Powerful, desk-sized 10 MWe turbine operates at 1,300 F to improve power production
Steam turbines, invented by Sir Charles Parsons in 1884, currently generate about 80% of the world’s commercial electric power. Heat, typically produced by burning fossil fuels, turns water into steam, which spins turbine blades to convert energy into rotation. A generator then transforms that rotation into electricity.
Replacing steam with supercritical carbon dioxide (sCO2) as the working medium could revolutionize the power generation industry. Carbon dioxide typically behaves as a gas at ambient temperatures and pressures, or as a solid — dry ice — when frozen. Increasing the temperature and pressure to a supercritical point (above 73.9 bar, or 1,071 psi) for carbon dioxide creates fluid properties somewhere between a gas and a liquid.
The economic and environmental benefits of sCO2 power plants would include higher efficiency, reduced fuel consumption and lower emissions. Additionally, the compact design and small footprint of sCO2 technology would lower capital costs and decrease cooling water consumption.
HOT NEW TURBINE
A team of Southwest Research Institute and General Electric (GE) engineers designed, built and tested the highest temperature sCO2 turbine in the world. The turbine was developed with $6.8 million from the U.S. Department of Energy (DOE) Solar Energy Technologies Office (SETO) and $3 million from commercial collaborators.* The DOE’s Advanced Research Projects Agency – Energy (ARPA–E) Full-spectrum Optimized Conversion and Utilization of Sunlight (FOCUS) program provided additional financial support to validate advanced thermal seals for the device.
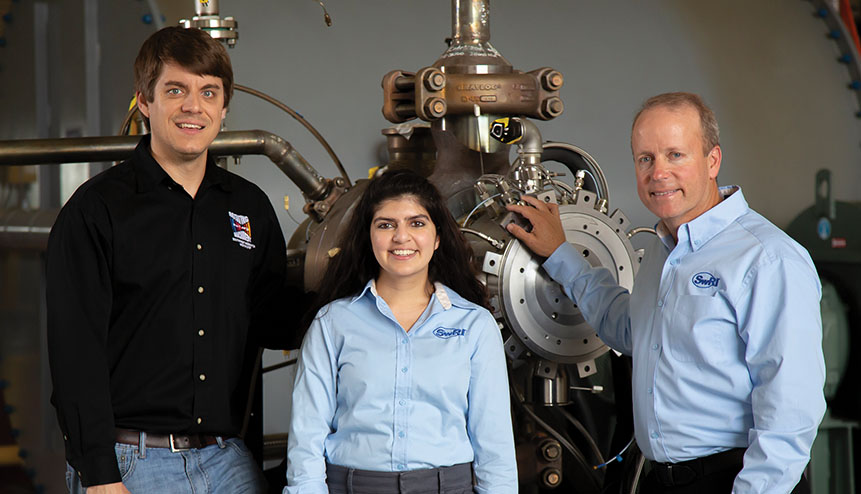
ABOUT THE AUTHORS
Dr. Jeff Moore (right) is an Institute engineer who specializes in high-speed rotating equipment. He led the team that developed the supercritical carbon dioxide turbine. Senior Research Engineer Stefan Cich (left) led the mechanical design, analyzing the stresses, flow and dynamics of rotating equipment. Research Engineer Meera Day Towler specializes in data acquisition systems, instrumentation and control systems to evaluate turbomachinery.
The new 10 megawatt electric (MWe) turbine is the size of a desk and yields the highest power density of any industrial turbine, rivaled only by the turbopumps used in space shuttle engines. This small powerful turbine was designed specifically to withstand the tough operating conditions associated with concentrated solar power (CSP) plants. However, sCO2 technology is heat agnostic, and could potentially improve the efficiency of fossil fuel, solar and nuclear power plants. The technology also lowers the cost of waste heat recovery and energy storage and is highly scalable. Engineers envision use in a 300 MWe utility plant. It could result in a 2–4% efficiency increase for fossil fuel plants over current state-of-the-art steam plants while reducing CO2 emissions by the equivalent of 14 million cars.
Achieving the conditions needed for sCO2-based systems required the project team to overcome significant engineering challenges for operating under high-temperature, high-pressure conditions. Over the past five years, the SwRI team worked with its collaborators and SETO to create a multi-stage axial flow sCO2 hot gas turboexpander. GE Research contributed significantly to the turbine’s design, especially in the turbine’s rotor.
