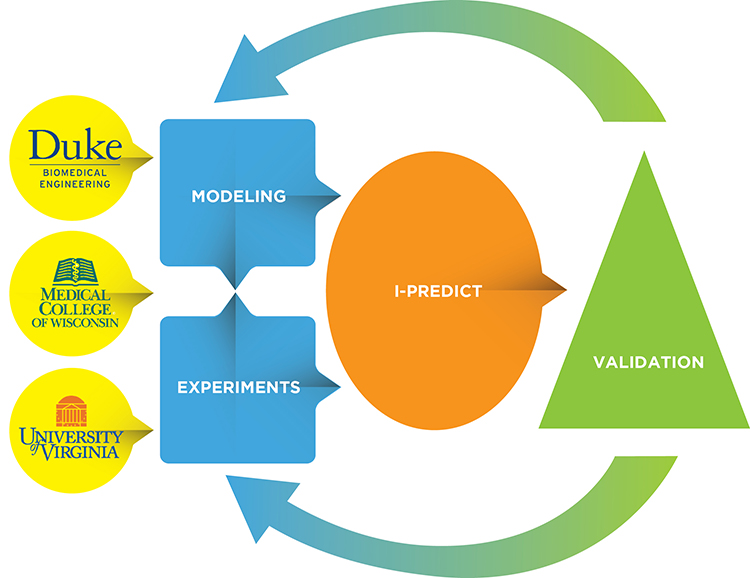
SwRI is working with Elemance LLC, the Medical College of Wisconsin, Duke University and the University of Virginia to develop, verify and validate a warfighter digital twin to predict the risk of injury and functional degradation associated with battleground experiences.
GETTING PERSONAL
Using digital simulations of the human body to understand its response to extreme conditions has contributed to significant advances in the design and virtual testing of military technology. However, another real benefit can be realized by developing a personalized human digital twin for an individual. Because each individual is different, each body may respond differently to similar conditions. Also, other factors such as exercise, nutrition, previous injury, rest and recovery are specific to each individual and can affect performance. SwRI is developing methods to efficiently create subject-specific, high-fidelity computational models of individuals.
The method uses artificial intelligence to integrate a 3D mesh of the outer skin layer with the detailed skeletal data from a single digital photograph of an individual. Then SwRI morphs the full body computational model to match the 3D size and shape of the individual. This personalizes both the exterior and interior of the computational model, transforming the model to match an individual. Using this method, SwRI can rapidly construct a personalized, high-fidelity human body model from simple digital photographs of an individual. Engineers can then use these personalized models to better understand how an individual will respond to potentially hazardous conditions. These individualized models can be used to create personalized designs for equipment such as helmets, body armor and boots and inform adjustments to or configurations for safety equipment such as aircraft ejection seats, etc.
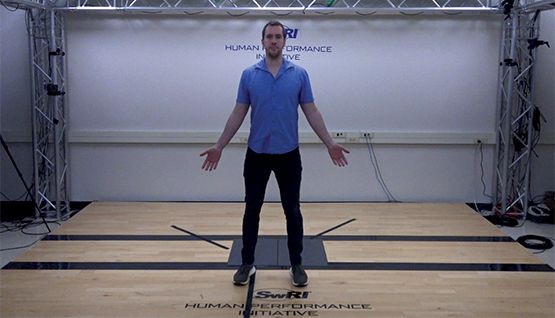
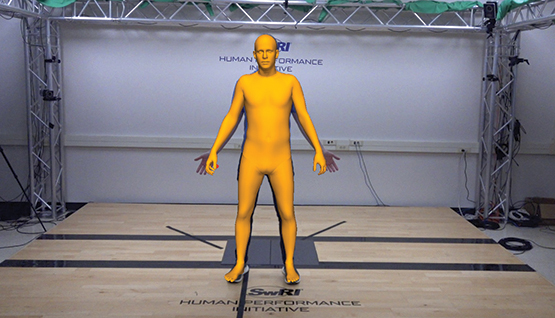
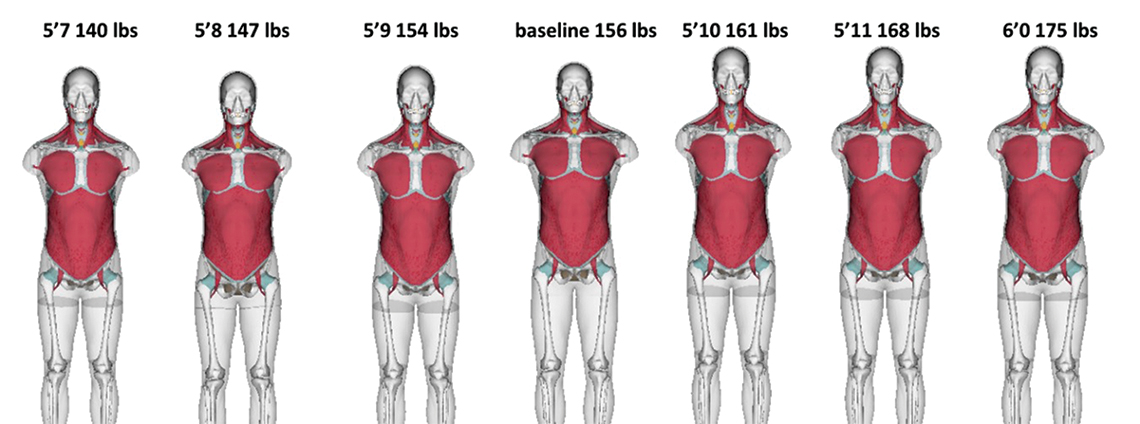
SwRI and its collaborators are developing methods to efficiently create subject-specific, high-fidelity computational models of individuals. The model uses artificial intelligence to integrate a 3D mesh of the outer skin layer with the detailed skeletal data from a digital photograph. Using the I-PREDICT full body computational model to match the 3D size and shape of the individual, the team personalizes both the exterior and interior of the model to match the individual.
