By Dr. Terry Alger
When most people hear “CAFE standards,” they think about the kitchen cops and health inspections for local eateries and the food they offer. At Southwest Research Institute, we think about another form of fuel, and more specifically, vehicle fuel efficiency. Corporate Average Fuel Economy — CAFE — standards set the bar for the average new vehicle fuel economy, as weighted by sales, that a manufacturer’s fleet must achieve.
Congress initially enacted CAFE standards in 1975 in response to the 1973 oil embargo that quadrupled the price of oil. Almost overnight, the cost of gasoline became a major concern among auto manufacturers and the public alike. These CAFE standards aimed to double the average fuel economy of the new car fleet to 27.5 miles per gallon by 1985. Recognizing the challenges facing heavier vehicles, the U.S. Department of Transportation set a second standard for light trucks with the same overall goal but with a 22.2 mpg target.
These standards remained fixed until the price shocks of 2007. Then economic factors, combined with growing concern about carbon dioxide emissions and the availability of oil, led to a new round of fuel economy agreements in 2009. SwRI is working with the auto industry to meet these requirements and simultaneously achieve acceptable safety, emissions and performance standards, all while keeping vehicles affordable for the average consumer.
As the transportation industry strives to improve efficiency, the electric power generation industry is also attempting to reduce CO2 emissions. And it’s working. The United States has reduced its CO2 emissions by nearly 20 percent since 2000. Most of this change is associated with the transition from coal to natural gas for power generation, although renewable energy sources and more efficient vehicles have also contributed. At SwRI, we work with both the transportation and electric power industries to improve energy storage technology.
The ESTC team includes, from left, Technician Mike Taylor, Research Engineer Kevin Jones, Assistant Manager Mickey Argo, Staff Engineer Dr. Bapi Surampudi, Senior Research Engineer Ian Smith, Manager Mark Walls, Principal Technician Mario Guillen, Staff Technician Doug Czaja and Engineer Christopher Kelly.
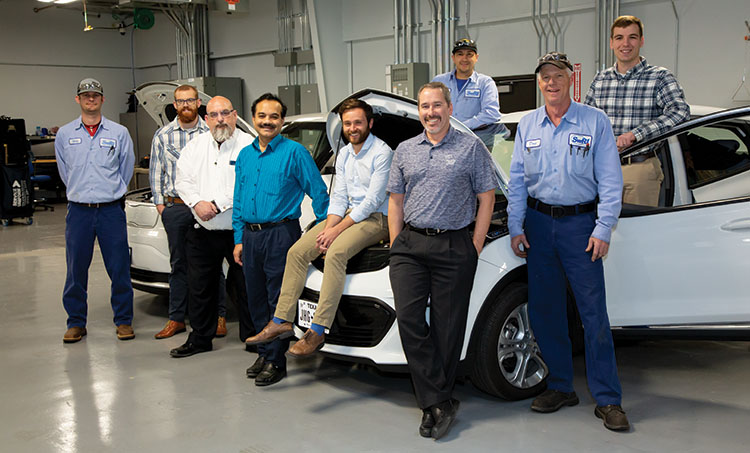
EFFICIENCY LIMITS
The fundamental efficiency of today’s automotive engines is actually quite high, which means it is difficult to make further significant improvements. Some can be made with new technologies (see “Clean and Cool” in the Summer 2010 issue of Technology Today). Other solutions involve waste heat recovery or adjusting the engine to operate more consistently in the efficiency zone. For power generation, the challenge of balancing the supply with demand can lead to inefficient operations. In both applications, adding an energy storage device — such as a battery — can significantly improve the efficiency of a system.
Batteries convert electrical energy into chemical energy for safe and efficient storage. In automobiles, braking is a huge waste of energy. For a typical car with friction brakes, the vehicle’s kinetic energy is converted into thermal energy when its brake pads rub on rotors. That thermal energy is then released as heat into the environment, so that, effectively, all the energy that went into speeding the car up is turned into wasted heat. By using an energy storage system and a generator connected to the axles, a hybrid vehicle converts kinetic energy into electrical energy during a braking event, which is stored in a battery. In this manner, some of the energy that went into accelerating the car can be recovered for use later. In addition, having an electric motor and battery that can power the vehicle allows the engine to be used more efficiently, saving fuel. Finally, batteries in plug-in hybrids can be charged when the car is not in use, supplying the vehicle with energy generated by cleaner, more efficient sources.
For the power industry, batteries can help balance the load on the grid. They are more responsive than generators to sudden demands for power and can also absorb energy for use later, depending on demand. Plus, a major challenge preventing the country from getting all the benefits from solar and wind energy is timing. Peak wind and solar production periods often occur when energy demand is low. Integrating batteries into the system allows utilities to capture the excess energy and send it to the grid later when demand might outstrip supply. And greening energy production makes electric vehicles even more attractive.