TURBINE FEATURES
The turbine has a four-stage rotor assembly. A rotor is a shaft or drum with blades attached. As moving fluid acts on the blades, they spin and impart rotational energy that a generator converts into electricity. Axial flow turbines use multiple stages or blade wheels to expand the working fluid. These turbines offer high efficiency and large mass flow rate, particularly for their size and cross-section.
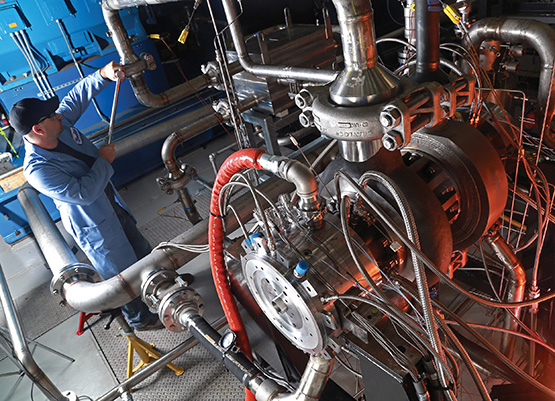
An SwRI-led team of engineers created this 15-megawatt (10 MWe) supercritical carbon dioxide turbine that can increase efficiency and lower the cost of power generation for solar power plants.
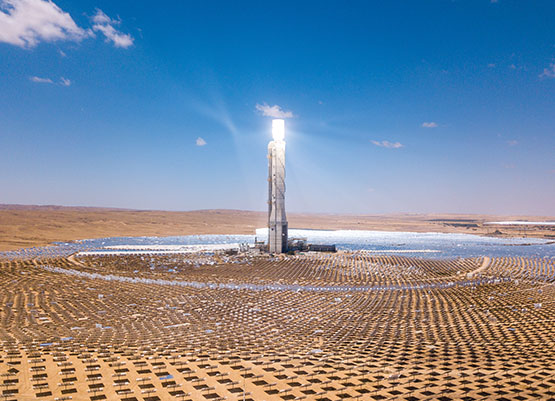
Concentrated solar power systems generate power by using mirrors or lenses to concentrate a large area of sunlight into a small area. The concentrated light is converted to heat, typically heating water into steam that drives a turbine connected to an electric power generator.
The new turbine expands high-pressure sCO2 gas to produce enough power to drive the compressor and generator that create electricity in CSP plants. These turbo-expanders must operate at temperatures greater than 1,300 degrees Fahrenheit and pressures over 3,600 pounds per square inch (psi) under a wide range of load conditions. They must also maintain high efficiency, a fast start-up time and the ability to handle rapid swings in transient heat input.
The turbine features dual inlets and exhausts to accommodate large gas flow in a small package. Its four stages extract energy from the high-temperature (715 C or 1,320 F) flow, while decreasing the pressure from 250 bar (3,600 psi) to 80 bar (1,200 psi) at the exhaust stage. The full-flow turbine will generate 15 MW (20,000 horsepower) gross power, or 10 MW of net electric power after subtracting the compressor power, while running at 27,000 revolutions per minute (rpm). Considering the rotor weighs less than 82 kg (180 pounds), this turbine has the highest power density — horsepower to pound — of any industrial turbine, second only to rocket engine turbopumps.
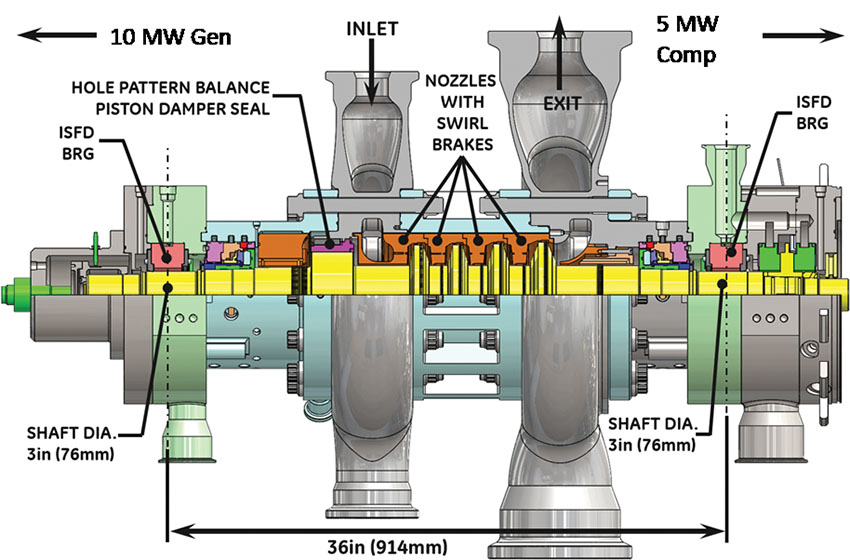
SwRI developed this 10 MWe sCO2 four-stage axial flow turbine under DOE’s Sunshot Program in collaboration with General Electric. The turbine generates 15 MW gross power at inlet conditions of 715 degrees C and 250 bar.