PITCH PERFECT
DETAILS
One aspect of biomechanics is the study of how the human musculoskeletal system generates forces and torques to produce movement.
Human performance optimization is an exciting application for personalized human digital twins. Given a physics-driven, accurate digital replication of an individual, SwRI is using digital human modeling to explore how an individual can optimize their performance on a given task or activity. This virtual replica can be used in nearly endless applications, from improving gait mechanics for reducing the risk of developing knee arthritis, optimizing ergonomics, minimizing overuse injuries for factory or warehouse employees, altering movements and improving athletic performance.
To investigate this application, SwRI developed a physics-driven digital twin of a baseball pitcher. Baseball is one of the most popular sports in the United States, with over 15 million participants each year. Every play in baseball starts with a high-velocity pitch, associated with strenuous movements of a pitcher’s shoulder and elbow. Elbow injuries in youth baseball pitchers are rising, with 30% of youth and high school players reporting pain in their throwing arm each year. Poor pitching mechanics are thought to be a major factor in these upper extremity injuries. Every pitcher will deliver a pitch differently due to differences in body size, shape, muscle strength and individual mechanics, so solutions that might be optimal for one pitcher could create problems for another.
SwRI has set out to investigate how an individual’s personalized pitching mechanics can be optimized to maintain pitch speed while decreasing the likelihood of injury. Engineers created a personalized digital twin of a pitcher and replicated that specific pitcher’s throwing mechanics, modeling torque activation in the joints. To reduce the risk of shoulder injury, the team developed a numerical approach to assess the pitching motion and recommend changes to minimize torque in the throwing shoulder while maintaining pitch velocity. By slightly altering pitch mechanics, the pitcher could reduce shoulder torque by up to 30% while maintaining pitch velocity to within 2%. Importantly, the changes to the pitching mechanics were realistic and made movements similar to those of high-performing major league pitchers.
