Background
Plasma-based manufacturing processes are not well known to the average person, but these processes are used to make cell phones, artificial hips, eyeglasses, car parts, clothes, and even electricity. More than $60 billion is spent each year on plasma-based processes for the application of coatings, surface treatments, and chemical processes. The physical, chemical, and electrical properties of a plasma dictate how it can be used or applied. For example, some plasmas are so hot they can melt metals in a matter of seconds while other plasmas can be used to safely treat a cut or wound on your skin.
SwRI has developed a unique plasma technique called High Power Impulse Plasma Source or HiPIPS. This technique combines a traditional atmospheric plasma jet with advanced power electronics to create a high-density plasma while maintaining a low temperature (less than 40oC) and low power consumption (35 watts). HiPIPS' unique combination of high plasma density and low temperature processing can enable enhanced chemical or physical processes that may not be achieved with conventional plasma techniques. The objective of this research is to characterize the coating or material properties that can be generated with a HiPIPS plasma

Figure 1: HiPIPS plasma head and finger contacting the low temperature plasma.
Approach
Computational fluid dynamic (CFD) simulations were conducted and validated with atmospheric plasma experiments to identify stable plasma operating conditions. Next, the atmospheric plasma jet was used to deposit metal and metal oxide coatings on polymer and metal substrates. Plasma coating variables such as gas flow, plasma power density, electrode materials, and substrate electric fields were correlated with resulting coating properties. Energy dispersive spectroscopy and scanning electron microscopy (SEM) were used to evaluate the morphology and composition of plasma deposited coatings.
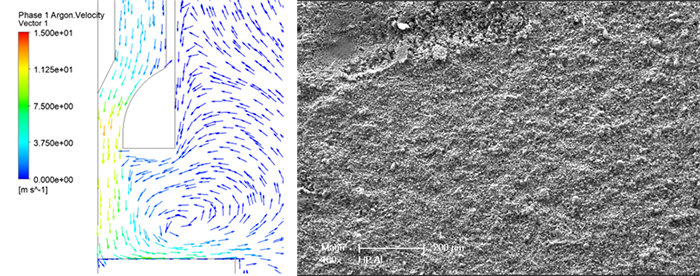
Figure 2: CFD simulation and an SEM photo of a HiPIPS coating.
Accomplishments
CFD modeling enabled the optimization of plasma head geometry which could achieve stable operating conditions. Experimental plasma trials were conducted under predicted stable operating conditions to explore the coating properties that could be generated. HiPIPS plasma conditions were developed to controllably produce coatings with hydrophobic or hydrophilic properties. Separately, the same HiPIPS plasma was used to explore plasma-based water decontamination, thus highlighting the diverse applications a HiPIPS plasma.
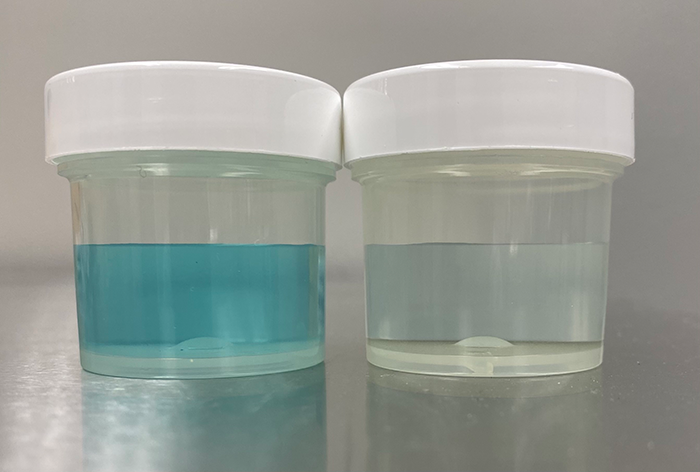
Figure 3: Before and after HiPIPS plasma water treatment.
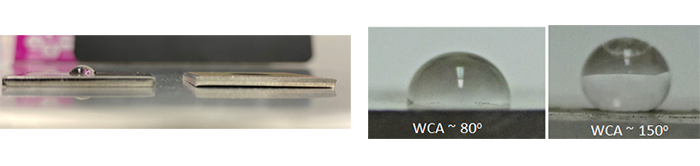
Figure 4: Hydrophobic and hydrophilic HiPIPS coatings.