Concerns over climate change and urban air quality have led regulators and governments to strongly encourage the use of electric-powered vehicles. The governor of California, for example, issued an executive order in September setting new statewide goals to prioritize clean transportation solutions that include having 100% of in-state sales of new passenger cars and trucks be zero-emission vehicles (ZEVs) by 2035. The order also aims, where feasible, to have 100% of medium- and heavy-duty vehicles be zero-emission by 2045 and for off-road vehicles and equipment to transition to 100% zero-emission by 2035. The governor charged the California Air Resources Board (CARB) and other state agencies to develop regulations or take other steps to achieve these goals. To facilitate the transition, state agencies are working with the private sector to develop affordable fueling and charging options. California is the largest automotive market in the U.S., and 14 other states and the District of Columbia follow its lead concerning emissions rules.
More recently, General Motors made a commitment to zero-emission vehicles by 2035, a move that will influence heavy-duty (HD) truck manufacturers and suppliers. Daimler Trucks, Volvo Cars, Ford Motor Company and Volkswagen AD have also signed on to making California’s goals a reality. The U.S. Environmental Protection Agency and other federal entities will face pressure to take similar measures, particularly as the rapid acceleration of the battery electric vehicle (BEV) market slowed in 2019.
DETAIL
According to the McKinsey Electric Vehicle Index, worldwide electric vehicle (EV) sales rose 65% from 2017 to 2018. But the number of units sold in 2019 rose by just 9% and declined by 25% during the first quarter of 2020.
The California order does not mandate the use of BEVs — fuel cells running on hydrogen are also an option — nor does it prohibit the import or resale of gasoline-powered vehicles. The end result, however, will almost surely be a significant increase in the number of BEVs on the roads. With this order, California joins 15 countries that have committed to accelerating the adoption of BEVs by banning or restricting the sale of internal combustion engines.
Electric powertrains offer several operational advantages over traditional powertrains, but they also present several unique challenges, notably a steep sticker price and what’s known as range anxiety — concern that an EV will run out of power before reaching its destination or a suitable charging point. Southwest Research Institute has been involved with vehicle electrification research and development since 1990 in light-duty, heavy-duty, on-road and off-road markets. We have the experience and technical expertise to assist our customers in addressing their needs for electric powertrains, including testing, research, modeling and analytical services. We also offer abuse, performance and durability evaluations on battery cells, modules and packs and other EV components — expertise that is even more critical as the BEV market expands.
ABOUT THE AUTHORS
From right, Dr. Terry Alger is the director of SwRI’s Automotive Propulsion Systems Department, a Fellow of the Society of Automotive Engineers and a consultant to the Army Science Board. His work at SwRI focuses on improving engine efficiency and emissions through in-cylinder combustion processes, advanced engine technologies and vehicle electrification. Dr. Bapi Surampudi specializes in energy storage system and powertrain research. He has developed control systems for diesel engines, transmissions, electric-hybrid powertrains, electric vehicles and automated vehicles. Ian Smith manages SwRI’s Electrified Powertrain Section and the Electrified Vehicle and Energy Storage Evaluation (EVESE) Consortium. This multiclient program focuses on EV benchmarking and testing to understand performance, efficiency and powertrain control strategies.
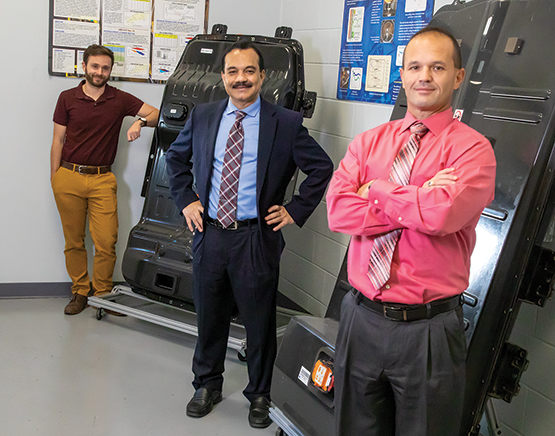
Advantages
BEV performance is often superior to conventional vehicles. The torque characteristics of electric motors can provide superior acceleration compared to internal combustion engines, and BEVs are not a mobile source of pollution. While these vehicles are not truly emissions-free — the electricity that runs them has to come from somewhere and renewable sources are not plentiful enough to power the U.S. transportation market — their use in cities would exchange tailpipe pollution in congested urban areas for powerplant emissions located in less populous regions, where it may be less harmful. Finally, for typical urban families, BEVs may be more energy-efficient than conventional vehicles, even factoring in the production and transmission of the electric energy that powers the car. Given these seeming advantages over conventional vehicles, why has the market penetration rate of BEVs been so slow and even recently stalled?
