Background
Friction reduction is considered a key technology for meeting the requirements of next generation internal combustion engine efficiency standards. Piston assembly to liner interaction can contribute up to 50% of total engine friction, of which approximately half can be attributed to the piston skirt to liner contact. These friction losses result from oil viscous shear, together with surface asperity interactions if the oil film thickness is marginal.
The primary objective of this research project was to further develop SwRI piston friction simulation expertise by accounting for the deformation of the piston skirt when calculating the distribution of the pressure in the oil film at the interface between the piston skirt and the cylinder liner, arising from the cylinder pressure and inertia loads acting on the piston. Previously, when a rigid piston was assumed, artificial modifications had to be made to the shape of the piston skirt to cater for it conforming to the liner under load. This approach, although satisfactory when test data is available, is not predictive and doesn’t account for differences between piston designs, materials and manufacturing technologies.
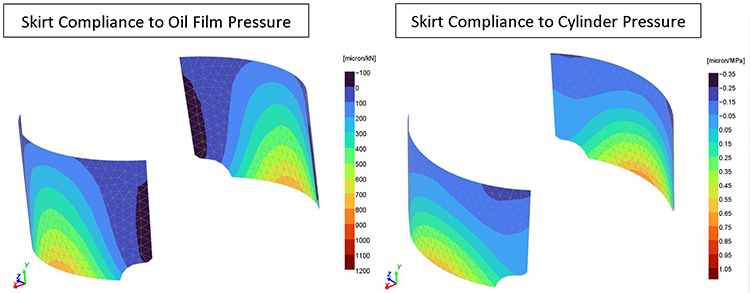
Figure 1: Processed Piston Skirt Compliance (Inverse of Stiffness)
Approach
This project utilized the latest simulation capabilities of a leading multi-physics computer-aided engineering (CAE) simulation package, which includes a flexible piston skirt object which was populated with data from a reduced degrees of freedom finite element analysis (FEA) ‘superelement’ piston model. Comparisons between a baseline rigid and the new flexible skirt version were made at motored (crankshaft spun, no engine firing) and full load engine firing conditions, and the effect of the flexible piston skirt on friction assessed. For the flexible skirt version the project also explored a modified piston design, detailed piston ring pressure modelling, and a flexible liner.
To provide accurate model information, skirt to liner friction coefficient measurements were made on the physical parts using a reciprocating friction rig at SwRI. Coordinate measuring machine (CMM) measurements of the piston skirt surface profile were also made (the skirt is not perfectly cylindrical by design).
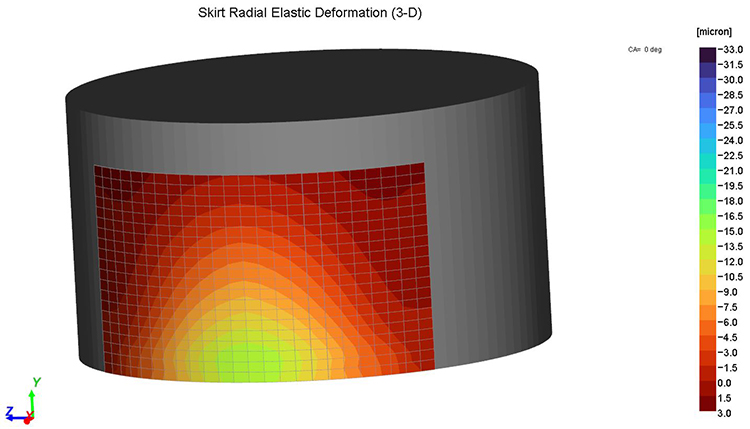
Figure 2: Example Skirt Radial Elastic Deformation (Full Load, at Top Dead Centre Firing)
Accomplishments
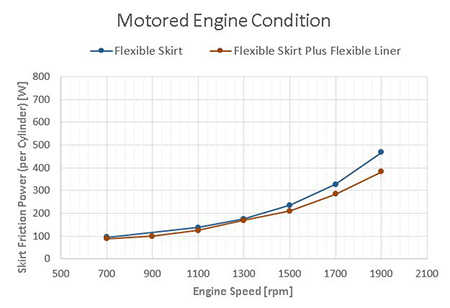
Figure 3: Effect of Flexible Liner (Motored Condition)
The flexible skirt simulation capability was successfully used at motored and full load engine conditions. Results showed a significant reduction in predicted skirt friction (~50%) compared to the rigid skirt model at motored condition. This demonstrates the importance of including a flexible skirt when correlating simulation models to engine friction measurements. At full load the predicted skirt friction was close to that expected, enabling “out-of-the-box” building of accurate friction models.
A design modification to the piston skirt wall thickness was shown to affect skirt friction, demonstrating that the software can be used to evaluate piston design changes. The effect of detailed ring pressure modelling was also quantified at the motored condition, with assumptions for ring groove and land pressures replaced by simulated pressures from an integrated blowby and ring motion model (1-D gas dynamics). This included ring dynamics within the groove and gas volumetric/mass flow rate through the various flow paths. The result was an increase the overall skirt and ring friction contribution by ~6%.
Simulations with a flexible liner at motored engine condition were found to reduce the predicted skirt to liner friction by up to 20%. Modelling of flexible liners enables comparisons between different liner designs (top, middle and bottom stop) on engine friction for the first time.