Background
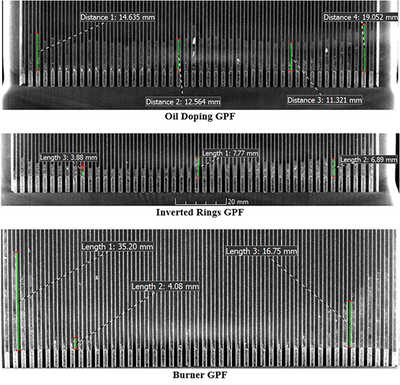
Particulate matter (PM) emissions from internal combustion engines have been of great interest to legislators. When evaluating the relative contributions of diesel- and gasoline-powered vehicles to ambient PM in the United States in 2000, the U.S. EPA concluded that diesel-powered vehicles contributed 62 percent of the mobile source inventory, while gasoline-powered vehicles contributed 38 percent. However, the California Air Resource Board (ARB) predicted that 32 percent of PM emissions were from diesel-powered vehicles and 68 percent were from gasoline-powered vehicles. Even though the results were not consistent, these studies demonstrated PM emissions from gasoline-powered vehicles can be significant.
With diesel particulate filters (DPF) implemented on diesel engines for US2007 heavy-duty diesel emissions compliance in the United States, tailpipe particulate matter (PM) emissions from diesel engines were substantially reduced, often by 99 percent or more. It is understood that a conventional gasoline engine emits a higher number of particulates than those from a DPF-equipped diesel engine for comparable engine power ratings given the relatively small diameter of gasoline particulates. Due to these reasons, and the implications for public health, PM emissions from gasoline vehicles are coming under increased scrutiny in the U.S. The European Union has already implemented a Particle Number (PN) standard for both on-highway heavy-duty and light-duty applications. The light-duty regulation (Euro 6c) does not exclude gasoline direct-injected (GDI) applications (previous PM regulations were only specific to compression ignition engines). Therefore, there has been an emergence of production-intent gasoline particulate filters (GPF) for light-duty GDI equipped applications.
Starting with MY2015 light-duty vehicles, ARB LEV III standards phased in a new 150,000-mile durability requirement, compared to the LEV II 50,000- and 120,000-mile standards. The combination of requiring a significant reduction in PM and an increase in the durability requirement may pose a concern for GDI applications equipped with a GPF. Since a conventional wall flow GPF captures the majority of solid material from the combustion process, the accumulation of inorganic components (i.e. wear metals from the engine or constituents found in the lube oil), termed as ash, will accumulate in the GPF over the lifetime of the application. Unlike organic components of PM, such as elemental carbon, that can be removed through a regenerative oxidation process, these inorganic components that accumulate are unable to be removed through traditional engine and aftertreatment management systems. Ash can only be removed through offline cleaning techniques. However, legislation has stated that light-duty emissions control systems must be warranted for the full useful life (FUL) of the vehicle. Therefore, devices such as the GPF typically are not replaced and do not have recommended cleaning intervals due to the accumulation of ash.
Accelerating ash accumulation in particulate filters has been studied extensively since the emergence of the DPF for diesel applications. Various acceleration methods have been evaluated and several of them have their drawbacks as they may not accurately replicate the deposition mechanisms that are observed in the real-world application. Acceleration methods for ash accumulation utilize lube oil as the primary driver, since multiple studies have confirmed the dominant source of ash is related to engine lube oil consumption.
While various methodologies have proven themselves as accurate and effective for accelerated ash loading of the DPF, the physical and chemical mechanisms for ash loading of the GPF are vastly different and will likely require an alternative strategy.
To address these significant differences between the conditions for a DPF and GPF, SwRI proposed to evaluate three methods for accelerated ash accumulation in the GPF:
- Add lube oil to the engine fuel supply using a liquid flow controller
- Invert the lower compression ring on all pistons to increase oil consumption via realistic mechanisms
- Load ash using SwRI’s ECTO-LabTM burner technology (combust oil in a burner)
Approach
This project consisted of evaluating various engine- and burner-based accelerated ash loading techniques. Each technique was compared to a non-accelerated, field generated GPF for their ash deposition profile and GPF pressure drop performance.
Accomplishments

The goal of this study was to achieve two results: gain capabilities in GPF accelerated ash loading and determine an acceptable accelerated ash loading approach that replicates real world ash deposition mechanisms for GPFs. The burner-based method produced the lowest density ash plug layer with a parabolic deposition profile, as shown in Figure 1. Although this method provided the most rapid approach to achieving the full useful life ash loading level of 30 g/L, the deposition profile and density of the ash did not replicate the highly dense and uniform ash plug layer observed in the field returned GPF. The oil doping method provided a controllable oil consumption rate over the period of ash loading. This method provided a uniform deposition profile by 30 g/L ash loading. However, the ash did not appear to be as dense as the field returned GPF. Finally, the inverted rings method yielded a deposition profile that was both uniform across the inlet channel plugs and highly dense. Based on the scans of the Field Returned GPF, as shown in Figure 2, the inverted rings method appeared to be superior in replicating ash deposition mechanisms observed in the real world. It is understood that there are many factors that can directly affect ash deposition profiles in particulate filters, including engine duty cycle, operational temperature, substrate design, and others. However, the methods and techniques utilized in this work can assist with considerably reducing the required times for full useful life ash loading of a GPF.