BACKGROUND
Carbon fiber composites have become extremely popular when high specific modulus and high strength are needed under severe weight restrictions. Due to their cost, their main application is in aerospace; but they are becoming also common in other industries like automotive, recreational sports, etc. Although CFRPs are very strong and stiff, their impact performance is very poor when compared to other conventional materials. Under low velocity impact 2D composites can delaminate, and under high velocity impact they are easily perforated. Other composite materials with polymeric fibers like Kevlar® or ultra-high-molecular-weight polyethylene fibers are much more efficient under ballistic impact. The main reason is that the carbon fibers are more brittle and hence absorb much less energy under impact when compared to the ballistic polymeric fibers. Due to the poor performance under ballistic impact of the carbon fiber composites, it is difficult to find in the literature a complete study aimed at obtaining a reliable computer model for ballistic impact on carbon fiber composites. A mesoscale computer model was developed that is validated by comparing the results from the mechanical and ballistic test with the computations, see Figure 1.
APPROACH
This work presents a thorough experimental campaign of both the material constituents and the composite, including loads in the different directions (longitudinal and transverse tension, shear, delamination, etc.) at low and high strain-rates (Hopkinson bar tests), and ballistic tests. The study is performed on non-woven (2D) non-crimp composite as well as a 3D woven composite with the same constituents. The material properties were determined using computations that reproduce the material tests. Ballistic tests were performed on single carbon fiber yarns to find the transverse wave speed and critical impact velocity. Composites were also tested ballistically and deflection histories recorded using two diagnostic techniques: digital image correlation from images recorded on two high-speed video cameras and transverse deflection from an ultra-high-speed camera. Ballistic limits were determined for the 2-D and 3-D composites. A mesoscale computer model was developed that is validated by comparing the results from the mechanical and ballistic test with the computations, see Figure 1.
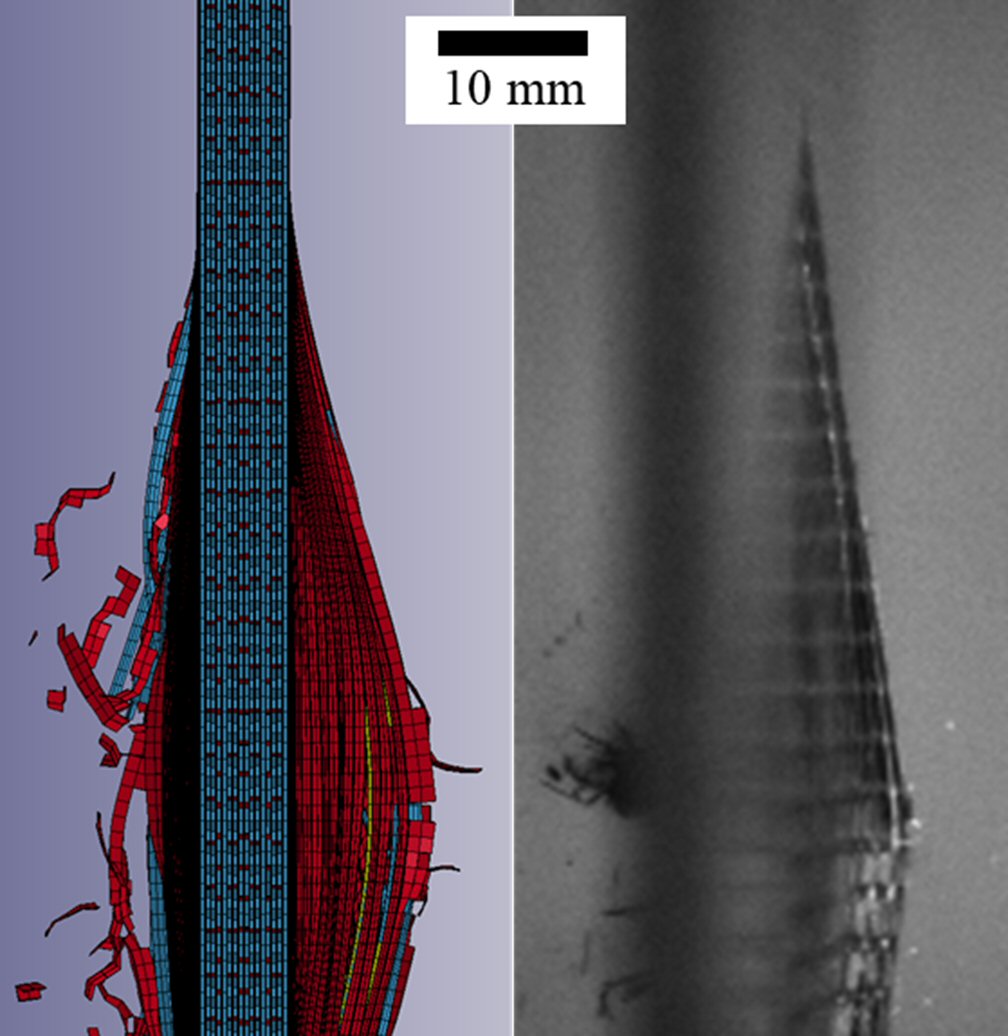
Figure 1: Deflection from ballistic simulation of 6.35-mm-thick 2D CFRP (left) is compared to high-speed video image from corresponding test (right) approximately 70 μs after impact.
ACCOMPLISHMENTS
The main conclusions from the project are:
- PR520 resin is strongly strain-rate dependent but strain-rate effects for the composites are probably negligible.
- 3-D specimens are stronger than 2-D under shear.
- Theory and numerical simulations predict properly the transverse wave velocity measured in the single yarn impact tests.
- The ballistic limit of the 2-D and 3-D composites with same areal densities is similar.
- The damage area found in 3D woven targets after initial and repeated impacts was nearly 70% smaller than the damage areas seen in the 2D targets. This finding supports the relative increase in damage tolerance of 3D composites when compared with 2D composites.
- The computer simulations capture properly the mechanical tests performed (tension, torsion, through-thickness tension tests).
- Using the material parameters obtained from the mechanical tests, the model captures well the ballistic limit without adding any strain-rate effects.
- Similarly, the model captures reasonably well deflection vs. time for the 2-D and 3-D panels.
In summary, the technique consisting on testing both the constituents of a composite and the full composite under different loads provides enough material data to build a predictive yarn-level model for ballistic impact without needing to calibrate further the material parameters.