Background
The purpose of this project was to investigate the ability of SwRI’s Renishaw AM250 to additively manufacture shape memory alloy (SMA) components, specifically nickel-titanium (NiTi, nitinol). Nitinol has become a popular alloy due to its unique elastic and shape memory properties and has numerous applications, ranging from biomedical to aerospace. While nitinol has many uses, there are drawbacks that have limited its use to select applications. Nitinol is readily available in smaller stock sizes, but there are few suppliers of large stock material. This makes the bulk material prohibitively expensive in small quantities. Additionally, nitinol can be difficult and expensive to machine due to work hardening. Its elastic properties also make it challenging to form into complex shapes. To date, additive manufacturing of shape memory alloys (AM-SMA) appears to be limited to academic institutions based on an initial survey of published research. While the published research provides a good starting point, none of the groups specifically used an AM250. Also, these institutions are focused on basic research without an intention to transition the technology to practical applications for industry.
Approach
The objective of this research was to develop build parameters at SwRI for additive manufacturing with NiTi powder to reduce the issues of working with standard nitinol material. Testing was also performed to determine the recovery force generated from the shape memory characteristic of the material. This research can also help establish SwRI as a leader in a technology that is growing but remains underdeveloped in industry due to manufacturing and cost limitations.
Small-scale test builds helped establish ideal build parameters for the NiTi powder. These parameters were used for larger builds and to fabricate test specimens. The test specimens were also compared to specimens fabricated from the raw ingot material.
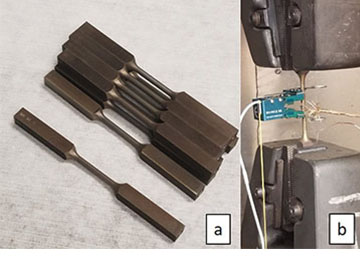
Figure 1: (a) Ingot tensile specimens; (b) Tensile test setup with extensometer and thermocouple.
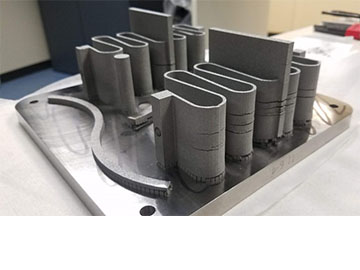
Figure 2: Full build with partially completed parts and cracking
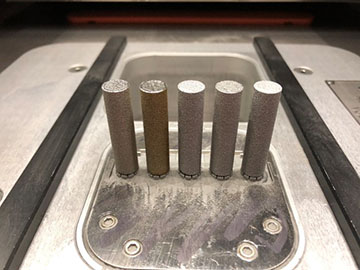
Figure 3: Successfully completed build on NiTi inserts in modified build plate.
Accomplishments
All mechanical and shape memory testing was performed on the ingot material and provided a good understanding for working with NiTi (Figure 1). Specimens fabricated from initial builds, where cracking was present, did not perform as well as the ingot material but did show a shape memory effect by generating a recovery force.
After successfully fabricating small density cubes on the AM250, large builds were attempted with varying degrees of success (Figure 2). The most successful builds still showed cracking and delamination throughout the part. Based on the results of the full build, an additional small-scale build was performed. This build used a modified base plate that allowed for building directly to NiTi inserts. It was believed that the material differences between the standard titanium base plate and the NiTi powder were creating the delamination and cracking issues experienced in other parts. This process appeared to provide the best prints with no noticeable cracking (Figure 3). Additional testing of this method with other parameters and larger builds is necessary to further validate this process.