Background
Electrostatic analyzers (ESA) are the sensors of space plasma instrumentation that require complex machining and assembly of a multitude of small parts. The cost of machining the parts for ESAs can cost up to $100,000. Instrument mass is also a critical issue for any spacecraft system and, of course, less mass is always more desirable. A mass reduction can be achieved to a certain degree by appropriately choosing metals used in the instrument, and most metal parts would be made from aluminum. A 35% mass reduction over aluminum could be achieved by using magnesium. However, magnesium is more difficult and costly to machine than aluminum and the resulting debris from machining is hazardous waste. A mass reduction of up to 50% and a reduction in the parts count could be achieved if aluminum parts were consolidated and replaced with plastic that has a thin metal layer on it where required for functionality and/or strength. In this project, we intended to prove that a functional ESA could be manufactured using 3D printing so that a path forward for low-cost mass production of ESAs is allowed.
If we can transition a majority of the traditionally machined metal parts in a space plasma instrument to 3D printed and metal coated plastic, we can significantly reduce the cost, mass, and time to fabricate that instrument. Additionally, new ESA designs could be rapidly prototyped in-house to assess their viability or to confirm numerical particle tracing simulations at low cost prior to production.
Approach
The Space Science and Engineering Division purchased a printer to support this project. This printer was orders of magnitude better than a hobby-grade printer but still much less capable than a high-end commercially available printer (i.e., the $200,000 price range). Key aspects of the printer were that it allowed printing the high-temperature plastics that we intended to use in this project and had a heated chamber and build plate to minimize thermal stresses and part warping.
We knew a priori that the high performance polyetherimide thermoplastic resin blend ULTEM™ 9085 would pass NASA’s outgassing requirements based on other researchers’ use of it for satellite parts. To confirm good outgassing, we designed inner and outer electrodes for a simple 90-degree ESA and printed them. The parts were cleaned and subjected to vacuum and low outgassing was confirmed.
We worked with Mechanical Engineering Division personnel to metalize surfaces of the ESA electrodes with a gold-over-titanium scheme using a vacuum sputtering system. We also explored other metalization methods but did not try these as the sputtering method provided excellent adhesion.
We performed visual inspection and surface resistance measurements on the metalized surfaces prior to and post thermal cycling to determine if there would be any degradation of the metalization due to thermal cycling. We did not observe any degradation.
The ESA electrodes were then gapped and subjected to controlled-discharge high-voltage testing. Aside from some whisker burn-off during the testing, the metalized surfaces of the electrodes exhibited expected behavior and should function well in ESA applications.
Accomplishments
The accomplishments of this project are delineated below. We believe this effort paved the path for others to follow and improve upon our work.
- We learned how to print high quality Ultem 9085 parts that are void-free and have good surface qualities.
- We proved that we can 3D print Ultem 9085 parts that will pass NASA’s stringent outgassing requirements for space applications.
- We developed one process for metalization of 3D printed Ultem 9085 parts that exhibits excellent adhesion. We also explored other metalization options that would allow for better adhesion, metalization of inaccessible areas, and allow for thicker metal layers if necessary.
- We determined that thermal cycling does not result in cracking of the metalized layers and surface resistance measurements confirmed this.
- We explored various mechanical and chemical processes to achieve better surface qualities prior to metalization of parts.
- High-voltage testing of the metalized plastic parts was successful in that we ultimately achieved ~78.6-85.7% of the approximate maximum hold-off voltage expected in dry air for the electrode separation distance and we developed potential solutions to mitigate any unwanted adverse effects due to the application of high voltage to ESA electrodes.
- In Phase II of this project, we ultimately learned the limits of our 3D printer, but found outside services available to print parts on demand.
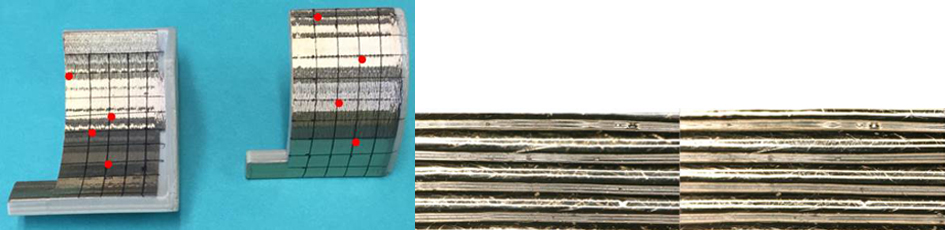
Figure 1: In (a) is shown the metalized surfaces of the simple 90o ESA with red dots showing the locations where surface resistance measurements were taken and in (b) is shown high magnification imaging on a specific location prior to and post thermal cycling.