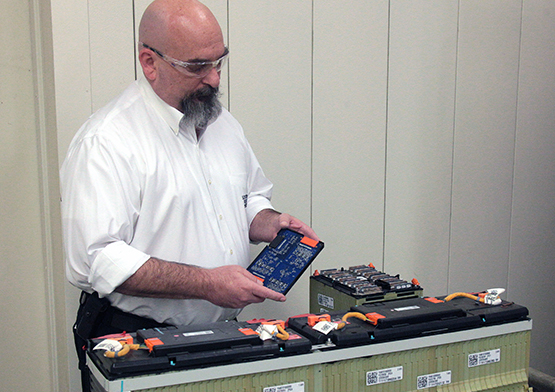
Assistant Manager Mickey Argo oversees SwRI’s Energy Storage Technology Center testing facilities, including manufacturing, characterization, life and abuse tests on lithium-ion cells and battery packs.
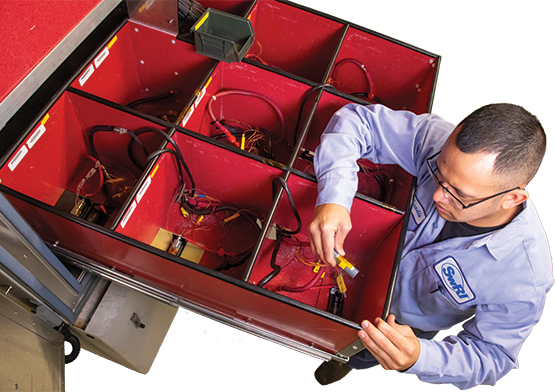
Technician Arcadio Maldonado prepares lithium-ion battery cells for thermal cycling. Thermal management plays an important role in battery charge and discharge events.
Challenges
Electric vehicles still have significant challenges to overcome. First, and most importantly, is their cost. Lithium-ion batteries are considered the energy storage solution of the future, particularly for electromobility. They store large amounts of energy but are comparatively light and compact. While lithium is the 25th most common element, making up 0.002% of the Earth’s crust, commercially viable concentrations are relatively rare. The other battery cathode materials — cobalt, manganese and nickel — are also expensive commodities. While increased manufacturing volumes and improved battery chemistries are bringing costs down, most BEVs are still significantly more expensive than comparable internal combustion engine cars. A considerable amount of research and development from commercial organizations and the U.S. government is aimed at decreasing the rare materials BEVs require. The goal is to reduce the cost of a battery pack, in terms of dollars per kilowatt (kW) hours, to the cost of an internal combustion engine by 2025.
Then there are the range restrictions associated with the limited energy density of a battery compared to a liquid fuel, combined with the time it takes to charge it versus filling a tank with gas. A combination of improved battery chemistries, better thermal management systems, more effective battery management systems and safer large battery packs has increased the range for many BEVs. However, the relatively long time it takes to charge the vehicle, combined with the potential erosion of battery life if it is repeatedly charged too quickly, means that improving fast charging battery packs can go a long way to making BEVs a more attractive option for consumers.
EV BATTERIES
Today’s BEVs are powered by lithium-ion battery packs, multiple cells with housing, electrical connections and, increasingly, control electronics. The battery packs charge and discharge through electrochemistry. In a battery cell, lithium ions move one way as the battery charges, absorbing power, and move in the opposite direction when the battery discharges, when it’s supplying power.
