Background
Lithium-ion batteries have been established as the preferred energy storage technology for electrified vehicles and for renewable energy grid storage. These batteries are relatively lightweight and energy dense, but their use introduces some safety challenges. When exposed to mechanical abuse, via crushing or penetration, damage to the internal battery structure can result in short-circuits that release large amounts of energy which can lead to dangerous battery fires.
This project builds upon the mechanical abuse modeling capabilities developed in 03-R6001 and the thermal abuse modeling capabilities developed in 03-R8968 by combining these two approaches so that complete evaluations of damaged battery packs can be made to determine if resulting short-circuits will be safely contained or result in thermal runaway.
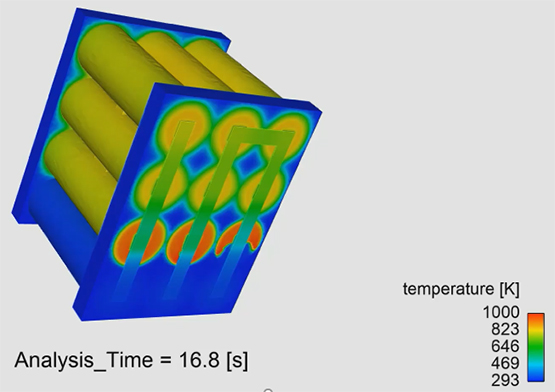
Figure 1: Temperature contour showing thermal runaway propagation in a 12-cell battery module.
Approach
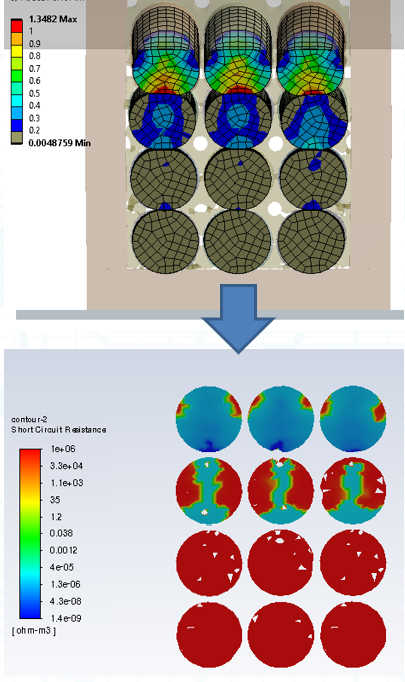
Figure 2: One-way mapping from the mechanical short-circuit damage metric to internal short-circuit resistance.
Test data and developed models from project 03-R6001 were used to develop the coupling method between the mechanical and thermal-electro-chemical domains. The voltage and temperature measurements from single cell drop tests were used to calibrate a mapping of a short-circuit mechanical damage metric to a corresponding internal short-circuit resistance that is applied in a electro-chemical thermal CFD model. This approach was then scaled to 12-cell and 72-cell module results to further calibrate the modeling approach for different series and parallel configurations of cells as well as dialing in convective and radiative model settings to capture thermal propagation. Finally, this approach will be used to design and test a novel battery module design that uses passive thermal management to prevent thermal runaway propagation.
Accomplishments
A mapping method for mechanical damage to internal short-circuit resistance has been developed. The other key finding so far is that the mechanical deformation must be considered when setting up the thermal model. The tested modules began with air gaps between the cells, but after the deformation caused by impact those gaps close and conductive heat transfer occurs between the cells. The team identified that the conduction directly between cells was the primary mode of heat transfer that led to thermal runaway in the tested modules.
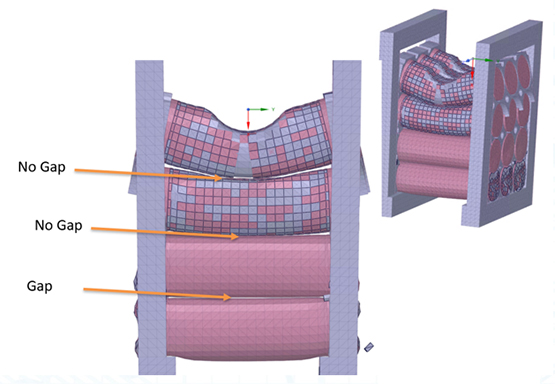
Figure 3: 12-cell battery module deformation causes gaps to close which creates new conduction paths that speed up thermal runaway propagation.