Electric grids maintain an instantaneous balance between supply and demand, with different resources making unique contributions to the power mix. Managing the balance between generation and load, while moving electricity from the source to the customer, is challenging.
As the world integrates more green, renewable resources, the complexities of balancing power generation with varying loads increase. Solar and wind are clean technologies, but they produce power that fluctuates with changes in wind and available sunlight.
To stabilize these fluctuations in solar applications, Southwest Research Institute engineers are developing critical technologies to combine renewables with natural gas-fueled energy to help make solar power a more cost-effective, dependable resource in the energy marketplace. Here’s how they’re doing it.
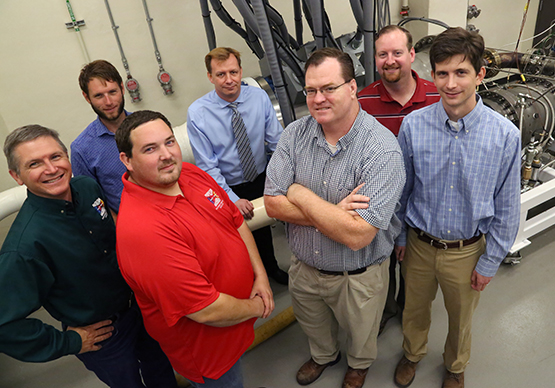
ABOUT THE AUTHORS
Dr. Klaus Brun (center) and Dr. Elliott Bryner (third from right) led a team of machinery experts, developing a unique, high-inlet-temperature combustion test facility at SwRI. The team included (from left) James Donnelly, Seth Cunningham, John Stubbs, Brun, Bryner, Nathan Poerner, and Shane Coogan.
CSP-Hybrid's Growing Role
With funding from the U.S. Department of Energy’s SunShot Initiative , SwRI is developing technology to supplement concentrated solar power (CSP) plants, or solar thermal plants, with natural gas burners. Solar thermal plants, much like traditional power plants, use heat to generate steam, which drives turbines to create electricity. SwRI’s hybrid solar-natural gas solution is aimed at increasing efficiency and output consistency, while operating in a sweet spot that minimizes the production of pollutants during gas combustion.
This hybrid solution applies to CSP plants that collect concentrated sunlight from thousands of heliostats, sun-tracking mirrors that reflect and focus solar energy to the collector at the top of a tower. The dense heat collected by these “power towers” can generate temperatures up to 1,000 degrees Celsius. The higher temperatures allow efficiencies — and costs — to approach those of conventional power plants using fossil fuels.
A New Injector for CSP Combustors
For peak power efficiency, the temperatures driving production turbines should remain constant. However, CSP plants provide variable levels of heat based on time of day, weather, and other conditions. To bridge this gap, SwRI engineers propose integrating a natural gas combustor to boost temperatures when sunlight input drops off. To produce the most efficient hybrid natural gas-CSP plant, SwRI needed to develop a natural gas combustor able to withstand inlet temperatures of 1,000 degrees C — about the melting point of gold.
Conventional combustors use a pre-mix injection system designed to minimize emissions of nitrous oxides (NOx). If temperatures get above 650 degrees C, current systems experience unwanted auto-ignition and flashback. Under these conditions, flammable mixtures ignite prematurely. The explosive results shorten combustor life and spew pollutants such as NOx.