SwRI fabricated and machined the turbine’s high-temperature, high-pressure casing out of nickel-chromium-based superalloys. These oxidation- and corrosion-resistant materials with high creep strength are ideal for extreme environments. Using an advanced five-axis electrode discharge machining (EDM) process, the team manufactured the rotor from one piece of a high-temperature, oxidation-resistant nickel-based alloy. Engineers developed thermal seals at each end to reduce temperatures and protect the mechanical seals designed to minimize atmospheric leaks.
Most conventional CSP systems operate at a thermal efficiency of 30–40%. The newly designed turbine with the sCO2 power cycle can approach 50% efficiency. With more efficient and cost-effective power, the new turbine makes CSP plants more economically competitive with fossil fuel power plants.
ROTORDYNAMIC CHALLENGES
Rotating machinery produces vibrations during operation. Because this turbine operates in such extreme conditions (high speed, vibration and temperature), engineers designed the components to minimize imbalance and manage the fluid dynamic forces acting on the rotor. This reduces the risk of catastrophic failures and improves reliability, targeting a 20-year operating life.
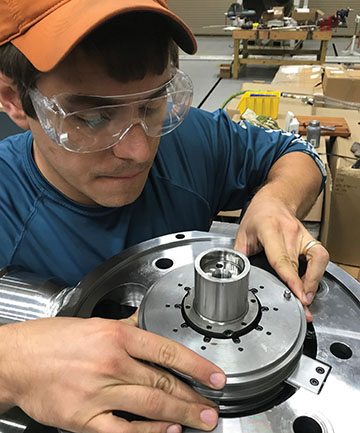
SwRI engineers assembled the thrust bearings on the 10 MWe sCO2 turbine. The radial tilting-pad bearings are outfitted with dampers to improve rotordynamics.
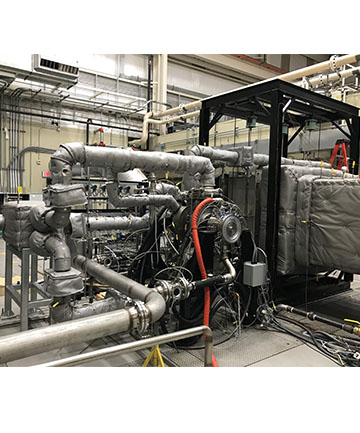
This test fixture constructed in SwRI’s Turbomachinery Research Facility incorporates a high-temperature natural gas-fired heater, a recuperator to capture exhaust heat and ancillary equipment such as mechanical seals and bearings.
Engineers designed the turbine bearings to utilize squeeze film dampers to improve the turbine’s rotordynamic response. These films between the bearing and the housing soften the bearing support and increase damping effectiveness. Other advanced features implemented include swirl brakes and hole pattern damper seals, components that improve rotordynamic stability at extreme conditions.
TURBINE TESTING
The Institute’s custom-built, high-pressure sCO2 1-MWe test loop’s size represents a compromise between capability and cost. The turbine internal flow path was reduced to match the test loop but provided nearly identical pressure and temperature distributions through the turbine. SwRI and its collaborators also designed the primary heater. Fabricated by an outside commercial entity, it is built from the highest-temperature-resistant piping available.

Engineers tested two different thermal seals. Both exhibited a linear temperature gradient at each end of the turbine to minimize thermal stress in the casing and rotor.
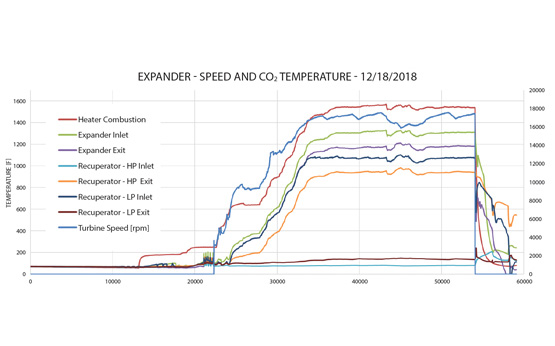
SwRI performed a six-hour endurance test at the maximum temperature of 715° C. The turbine accommodated a rapid transient shutdown at the conclusion of the test.
