Background
Modern engine design strategies that increase performance while reducing emissions result in higher component temperatures that are pushed to their limits. To predict temperatures and stresses in these components, 3D computational analysis tools are used. Implementation of these tools requires several assumptions, each of which adds error to the analysis which must be accounted for with conservative design limits. One way to reduce these errors is to validate the models with testing.
Thermal management in engines is controlled by flowing coolant through the high-temperature components. This project leveraged a test rig developed on internal research project 03-R8848 to experimentally determine convective heat transfer coefficients, as well as boiling heat transfer.
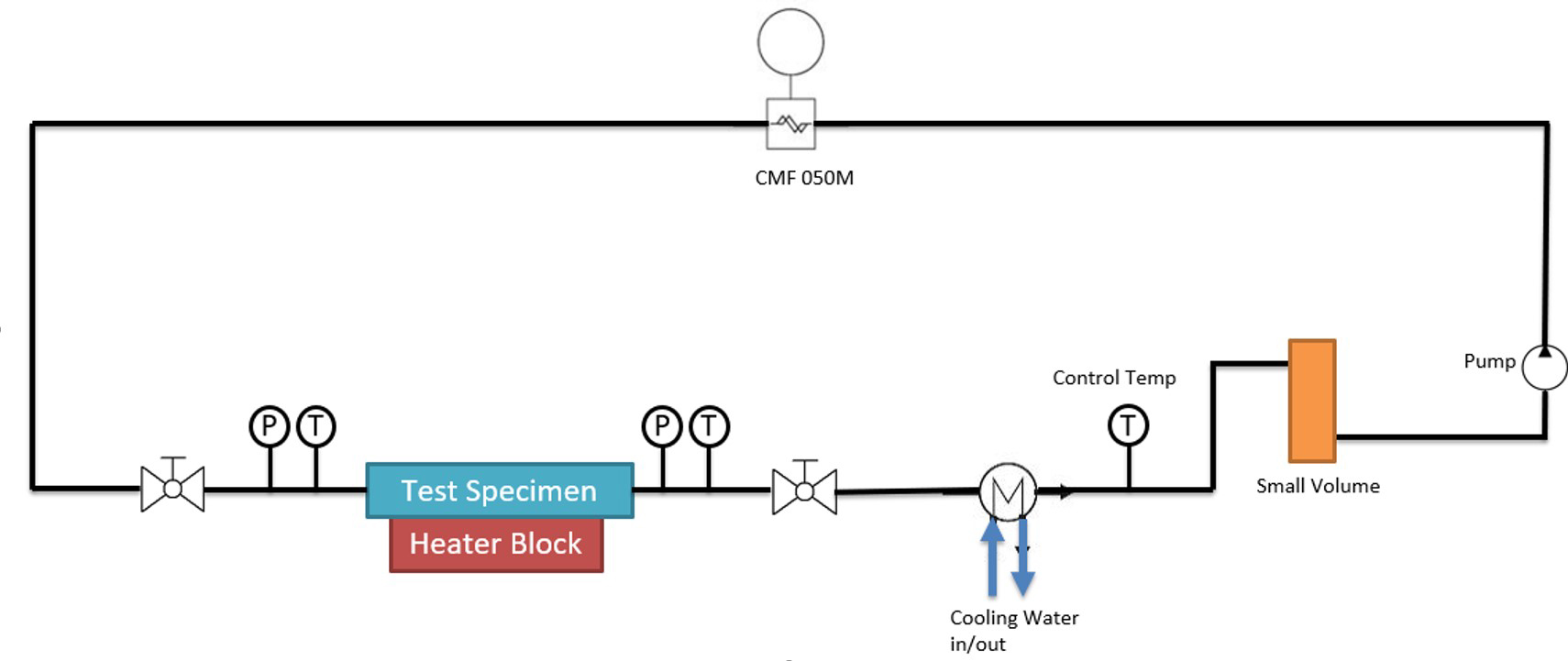
Figure 1: Heat transfer test rig schematic
Approach
The test specimens consisted of cast iron and cast aluminum parts containing a rectangular flow passage. Along this passage, five thermocouple pairs were used to relate the temperature change to a local heat flux. Inlet and outlet temperatures and pressures of the fluid are also measured. The test data is gathered by flowing coolant at various flow rates and incrementally increasing heat input into the test specimens. With the data measured, heat flux can be determined as a function of surface temperature as well as heat transfer coefficients. This data can then be used to calibrate relevant coefficients and parameters in finite element and CFD models.