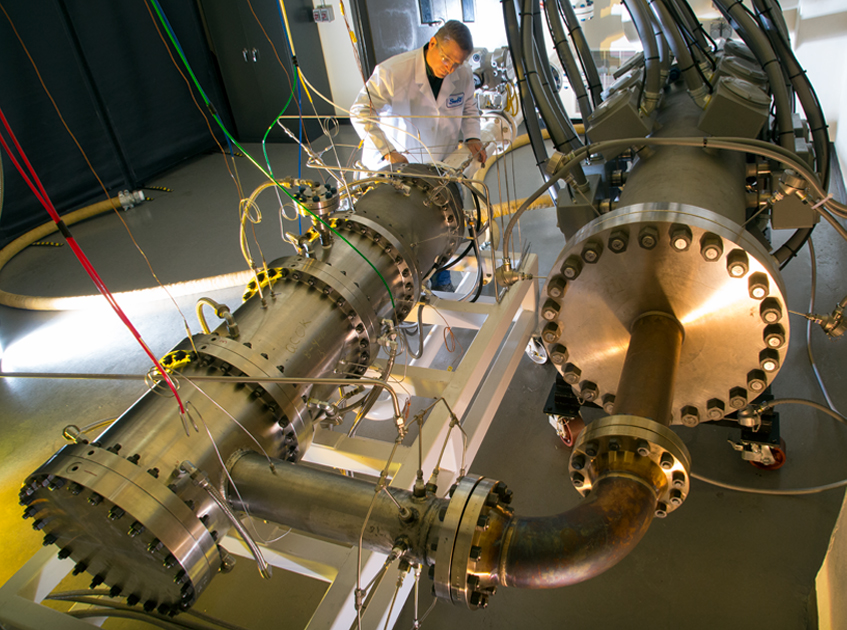
An SwRI team led by Dr. Elliot Bryner fabricated and commissioned a unique, high-inlet-temperature combustion test facility. This facility is capable of reaching combustor inlet temperatures of 1,000 degrees C with an air mass flow rate in excess of 2.0 kg/sec and pressures nearly eight times normal atmospheric pressure.
DETAIL
The SunShot Initiative is a national collaborative effort to make solar energy cost-competitive with other forms of electricity by the end of the decade.
SwRI’s Mechanical Engineering Division has overcome these challenges with a novel combustor design that uses a patent-pending arrangement of injectors. This computer-controlled system adjusts fuel injection rates to meet the precise heat addition requirements needed to maintain a constant turbine input temperature, despite fluctuating solar inputs. When the CSP-heated air is delivered to the combustor, the system determines how much natural gas is needed to heat up the air to reach peak efficiencies. The combustion process takes place in cylinders, better known as “cans.” When this air-gas mixture is ignited, it spins electricity-generating turbines.
Can Design, Multi-Bank Micro-Mix Injector
For this project, the SwRI team had to deal with problems associated with air heated above 650 degrees C, at which point air and fuel will burn immediately when they are mixed together without an external source of ignition. Instead of using conventional lean pre-mixing injection schemes to reduce NOx, the SwRI technology uses a series of injectors that introduce the fuel and air into the combustion chamber to reduce emissions.
To avoid triggering auto-ignition, SwRI engineers created a novel process for injecting, mixing, and burning the hot air and natural gas. For added durability, the combustor is made from a pressure vessel fabricated from a thick-walled, high-temperature cast steel alloy, designed to withstand hot inlet air, combustion, and exhaust gases.
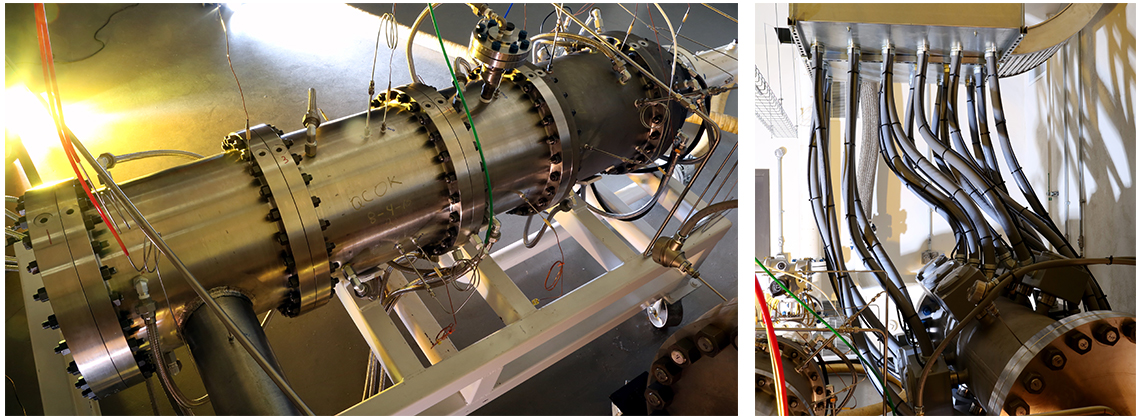
The combustor (left) is made from a pressure vessel fabricated from a thick-walled high-temperature cast steel alloy, designed to withstand extreme inlet air, combustion, and exhaust gases. Without access to many square miles of heliostats to generate high air temperatures, SwRI needed to develop a test rig to simulate superheated solar inputs. A 2-megawatt electric heater (right) raises inlet air temperatures to 800 degrees C. Then, a secondary gas-fired heater bumps temperatures up to 1,000 degrees C.