During charging, lithium ions flow from a positive cathode, usually a cobaltoxide material, to a carbon-based negative anode through an electrolyte fluid. Electrons also flow from the positive electrode to the negative electrode but take a longer path around an outer “circuit.” The electrons and ions combine at the negative electrode and deposit lithium there. When no more ions will flow, the battery is fully charged.
During use, the ions flow back through the electrolyte from the anode to the cathode and electrons flow through the outer circuit, creating an electric current to power the vehicle. When the ions and electrons combine at the positive electrode, lithium is deposited there. When all the ions have moved back, the battery must be recharged.
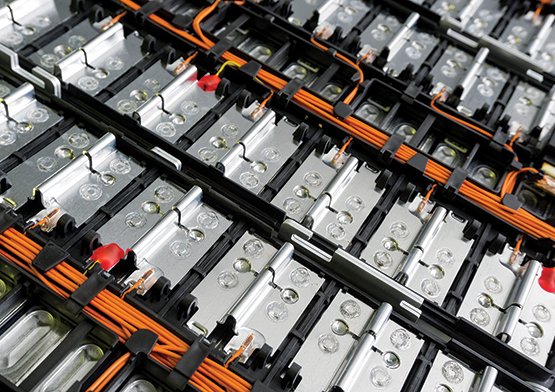
Lithium-ion battery packs are the energy storage solution of choice for electromobility
Fast Charging Phenomena
A battery’s charge rate is often referred to as the “C rate,” which measures the battery charge/discharge rates relative to its capacity, where C is the rate it takes to fully charge, or discharge, a battery in one hour. For example, a 2C rated battery will go from 0% state-of-charge (SOC) to 100% SOC in 30 minutes. To achieve an equivalent charge time to that of refueling a fossil-fueled vehicle, a battery must be charged at 12C or higher to match the five minutes it typically takes to fill a standard automotive gas tank. While this is the optimal scenario, most current efforts are targeting a 10–15-minute recharge time, or a 4–6C rate. However, achieving high C rates presents a series of unique challenges to both the battery and the infrastructure needed to support it.
DETAIL
In 2011, SwRI launched the Energy Storage System Evaluation and Safety (EssEs) multiclient consortium to help the EV industry develop precompetitive, detailed cell-level test data on electrochemical storage systems and to advance the methodologies to evaluate batteries. In 2020, SwRI began a new phase of the consortium, renamed the Electrified Vehicle and Energy Storage Evaluation (EVESE) consortium, to better reflect the focus on electric mobility.
Fast charging battery packs will require a considerable infrastructure investment. For instance, charging a Chevrolet Bolt battery pack in 12 minutes would require 330 kilowatts of electric power or 66 kWh of energy. This would require an average current of 94 amperes (amps), which presents some safety and other concerns. Consider, most homes in the U.S. are wired with a combination of 15-amp and 20-amp, 120-volt circuits with some high-current lines such as 220-volt dryer or electric stove lines. Even the highest current lines only handle 30–50 amps. Today’s fastest charging battery stations are located in places such as shopping malls that have the power infrastructure to handle it. As BEVs become more prevalent, public and private sector entities are working diligently to ensure that more stations providing quick recharging are available and that this inherently more dangerous high-voltage power can be delivered safely to electric vehicles.
The greatest challenge with quickly charging BEVs is the damage that fast charging does to the battery itself. Using current technologies, repeatedly fast charging a battery pack significantly degrades the performance and life of the battery. Charging a battery is a very exothermic or heat-releasing event, which increases the overall temperature of the battery pack. Charging or discharging a battery at elevated temperatures not only degrades its performance but also has the potential to decrease its lifespan and, in some extreme circumstances, can lead to catastrophic failures.