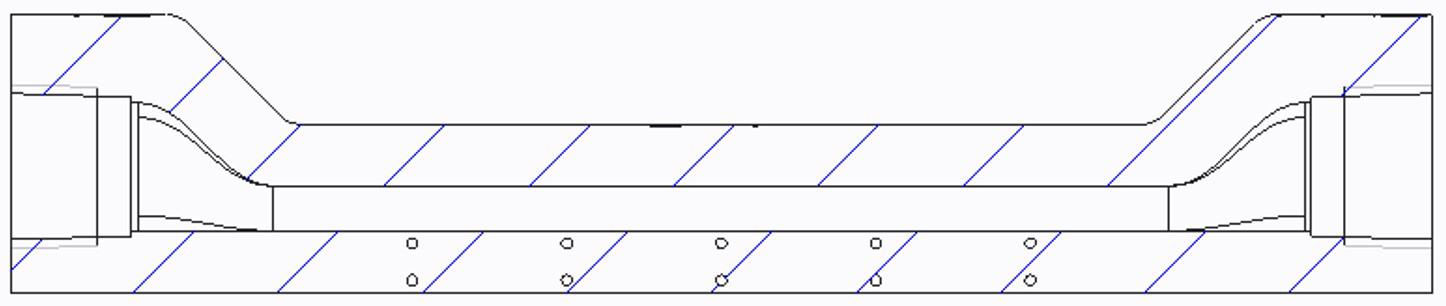
Figure 2: Cross-section of cast test specimen with rectangular flow passage.
Accomplishments
The test specimens consisted of cast iron and cast aluminum parts containing a rectangular flow passage. Along this passage, five thermocouple pairs were used to relate the temperature change to a local heat flux. Inlet and outlet temperatures and pressures of the fluid are also measured. The test data is gathered by flowing coolant at various flow rates and incrementally increasing heat input into the test specimens. With the data measured, heat flux can be determined as a function of surface temperature as well as heat transfer coefficients. This data can then be used to calibrate relevant coefficients and parameters in finite element and CFD models.
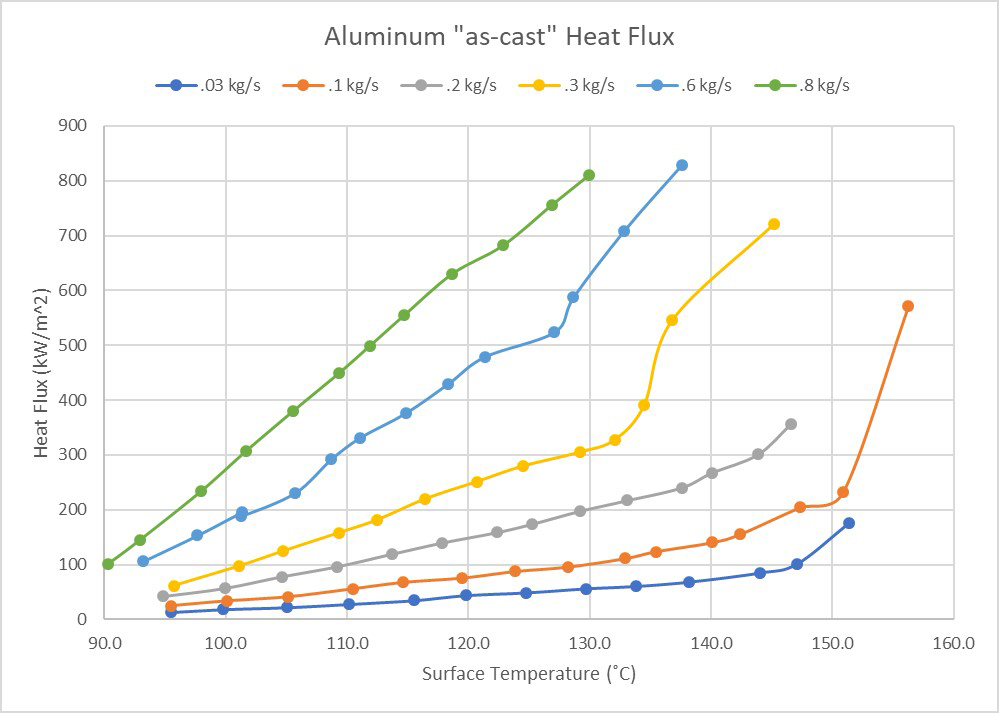
Figure 3: Aluminum as-cast heat flux values as a function of surface temperature.