Background
Advancing the nation’s capabilities in hypersonic vehicle technology is a high priority for the U.S. Department of Defense. This project will enable SwRI to capitalize on near-term opportunities to support imminent hypersonic vehicle production due to a lack of bandwidth in the industrial base. Few companies in the U.S. can test materials at the ultrahigh temperatures required, and there is broad concern that they will be unable to keep up with demand as new production lines begin operating.
Approach
The objective of this project was to develop the following capabilities:
- High strain-rate testing of materials up to 4,000°F
- Quasi-static testing of materials up to 4,000°F
- Machining of carbon/carbon parts
These were primarily achieved by integrating high power induction heating systems with our existing extensive testing capabilities. However, these ultrahigh temperatures brought additional complications for fixturing, gripping, measuring, and preventing oxidation of the carbon/carbon material. Machining was advanced through experience gained from creating test coupons from bulk material provided by external sources.
Accomplishments
We successfully integrated a 10-kW induction heating system with our split-Hopkinson pressure bar system and conducted high strain-rate compression tests up to 300 s-1 at temperatures nearing 3,300°F. This is shy of our 4,000°F goal, but is still a tremendous accomplishment and creates (to our knowledge) a combination of temperature and loading rate not available anywhere else.
For the quasi-static testing, we have integrated a 15-kW induction system with a hydraulic load frame and designed and procured an array of custom tungsten and ceramic fixtures to enable tension, bending, compression, and shear testing at ultrahigh temperatures. With this system, we demonstrated the capability of performing tests at temperatures exceeding 5,000°F.
Machining of these tough carbon/carbon composite materials has seen tremendous progress. With some custom designed tooling, the team has been able to produce complex geometries with extremely smooth surface finishes all while significantly reducing the cost of consumables.
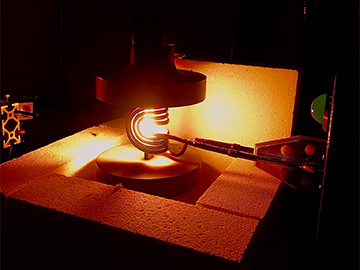
Figure 1: Setting up for a compression test of carbon/carbon at 4,100°F.
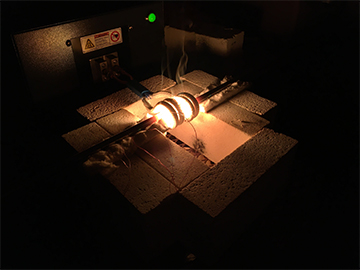
Figure 2: Heating test using SwRI’s new induction system. The glowing specimen is made of a carbon/carbon composite placed between tungsten bars to imitate Hopkinson conditions. The maximum temperature reached with this configuration was nearly 4,000°F.
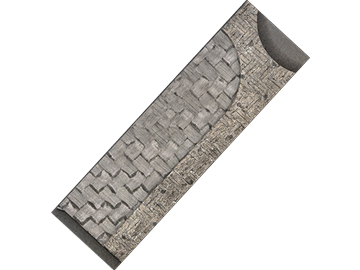
Figure 3: Example of machined carbon/carbon with smooth finish.