Another significant issue with fast charging a battery is lithium plating, an irreversible phenomenon caused when metallic lithium coats the surface of the anode, or negative electrode, during charging. Lithium plating occurs when the anode’s ability to absorb lithium ions is less than the lithium ion transfer rate, which is very high during a fast charging event. When ions cannot be absorbed, they coat the surface of the electrode, reducing the number of lithium ions available for power transfer and forming dendrites, spike-shaped deposits that degrade battery performance. Eventually, if the dendrites get large enough, lithium plating leads to internal short circuits and battery failure. Preventing lithium plating is a key step to enabling regular fast charging critical to widespread consumer acceptance of BEVs.
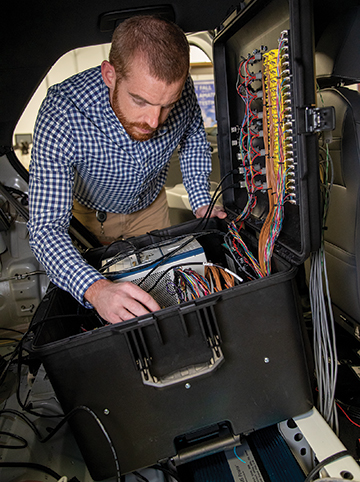
Senior Research Engineer Kevin Jones uses a mobile data acquisition system to collect battery performance data for an electric vehicle.
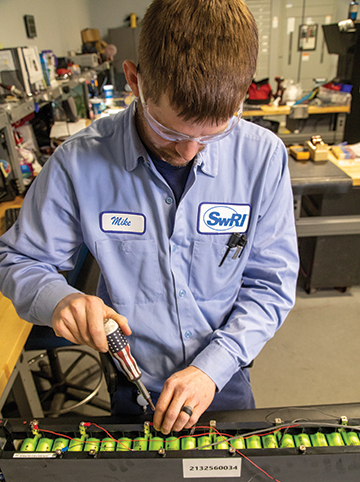
Senior Technician Mike Taylor instruments an EV battery module to collect the data needed to develop new solutions to limit battery degradation while decreasing battery recharge times.
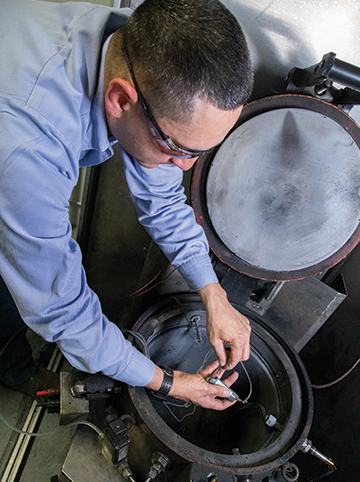
Staff Technician Mario Guillen installs a lithium-ion battery cell in a calorimeter to evaluate the thermal stability limit for battery cells and calculate heat release during failure.
Need for Speed
The team at SwRI’s Energy Storage Technology Center (ESTC) has been developing solutions for fast charging batteries for over a decade. Initial efforts focused on understanding the performance and durability of different battery chemistries under a variety of conditions — charging/ discharging rates, ambient temperatures, and so on. For the past decade, SwRI has operated a consortium that evaluates the unique chemistries and designs of batteries to understand the physical mechanisms that cause battery performance to degrade. This information allows the team to develop and tune battery models, enabling us to accurately predict battery performance under a variety of conditions with a limited test data set. More importantly, the know-how and understanding the team has built through this testing has allowed SwRI to propose new solutions to limit battery degradation while decreasing battery recharge times.
One new solution is a real-time controller that monitors lithium plating during fast-charging events and adjusts the charge current accordingly. The goal is to charge the battery at the optimal limit of its ability to intercalate or absorb the lithium ions into the anode, but no faster. This rate is changeable and inconsistent, varying with the state-of-charge of the battery and environmental conditions, so the controller must continually adjust the charging rate in real time. As part of an internally funded project, the ESTC team used a controller on a set of batteries from a modern EV. Compared to the manufacturer’s recommended fast-charging strategy, the SwRI controller resulted in a charge profile that is 30% faster with significantly reduced degradation.
