Background
Production volumes of electric vehicles (EVs) have increased considerably across light-duty vehicle manufacturers in the past 10-15 years as battery storage safety and efficiency continues to improve. As EVs move into every light-duty vehicle category, power and efficiency will play a differentiating role. Increased power outputs will require a more-detailed understanding of the thermal and cooling mechanisms at play within the motor. Lubrication/cooling oil companies will also seek to differentiate their products within EV applications.
The primary objective of this Targeted IR study is to develop and validate a cooling computational fluid dynamics (CFD) model of a current e-motor using conjugate heat transfer (CHT) methods. A fully coupled CHT cooling model was developed to analyse the electric motor performance and cooling system design. Computationally efficient synergetic coupling between various physical processes were implemented in the model, including the electromagnetic e-motor power loss analysis, solid thermal analysis, and multiphase coolant fluid analysis.
Approach
A 3D CAD model was generated from an existing e-motor, namely Tesla Model 3 motor. A cooling CHT simulation model was established combining several modelling approaches. Two operating points were selected: typical real-world city driving and highest efficiency motor operation. The existing test data on this motor was used to validate the simulation.
A moving reference frame (MRF) approach was applied to simulate the e-motor rotation. Eulerian method-based Volume of Fluid (VOF) model was selected for two-phase modelling. Phase change model was coupled with the VOF model and solved via Eulerian method for vaporization. The Eulerian method treats the vapor and liquid phases as incompressible and solves transport equations for each phase of the mixture. Conjugate Heat Transfer (CHT) model was used to simulate the heat transfer between cooling oil and the e-motor parts.
The heat is generated within the motor due to the losses during the electromagnetic process. To have an accurate spatial heat generation within the stator, the winding and rotor for the CHT-fluid flow simulation, the electromagnetic process within the model was solved.

Figure 1: Stator Power Loss Contour
Accomplishments
A comprehensive 3D CFD CHT tool was developed in-house for a Tesla Model 3 electric motor and the developed approach was implemented in the 3D ANSYS software package. The resulted temperature was validated with the test data. Two K-type thermocouples were mounted in the motor to measure the stator surface temperature (top and bottom side). The resulted temperatures show a good agreement with test data and the difference is within the k-type thermocouple accuracy, which is +/- 2.2 °C. The motor power losses were calculated as the average of last two converged cycle results using electromagnetic analysis for both operating points. The calculated power losses were found to be within 5%.
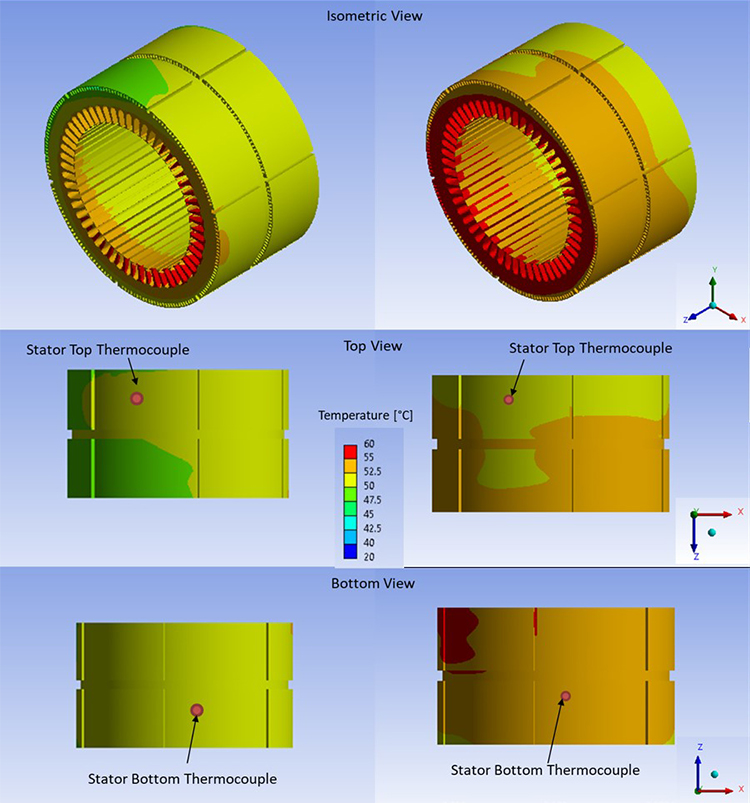
Figure 2: Stator Temperature Contours