To keep it simple, this project looked at only a single combustor can. The prototype was developed at one-eighth scale for compatibility with a prototype gas turbine. The design can be scaled up for commercialization and modified for multi-can turbines.
To manage the airflow from the high-temperature air inlet to the combustion chamber, SwRI designed a multi-bank, micro-mix injector. This design regulates fuel injection in such a way that combustion of the air-fuel mixture is delayed until it reaches the combustion chamber. The circular injector, which looks a little like a showerhead, uses a series of metal plates pierced with dozens of small holes. The holes create a uniform lean mixture of air and natural gas to counter the effects of premature auto-ignition and flashback. When flame speeds propel combustion back into the injector, this “flashback” causes damage, greatly reducing injector service life. Because moving parts are problematic at high temperatures, the team used injection ports fed by multiple banks to manage airflow without a high-temperature valve.
Testing and Evaluation
To develop and evaluate this design, SwRI developed a sophisticated test rig in its Turbomachinery Research Facility. Without access to many square miles of heliostats to generate high air temperatures, engineers needed to simulate the superheated solar inputs. A 2-megawatt (MW) electric heater raises inlet air temperatures to 800 degrees C. Then, a secondary gas-fired heater bumps temperatures up to 1,000 degrees C. During testing, SwRI monitored the combustor rig with a suite of instrumentation. Thermocouples measured air and metal temperatures. Steady-state pressure transducers and a gas sampling system determined the composition of combustion products. A centrifugal compressor, designed by SwRI engineers as part of a previous Department of Energy project, delivered the pressurized air.
During proof-of-concept testing in 2015, the SwRI technology mixed record-high temperatures of heated air with natural gas in a combustion chamber.
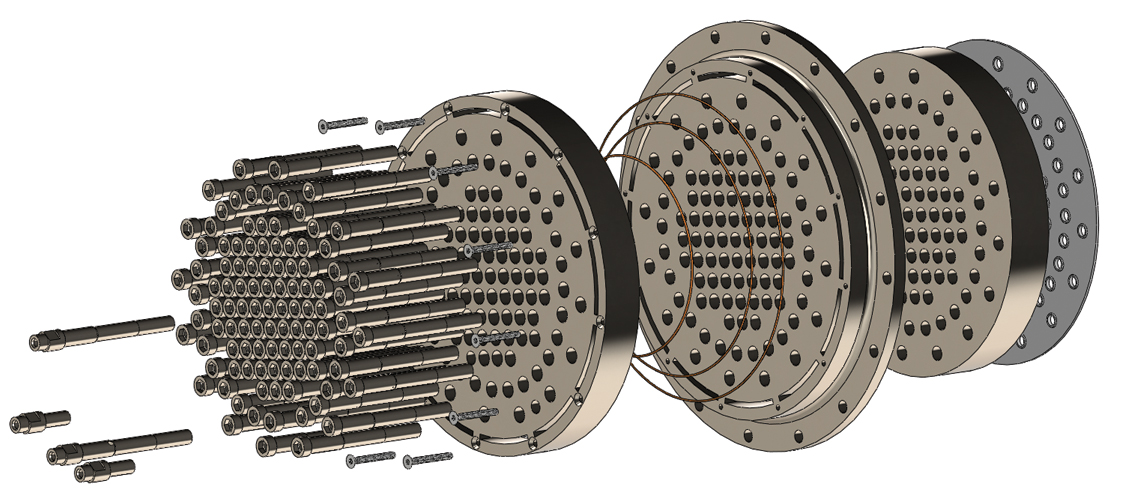
SwRI designed this novel multi-bank, micro-mix injector to regulate natural gas injection. The air-fuel mixing is delayed until it reaches the combustion chamber. This expanded engineering drawing shows the internal complexity of the finished component.