In this facility, engineers put the turbine through a rigorous series of tests, varying speed, temperature and pressure. The turbine met all mechanical and performance objectives, hitting maximum targets of 27,000 rpm, 715 C and 250 bar. The rotor experienced low vibrations throughout the test and demonstrated good stability under the full range of operating conditions.
APPLICATION
A full 10 MWe version of the turbine will be incorporated into the Supercritical Transformational Electric Power (STEP) 10 MW demonstration plant, a $119 million sCO2 pilot plant currently under construction at the Institute. Developed through a collaborative effort among Gas Technology Institute, SwRI and GE and funded by DOE’s National Energy Technology Laboratory, STEP will demonstrate a fully integrated sCO2 power plant that generates power at higher efficiency and lower costs with a smaller carbon footprint than conventional plants.
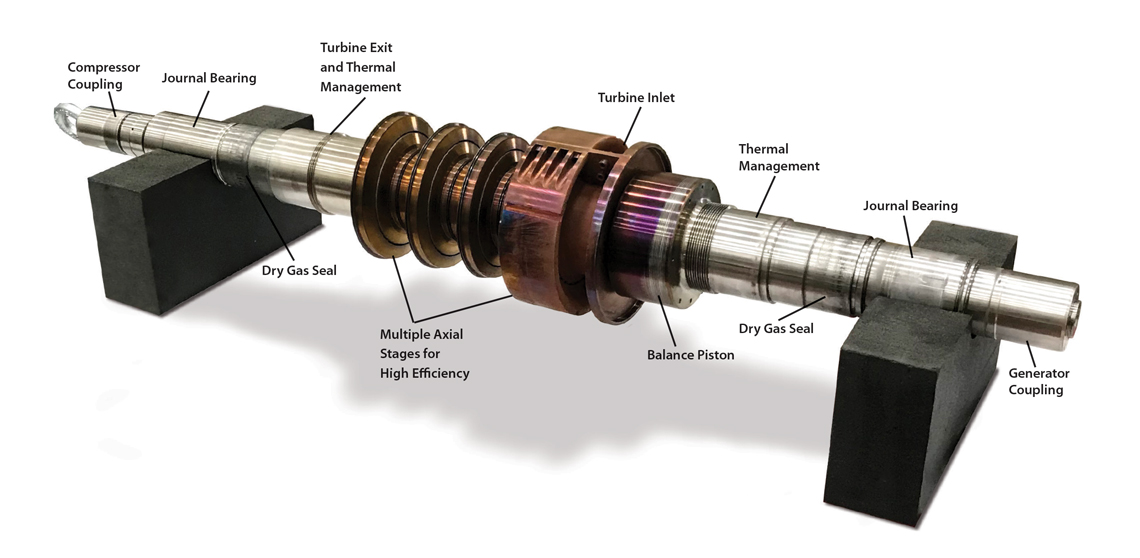
The new 10 megawatt electric (MWe) turbine is the size of a desk and yields the highest power density of any industrial turbine, rivaled only by the turbopumps used in space shuttle engines. The turbine’s four-stage rotor design was machined from a single piece of high-performance nickel alloy.
SwRI broke ground on the project in October 2018, with construction set to begin in early 2019 and a completion goal set for April 2020. STEP technology, including the high-temperature turbine, could revolutionize the power generation industry, providing economic and environmental benefits including higher efficiency, reduced fuel consumption and lower emissions. In addition, the small footprint of sCO2 technology would lower capital costs and decrease cooling water consumption.
Future turbine concepts under development are incorporating direct-fired oxy-fuel combustors that can burn natural gas with oxygen, allowing much higher turbine temperatures and producing CO2 and water as its only by-products. Because combustion is performed at elevated pressures, the CO2 can be easily captured to create a true emission-free power source with efficiencies that rival the current state of the art with no carbon capture.
What this all means is that the same gas largely blamed for Earth’s climate change may be the one that prevents it.
For more information, visit Supercritical Carbon Dioxide Power Systems.
Questions about this article? Contact Jeff Moore or call +1 210 522 5812.