Background
Dilute combustion in advanced gasoline and natural gas engines offers the greatest potential for increase in engine efficiency and reduction of emissions. However, the lean limit is determined by the capability of the ignition system to reliably ignite the fuel-lean mixture. As compared to other high-energy ignition systems, a passive pre-chamber ignition system offers a more simplified solution since it requires minimum engine modifications and is structurally less complex. Although passive pre-chamber ignition systems have been investigated for many years, and several experimental and computational studies have been performed, they have achieved little commercial success. Their performance is quite robust in a controlled laboratory environment, but they have been found to be extremely sensitive to residual exhaust concentrations and the ability to control the fresh air to fuel ratio within the chamber. The objective of this project is to demonstrate through computational fluid dynamics (CFD) simulation that a significant improvement can be achieved in pre-chamber scavenging and air-fuel mixing of a passive pre-chamber engine. This will result in enhanced combustion performance, increasing engine efficiency with reduced emissions compared to the baseline engine design with a standard spark plug.
Approach
Project tasks included creating a design matrix encompassing key pre-chamber design variables for both passive pre-chamber gasoline and natural gas engines, performing 3D CFD flow and combustion simulations, and analyzing parameters that govern the pre-chamber scavenging and flow field and combustion performance to achieve an optimum pre-chamber design that performs better than the baseline engine without a pre-chamber. Gasoline engine pre-chamber optimizations were carried out at both full- and light-load conditions. Natural gas engine pre-chamber optimization is currently in progress.
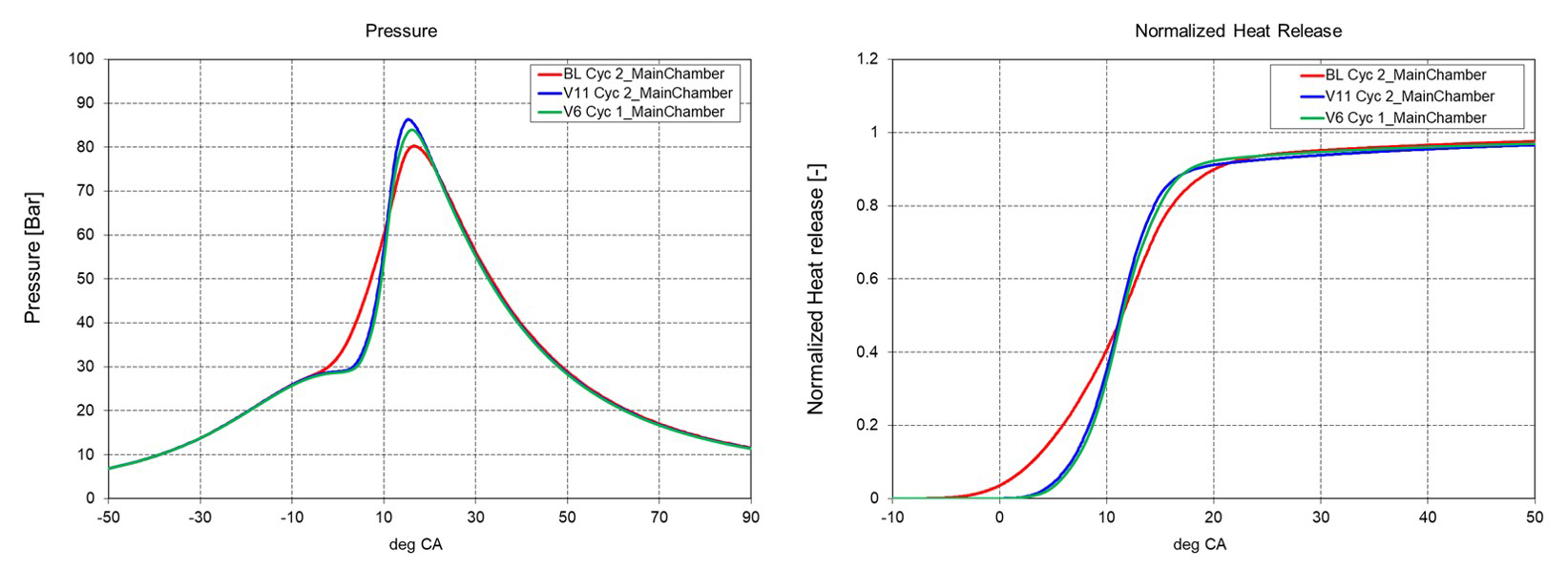
Figure 1: Pressure and normalized heat release comparison between open chamber (BL) and optimized pre-chamber engines (V6 and V11) under high-load condition for gasoline engine.