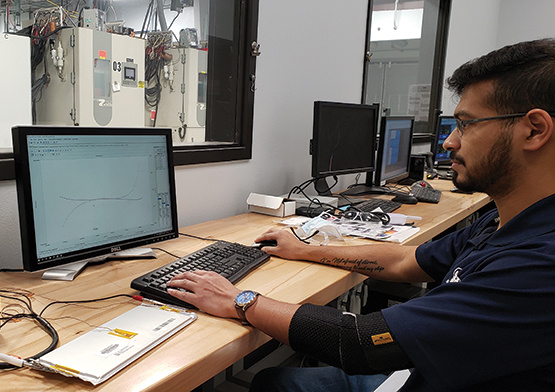
Research Engineer Shuvodeep Bhattacharjya models lithium-ion batteries to capture how voltages would change under different currents at different states of charge.
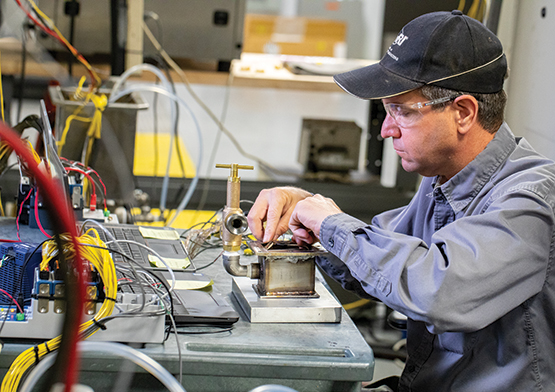
Senior Research Technologist Barrett Mangold instruments a lithium-ion battery module inside a test rig used to evaluate immersive coolants. Immersive cooling significantly improves heat transfer, allowing battery packs to be charged and discharged at higher rates while avoiding negative heat-related effects.
Cool Solutions
In addition to developing a thorough understanding of the role that battery chemistry plays in the response to environmental conditions and charging/discharging profiles, the ESTC team has studied battery thermal management. This research focuses on maintaining a constant temperature during battery charge and discharge events and developing and applying innovative coolants to improve battery performance and safety.
SwRI’s energy storage consortium benchmarked several of the latest BEVs to understand how their thermal management systems function during aggressive charging and discharging events to identify deficiencies and potential improvements. For instance, the team developed a pulsed charging/cooling strategy that exploits the unique nature of the battery chemistry to charge aggressively when cells are in an endothermic or heat-absorbing charge region and then less aggressively when cells are in an exothermic charge region. Charging faster when a battery is absorbing heat than when it is giving off heat reduces the temperature increases usually associated with fast charging. This strategy reduces charge time and battery degradation after multiple fast charging events.
Typically, BEV thermal management systems use indirect cooling systems, transferring the heat generated through conduction by setting the battery on a cooling plate. This strategy separates the electrically conductive coolant from the battery cells. The technique is superior to air cooling but can significantly increase the size, weight and complexity of the battery pack.
New immersive cooling techniques using liquids that conduct heat but not electricity in direct contact with the battery can improve thermal management. These systems conduct 50 to 100 times more heat than conventional indirect cooling solutions. With this significantly improved heat transfer, battery packs can be charged and discharged at higher C rates while avoiding negative heat-related effects. Moreover, this technology improves safety. When battery cells fail, they undergo extreme exothermic reactions that, if left unchecked, can propagate to other cells and destroy the entire battery pack. An immersed coolant system mitigates thermal propagation, reducing the likelihood of a total battery pack failure.
The next logical step for SwRI’s ESTC team is to couple the real-time lithium plating controller with an advanced, immersed coolant thermal management system to push the limits of fast charging without sacrificing battery safety, life or performance. By developing these innovative solutions to the problem of fast charging, SwRI is helping to smooth the path for the adoption of BEVs worldwide.
Questions about this article or Electric Powertrain Systems? Contact Ian Smith at +1 210 522 2041.