Background
Metal additive manufacturing (AM) produces net-shape products and generally introduces local features and defects that need additional heat treatments to tailor the microstructure and meet the performance requirements. Because the as-built alloy contains a higher fraction of defects, the standard heat treatment developed for fully dense wrought material needs to be reviewed to improve its properties effectively. The purpose of the process design is to study the microstructure evolution and evaluate the alloy properties in a wide variable space, which can be labor- and time-intensive by only experimental approaches. A modeling framework can relieve the reliance on iterative experiments and provide an efficient and reliable way to design the manufacturing processes. This project aimed to implement a hierarchical model to simulate the microstructure evolution of the as-built alloy during the heat treatments.
Approach
This project developed an integrated computational materials engineering (ICME) framework that includes the data infrastructure and Python libraries to connect the experimental and computational workflows. This framework adopts a finite element method to solve the heat transfer equations and simulate the AM build process. The temperature history, Scheil-Gulliver equation, and martensitic transformation model are used to estimate the micro-segregation and the stability of the as-built microstructure. A diffusional precipitation model calculates the phase fractions and grain size of the alloy after the heat treatment. This hierarchical model is calibrated using a Bayesian regression function with literature data and leverages experimental data of Ti-6Al-4V from the MAKERS Focused IR&D program to test the sub-models.
Accomplishments
This ICME framework accommodates a hierarchical model to simulate the microstructure evolution in AM and post-build heat treatments. The verification result using Ni-7.5Al-8.5Cr alloy shows that this model captures the trend of the microstructure evolution. The results for Ti-6Al-4V bring insights to the transformation process and provide preliminary knowledge for future process design. All the experimental data and computer codes are archived using XML schema in a data infrastructure for future applications.
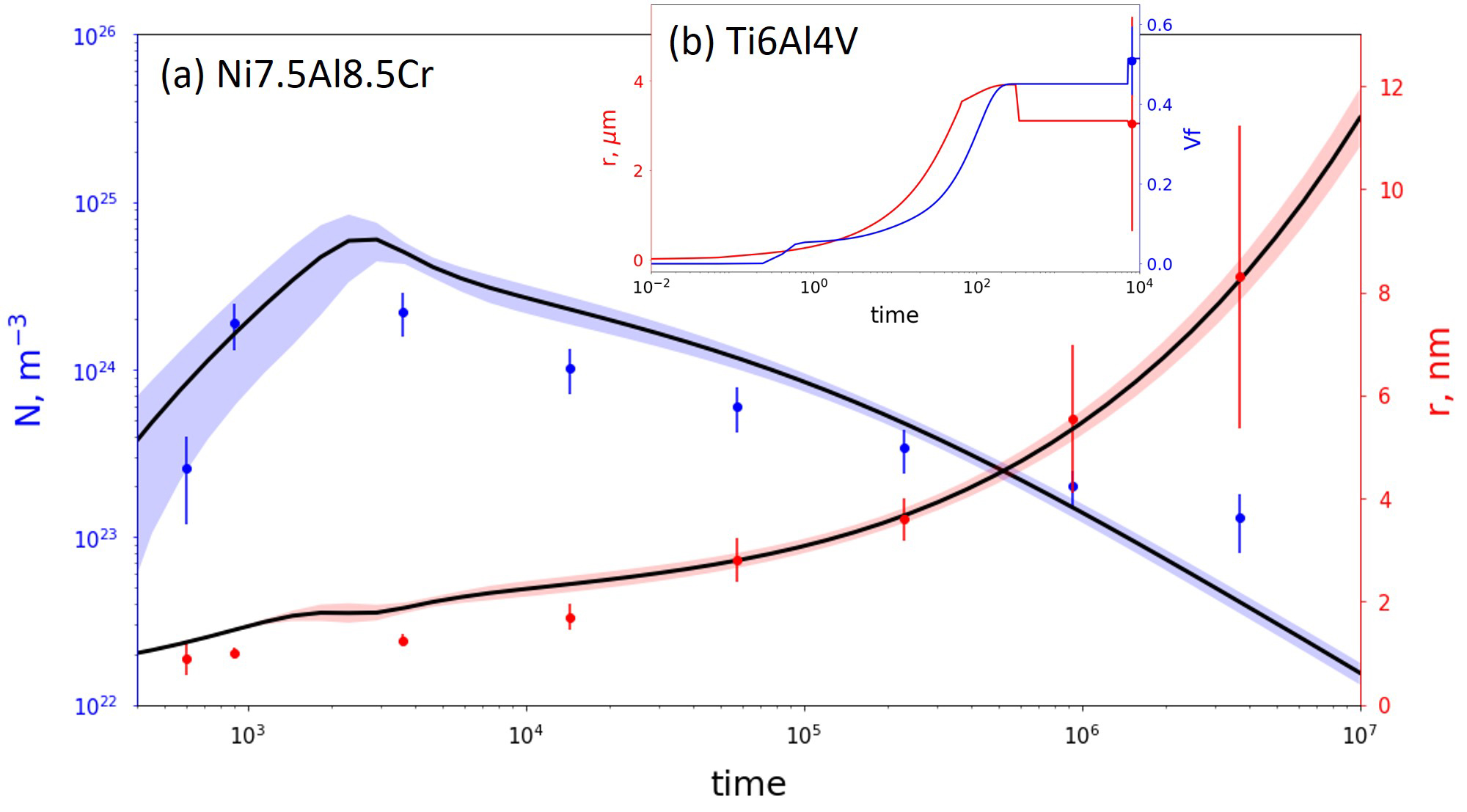
Figure 1. (a) The simulations use the last 10 sets of model parameters from Bayesian regression. The scatter points are the experimental results from [1]. The solid black lines are the mean of the results and the shaded areas represent the 95% confidence interval of the predicted mean. The shaded areas cover 95% confidence interval of the data along the processing time. (b) The calculation of mean radius and volume fraction of precipitation in Ti-6Al-4V.
[1] C. Booth-Morrison, J. Weninger, C. K. Sudbrack, Z. Mao, R. D. Noebe, and D. N. Seidman, “Effects of solute concentrations on kinetic pathways in Ni–Al–Cr alloys,” Acta Mater., vol. 56, no. 14, pp. 3422–3438, 2008.