Background
Regulated emissions output for medium-duty diesel engines are set to be significantly reduced over the coming decade. There are significant concerns that diesel engines will have difficulty meeting these future NOx and greenhouse gas (GHG) emission standards with reasonable aftertreatment costs.
New technologies, such as cooled EGR, have recently been developed for stoichiometric SI engines which enable high efficiency and high BMEP at low engine speeds. This enables torque curves comparable to diesel engines and therefore comparable operating conditions in vehicle, which enables diesel-like durability in an SI engine. Because of the potential improvement in durability and efficiency of SI engines, MD OEM’s have begun exploring the viability of SI in the market.
Furthermore, because these technologies use stoichiometric combustion, three-way catalysts can be used for simplified exhaust aftertreatment. With three-way catalysts technological and market maturity, they are very affordable and durable. SwRI has also demonstrated 0.02 g/bhp-hr NOx capability on an ISX12G heavy-duty SI engine with 12% efficiency improvement. In addition, conventional SI fuels (i.e. gasoline, LPG and NG) have historically been less expensive than diesel fuel.
Alternative fuels, such as natural gas, propane and methanol, offer a GHG benefit due to the chemical makeup of the fuel or its renewable sources. As such, many OEMs offer alternative fueled engines as an option for their vehicles. To date, all alternative fueled, spark-ignited, medium- and heavy-duty engines on the market derive from one of two development paths: (1) an automotive-derived pent-roof spark-ignited engine which is engine-dyno rated for medium-duty applications or (2) a medium- or heavy-duty diesel derived flat head spark-ignited engine. Neither of these two paths allow the engine to be fully optimized. The automotive-derived engines must be significantly de-rated from their light-duty configuration to provide for more durability (but the engine durability is still limited relative to the life of the truck) and generally offer very poor fuel economy. Evaluation of the EPA Phase 2 GHG rules suggests these engines will not be able to meet the 2024 and 2027 GHG targets as currently designed and built. The heavy-duty derived engines offer the required durability, but they are restricted in their efficiency potential as the combustion system is severely compromised for spark-ignited operation. The flat head design prevents the use of high tumble flow in-cylinder to generate the turbulence required for fast combustion, so a high-squish piston design is used instead. This can offer reasonably high turbulence, but with high heat losses due to the large surface area of the resulting combustion chamber. These converted diesel engines also appear to have substantial challenges in meeting the 2024 and 2027 GHG requirements.
Spark-ignited engines require turbulence generation to accelerate the burning velocity of the fuel to an acceptable level. This is usually provided for with an intake port design that directs the flow across the valve towards the far side of the cylinder, where a tumble flow pattern is generated. As the piston moves towards top dead center, the tumble flow “breaks down” into turbulent flow structures which wrinkle the flame and speed it up. The fast burn rate associated with tumble flow is valuable for SI combustion, the most relevant of which are the high base burn rate that can be achieved with proper tumble flow design and the resulting tolerance of dilution that comes with the high tumble and high burn rates.
Approach
The SwRI high-efficiency medium-duty single-cylinder engine was operated on natural gas fuel with a first-generation (Gen 1) and second-generation (Gen 2) combustion system. The Gen 1 combustion system was had a compression ratio of 9:1, while the Gen 2 system had a compression ratio of 12:1. The cylinder head was also modified to adjust the tumble ratio and turbulent kinetic energy, as well as the flow characteristics, of the Gen 2 combustion system. Thermodynamic analysis of the combustion was performed to determine the improvements in efficiency between two combustion systems. CFD was also performed to generate calibrated models to support further analysis.
Accomplishments
The gross-efficiency of the second-generation combustion system increased almost 5% at some operating conditions. Gross efficiency achieved almost 45.5% as well. The increase of efficiency was mostly due to the increase compression ratio, but the changes to the cylinder head to optimize tumble ratio and flow performance also improved overall losses of the engine at some operating conditions as well. The optimization of the cylinder head also increased dilution tolerance. The results show this architecture to be a viable base for development of a high-efficiency medium-duty spark-ignited platform.
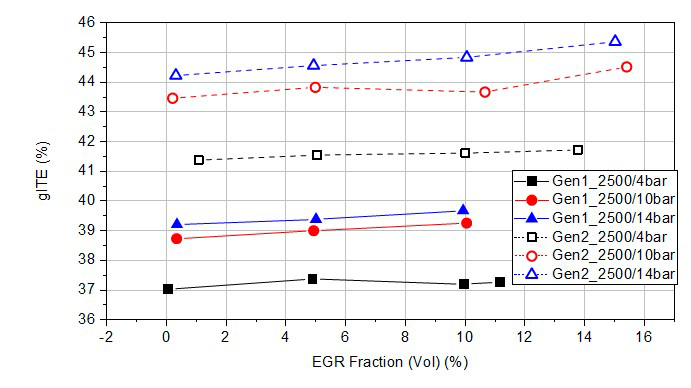
Figure 1: Indicated thermal efficiency during EGR sweeps at 2500 rpm for Gen 1 and Gen 2 engines.
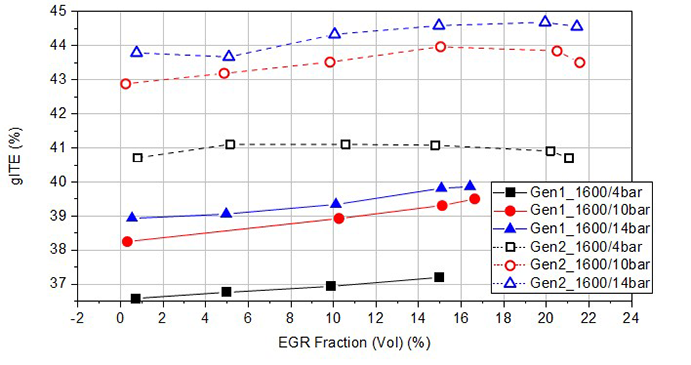
Figure 2: Indicated thermal efficiency during EGR sweeps at 1600 rpm for Gen 1 and Gen 2 engines.
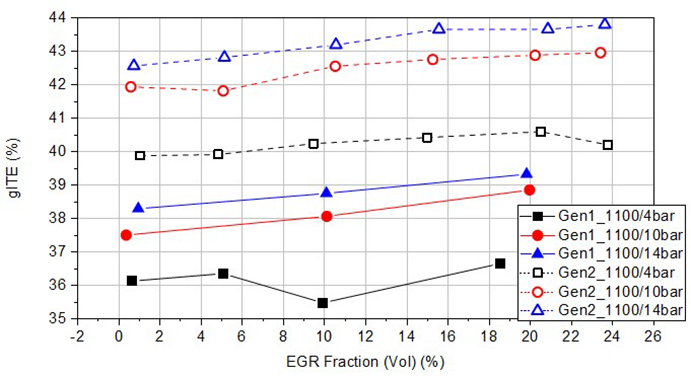
Figure 3: Indicated thermal efficiency during EGR sweeps at 1100 rpm for Gen 1 and Gen 2 engines.