Conclusions
The project has produced a number of valuable results. The SwRI team fabricated and commissioned a unique, high-inlet- temperature combustion test facility. This facility is capable of reaching combustor inlet temperatures of 1,000 degrees C with an air mass flow rate in excess of 2.0 kg/sec and pressures of nearly eight times normal atmospheric pressure. The facility is equipped with a flexible and extensible instrumentation and data acquisition system for measuring temperatures, airflow, species concentrations, and static and dynamic pressures. This facility has demonstrated operation over the full temperature range and up to near-real-world turbine inlet pressures.
Using this facility, SwRI conducted preliminary flow, combustion, acceptance, endurance, and stability testing on the high-temperature combustor. The team conducted more than 50 hours of testing for this clean sheet injector design under very harsh and destructive conditions. These tests provided considerable insight to the current design as well as direction for improving the service life in future generations of the injector design. In the next phase, the team will combine a cutting-edge additive manufacturing process with advanced materials to address more challenges and meet operational standards, including a service life of 30,000 hours.
What's Next?
SwRI engineers are working with industry partners to develop a commercialization path for the technology to be ready to hit the market by 2020.
SwRI analysis indicates that CSP-hybrid systems with temperatures reaching 1,000 degrees C can dramatically lower the leveled cost of energy (LCOE) while increasing solar energy production. LCOE weighs everything that affects energy costs, from installation to maintenance, including facility costs, electricity prices, and government subsidies. Furthermore, combining natural gas and renewables in a single hybrid power plant is more economical than having two completely separate plants.
DETAIL
The SunShot Initiative is a national collaborative effort to make solar energy cost-competitive with other forms of electricity by the end of the decade.
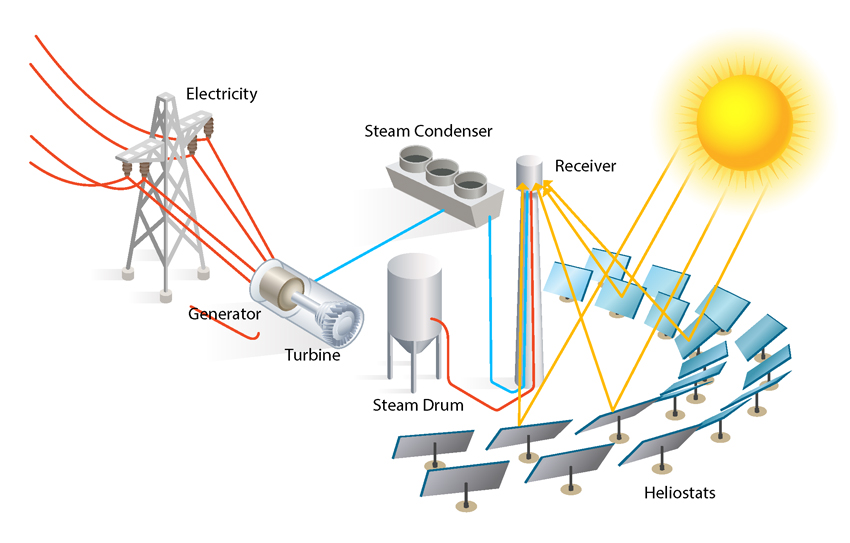
In the U.S. alone, total solar capacity exceeded 20 gigawatts (GW) in 2015.1 Most of that power is associated with photovoltaic solar, but five CSP projects totaling 1,250 MW of capacity were installed in 2014 in the desert regions of Arizona, California, and Nevada. And more are on the way.
Rapid deployment of CSP has created demand for improvements to address the unique technical challenges to operation. This has created many opportunities for SwRI scientists and engineers.
SwRI is also developing a turboexpander for supercritical CO2 power cycles in CSP plants for the DOE. Supercritical is a state of matter that puts gases and liquids under a combination of high temperature and pressure to create a working medium ideal for power-generating systems. For a commercial client, SwRI has also developed encapsulated phase-change chemicals as an energy storage solution. Tanks of encapsulated salts alternately melt and solidify to efficiently store and distribute energy from parabolic mirror-based solar plants.
1Solar Energy Industries Association
Questions about this article? Contact Tim Allison or call +1 210 522 3561.