Background
Micro- and nanoencapsulation are core competencies within Southwest Research Institute, making SwRI a recognized leader in the field of encapsulation with over 70 years of research and development experience ranging from proof-of-concept to production. With continued exposure to a wide variety of clients, industries and technologies, we have observed several common trends and deficiencies in common commercial encapsulation technologies. For example, companies familiar with the field of encapsulation are in search of encapsulation formulations and technologies capable of producing highly loaded core-shell microcapsules smaller than 100 µm with formaldehyde-free, non-animal source, natural materials that are approved for use in food, pharmaceuticals and cosmetics. Pending domestic and international bans on microplastics are accelerating demand for biodegradable encapsulation materials. Furthermore, these capsules must be prepared using equipment currently available at contract manufacturing facilities with minimal modifications.
This project began to address the unmet needs for the field of encapsulation related to both the technique used for encapsulation and the formulations. The adaptation of existing drying oil film-forming materials was combined with classic emulsion-based microencapsulation to form a new emulsion-based encapsulation system.
Approach
Our approach is the preparation of emulsion-based microcapsules using a novel shell material composed of drying oils, such as tung oil or linseed oil. The oils, core diluents, catalysts, accelerants and crosslinking conditions were investigated to identify a stable and reproducible encapsulation process. The capsules were characterized for size, morphology, payload and shell structure. Subsequent capsules were prepared with model compounds to demonstrate the performance of the novel shell material, followed by preparation of capsules with industry-specific core materials. A general schematic of the encapsulation process is shown in Figure 1.
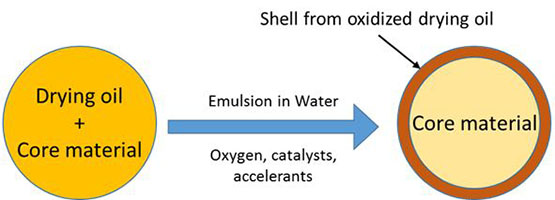
Figure 1: General schematic of the encapsulation process.
Accomplishments
Microcapsules were successfully prepared using a newly developed interfacial polymerization process based on the oxidation of drying oils. Capsules were prepared with a core-shell morphology, less than 50 µm, processing less than 50°C, with a payload over 65%, using materials that are mostly approved for pharmaceutical, food or cosmetic use. The materials are inexpensive relative to other encapsulation systems, with many available from natural sources. The oxygen barrier performance, payload and shelf-life were not fully quantified.
The formulation for shell formation was developed through evaluation of a variety of drying oils, surfactants and catalysts. The most successful formulation used a dispersed phase of 30:70 tung oil to core material and bulk phase dispersants, surfactants and oxidation catalysts. Evaluation of shell formation conditions found that the use of bubbling air for up to 48 hours at 45°C fully cured the capsule shell wall. Capsule shell formation was primarily characterized using optical microscopy.
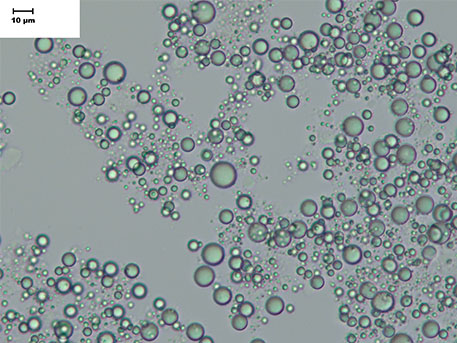
Figure 2: Oxidation protection results were inconclusive in encapsulated limonene.
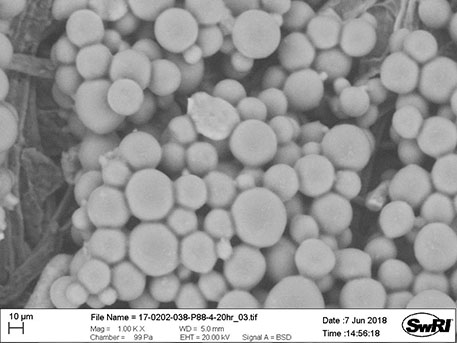
Figure 3: Octadecane performed well after encapsulation, showing the same phase change behavior before and after encapsulation
Performance of the drying oil capsules was evaluated for oxidation protection, water encapsulation, phase change material encapsulation and mechanical integrity. Using encapsulated limonene (Figure 2), oxidation protection results were found to be inconclusive due to potential rupture of the capsules during drying. Water encapsulation was successful using a double emulsion process. However, leaking of water-soluble dyes occurred, indicating poor barrier properties on initial formation. Encapsulated octadecane (Figure 3) performed well after encapsulation, showing the same phase change behavior before and after encapsulation. Mechanical testing was inconclusive due to testing difficulties and potential interference from the use of silica in the formulations.
Drying oil capsules were successfully prepared with a variety of representative core materials from major industries. Limonene was encapsulated as an example of a common volatile component used in both the flavor and fragrance industries. MCT, a common diluent in the same industries, was also encapsulated. Lavender oil was encapsulated as an example of an essential oil, and octadecane was encapsulated as an example of a phase change material. Finally, aqueous dyes were encapsulated to demonstrate water encapsulation.