STORAGE SYNERGY
Despite their potential benefits, widespread adoption of advanced energy storage systems has been stymied by challenges in cost, reliability, safety and energy density. SwRI has spent the last two decades addressing these issues to encourage more widespread adoption of advanced storage technology.
DETAIL
SwRI manages more than a dozen multiclient projects, including seven automotive consortia, allowing organizations to pool their research and development dollars for pre-competitive research.
For the automotive sector, SwRI has worked on many different hybrid systems over the past 20-plus years. In the early 2000s, we evaluated the durability of a powertrain for a groundbreaking electric vehicle and contributed to a hydraulic hybrid system for delivery trucks. Then in 2011, SwRI launched its first major battery effort for the transportation sector, initiating the Energy Storage System Evaluation and Safety (EssEs) consortium to study and benchmark lithium-ion batteries for the emerging hybrid vehicle market.
EssEs, now in its seventh year, has tested over 40 different types of lithium-ion cells, the building blocks of battery packs in today’s hybrid and electric vehicles. The consortium also buys one electric vehicle per year, benchmarking its performance before disassembling the battery pack and benchmarking individual cells.
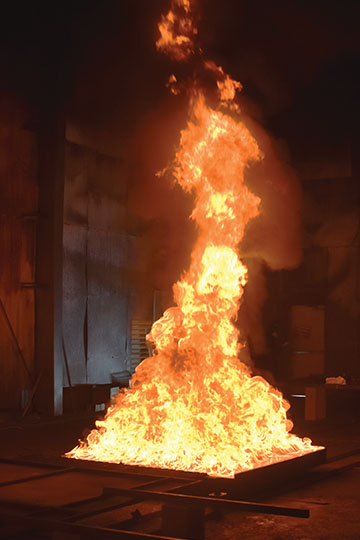
Fire specialists expose fully charged electric vehicle batteries to gasoline pool fires. Engineers monitor 60 sensors measuring temperatures up to 800 degrees C in this 2-minute test to characterize resistance to fire and explosion.
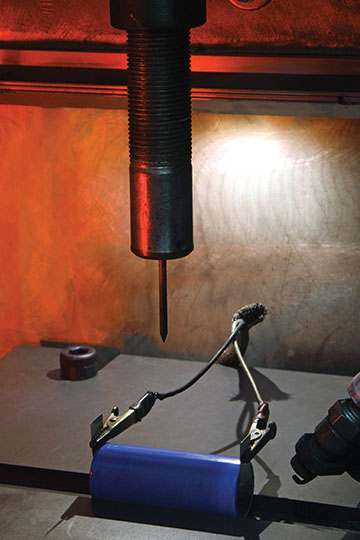
Among the battery of storage cell tests SwRI conducts is penetration testing to simulate damage from road hazards.
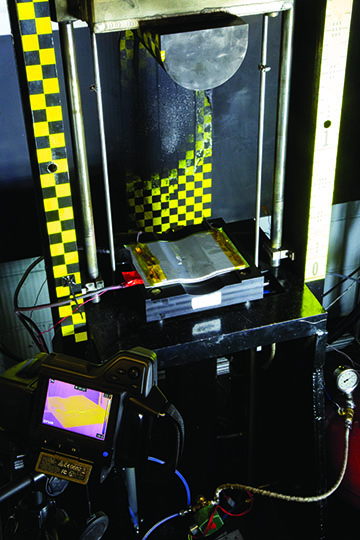
SwRI has developed a unique crush test fixture that uses sensors and video to characterize what could happen to a battery in an accident.
Our early battery test work was a grassroots effort, with SwRI repurposing engine test cells as battery test facilities. Outfitted with thermal chambers to keep the test articles at a consistent temperature, these test cells characterize batteries operating over a range of ambient temperatures. A cycler charges and discharges batteries in a prescribed manner, depending on the test.
Initially, the EssEs consortium focused on performance, life and abuse-tolerance testing of lithium-ion cells. Activities expanded beyond the consortium to include testing batteries for individual clients as a part of their product development process.
STORAGE SAFETY
As more electric vehicles took to the roads, several highly publicized accidents occurred, where batteries caught fire or exploded. To address these safety hazards, battery abuse testing became an important component of the electric vehicle product development process. Batteries in cars, cell phones and even medical devices must pass abuse tests while meeting performance requirements.
To meet these demands, the EssEs team built devices to crush, puncture and otherwise damage battery cells to characterize safety, creating a core capability to perform all required battery abuse testing to various U.S., European Union and United Nations standards.
Battery abuse testing takes several forms. The first is electrical abuse.
Although modern battery management systems are extremely robust, overcharging or overdischarging can still potentially occur. To minimize this risk, SwRI evaluates how batteries deal with these situations, charging or discharging the units at different rates until they fail or a specified testing period ends.