Accomplishments
A comprehensive pre-chamber design and analysis methodology was created for spark-ignited pre-chamber engines. Under high-load conditions for a 1.2L gasoline engine, an optimized pre-chamber design with uniform hole size was found to perform very well. The 10-90 burn duration (time or crank angle increment during which the tenth percentile to the ninetieth percentile of fuel is burned) was reduced to two-thirds the duration seen under the same conditions in an open-chamber engine and combustion efficiency was increased by almost 2%. However, the pre-chamber designs with uniform hole size did not perform as well at light-load and high-residual gas conditions. Significant improvement was made in pre-chamber scavenging by using varying outlet nozzle sizes based on the bulk flow-field and pre-chamber turbulence. The 10-90 burn duration was reduced by 20% compared to an open chamber engine under light-load and high residual-gas condition for the novel optimized pre-chamber design. It performed better at high-load conditions as well compared to an open-chamber engine and the 10-90 burn duration was reduced by 25%.
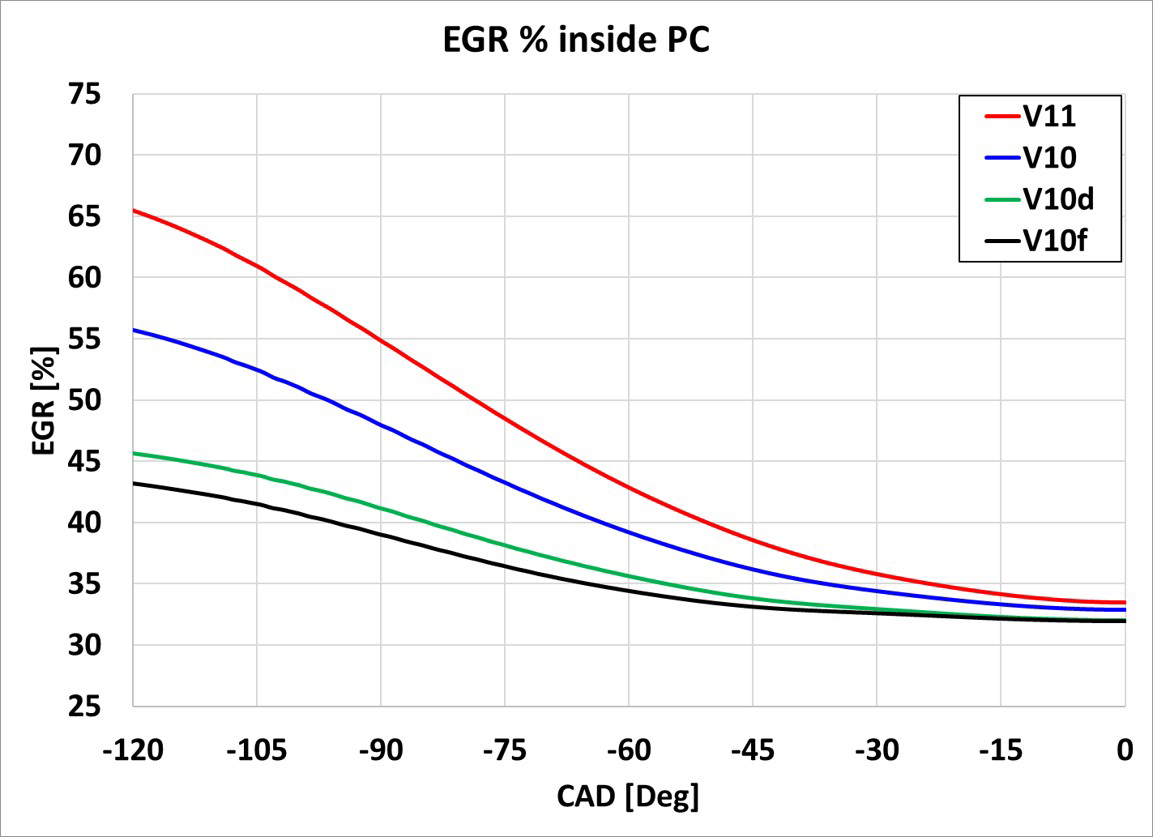
Figure 2: Examples of improved pre-chamber evacuation (Cases V2a, V2b and V2c) as compared to baseline pre-chambers (Cases V1a and V1b) at light-load and high-dilution condition for gasoline engine.