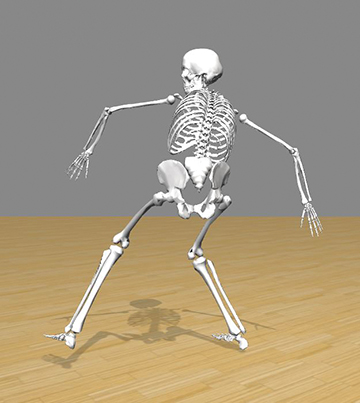
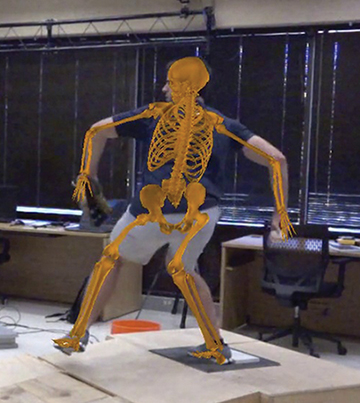
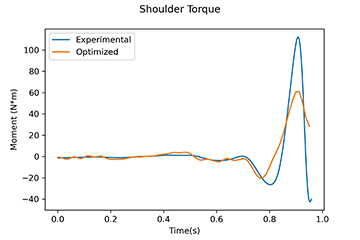
Using personalized digital twin technology, SwRI assessed pitching mechanics to minimize torque in the throwing shoulder while maintaining pitch speed. Based on the models, slightly altered pitch mechanics could reduce shoulder torque by 30% with minimal impact on pitch speed.
FUTURE DIRECTIONS
The digital twins concept originally conceived by Grieves has progressed to permitting the efficient creation of a virtual representation of a specific individual based on medical imaging and baseline data collected during medical examinations. The digital twin can be updated periodically from medical exams or in real time from wearable devices that monitor everything from heart rate to body temperature, glucose levels, physical activity and detailed individual biomechanical movement. Using personalized digital twins throughout a person’s lifetime can extend careers by optimizing performance, anticipating disease and injury, recommending treatment strategies and customizing safety systems. This technology represents the future of human performance optimization and holds tremendous promise for improving the quality of lives, reducing injury and disability in all age groups.
Questions about this story or Biomechanics & Human Performance? Contact Dan Nicolella or call +1 210 522 3222.
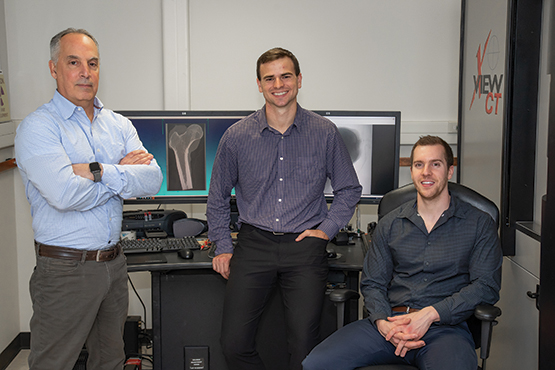
ABOUT THE AUTHORS
From left, Dr. Dan Nicolella has over 30 years of experience in basic and applied research in musculoskeletal biomechanics and bioengineering. His diverse experience includes human performance initiatives, bone mechanics, computational mechanics, human body modeling and advanced materials characterization. Ty Templin uses biomechanics and musculoskeletal modeling and simulation to create dynamic models of the human body, including a physics-driven digital twin of a baseball pitcher. Dr. Lance Frazer is a senior research engineer with eight years of experience in basic and applied research in computational biomechanics with an emphasis on finite element modeling and machine learning.
The I-PREDICT program is funded by the Office of Naval Research (ONR) and U.S. Army Medical Research and Development Command (USAMRDC) through the Medical Technology Enterprise Consortium (MTEC). USAMRDC and MTEC produce medical solutions for the battlefield to protect, treat and optimize the health and performance of U.S. military personnel and civilians. The views expressed in this article are those of the authors and may not reflect the official policy or position of the Department of the Navy, Army, Department of Defense or the U.S. government.