The second form of abuse, physical abuse, comes in many forms. Teams from across the Institute use their capabilities to accomplish the work. SwRI performs all required physical abuse tests, from crushing cells, modules and packs to drop testing and simulating crash damage. Penetration tests mimic damage from road debris, and salt fog simulates corrosive environmental conditions. Fully charged batteries are exposed to pool fires to assess resistance to fire and explosion. As battery technology has matured, abuse testing has become less dramatic. Five years ago, abuse testing almost always resulted in a fire or some kind of dramatic event. Today, those incidents rarely happen. While the team might miss the excitement, it is nice to know that as batteries have proliferated, they’ve become much, much safer.
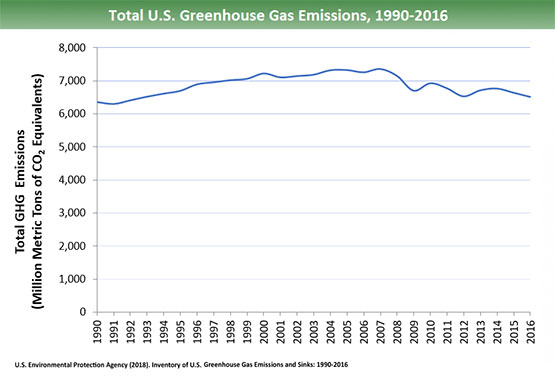
The United States has successfully reduced CO2 emissions since 2000.
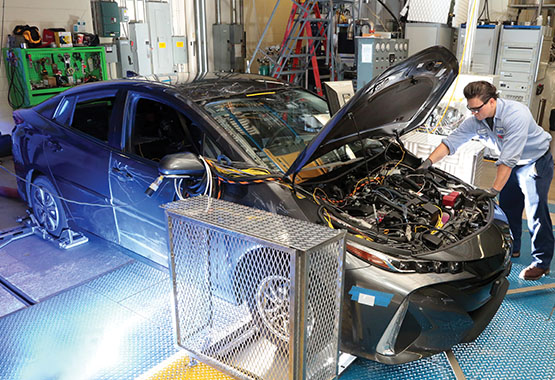
SwRI purchases one electric vehicle per year, benchmarking its performance before disassembling the battery pack and benchmarking individual cells.
STORAGE SPECS
Characterization and performance testing round out our battery test work. SwRI evaluates manufacturers’ ability to make consistent cells for both the EssEs consortium and individual clients. Size, weight and electrical properties are measured for a statistically representative sample of cells to evaluate the production quality of different cell types. Once characterized, we test cells under standard and custom charge and discharge cycles to measure their response to changes in temperature, charge/discharge rate and starting energy levels. As a part of this testing, a subset of cells are aged and tested at intervals to establish the response of the cell. It is common knowledge in the industry that batteries function differently as they get older, so an important part of our work is establishing how aging affects different cell chemistries.
ELECTRIFICATION EXPANSION
As this work continued to expand, testing activities soon outgrew their space, so SwRI developed a dedicated facility completed in March 2018. SwRI’s new Energy Storage Technology Center (ESTC) is 10 times larger than the previous lab, providing plenty of room for thermal chambers and space for several electric vehicles. The new facility has two dedicated “abuse rooms” with separate ventilation systems and scrubbers, ensuring that no toxic materials escape, and that battery abuse testing can be done safely.
SwRI is now one of the few one-stop shops in the United States that performs all regulatory battery safety tests on cells, modules and even complete battery packs. And, thanks to the emissions scrubbing system installed at the fire technology laboratory in 2014, even pack-level tests can be done safely and without impacting the environment.
The new lab offers more opportunities for vehicle benchmark testing, calibration and validation services for power electronics and technology in electrified vehicles. The team has completed internally funded research programs to develop new algorithms to predict battery life and improve fast charging. In addition, engineers are using existing SwRI intellectual property to investigate and improve battery coolants.
In a future project, the team will also work with CPS Energy, San Antonio’s electric utility, on a grid storage experiment. CPS is building 5 MW of solar generation capacity and grid storage batteries at SwRI. Our engineers will participate in the operation of the system, performing experiments on the batteries and collecting data on the system for use in future applications.
TOMORROW’S CAFE MENU
Contrary to some reports in the popular press, the internal combustion engine is not dead, nor is it about to be replaced as the prime mover for the majority of the country’s transportation needs. Nonetheless, electrified vehicles are destined to be a big part of future mobility solutions. SwRI’s new Energy Storage Technology Center offers a full menu of innovative solutions for electric vehicles, which will play an increasing role in helping the automotive industry meet CAFE standards. Figuring out the safest, cleanest and most efficient means to fuel our way of life benefits all of us, no matter where we live or what we do.
For more information, visit Electric Powertrain and Energy Storage Systems.
Check out this video about SwRI’s new Electric Storage Technology Center.
Questions about this article? Contact Graham Conway at +1 210 522 5134.