Supplying, maintaining, updating, testing and developing the equipment that supports warfighters and military machines is a significant part of Southwest Research Institute’s research and development activity and a representative sample of the Institute’s interdisciplinary and interdivisional capabilities.
Technology Today recently brought together a panel from three technical divisions to discuss projects and processes that address SwRI’s logistical support workload.
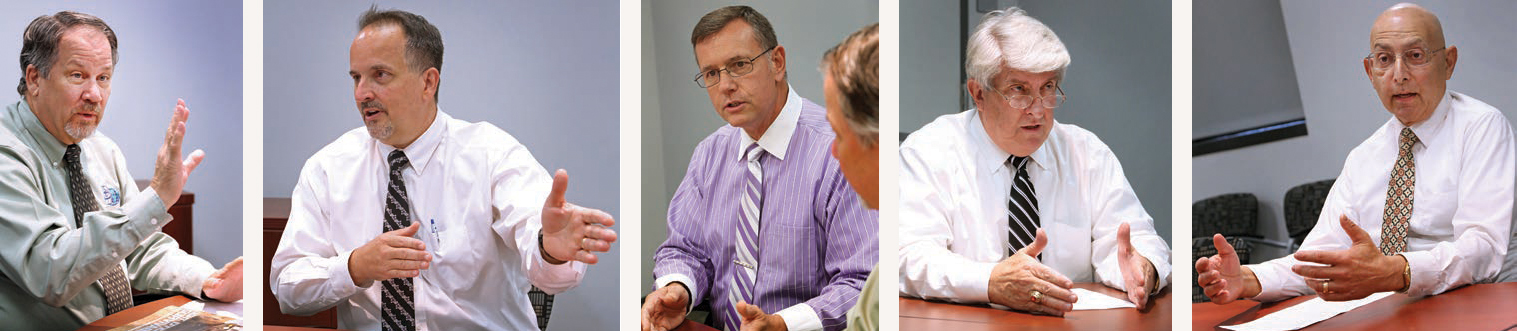
Panelists taking part in this discussion include (top row, left to right): Gary Bessee, director of the Fuels and Lubricants Technology Department and U.S. Army TARDEC Fuels and Lubricants Research Facility, Fuels and Lubricants Research Division; David A. Ogden, director of the Aerospace Engineering Department, Aerospace Electronics, Systems Engineering and Training Division; and Michael W. Stange, manager of the Aircraft Avionics Sustainment Section, Aerospace Electronics, Systems Engineering and Training Division; Dr. Kenneth E. Griffin, manager of the Aerospace Structures Section, Mechanical Engineering Division; and Michael A. Kluger, senior program manager, Fuels and Lubricants Research Division.
TT: How do you deal with age issues in logistics support?
Griffin: The mechanical engineering focus is to try to keep these older mechanical systems functioning. That’s engines, that’s the drivetrains that come off of the engines, that’s the airframe itself and the different systems that go in the airframe. If you look at the T-38, that airplane was designed in the late 1950s. They started putting together parts in the early ‘60s. Well, do you remember what you were driving in 1959? Think about trying to find a particular part for an air conditioner for a car that was built back then. We end up doing a lot of reverse engineering. We try to provide a lot of pieces that you can’t commercially find any more. It’s a broad range of different subjects, trying to keep these systems going. They’re still viable, they’re still useful. They’re just long in the tooth.
Ogden: That’s a common aspect with a lot of the aerospace that we do, too. The military has these assets, and they’ve got to keep them all running. We see that in both the Army and the Air Force. A lot of the things we’re replacing with new technology have been in use for 40 years. Transmission testing, engine testing, electronics — we’ve seen things go through generations. The electronics may have rolled over a couple of times, but the mechanical systems are still there. There are a lot of age issues there. When we’re fielding a system, we’ve got to worry about how it is going to be supported. If you buy a PC for part of a system, it’s got nine months before it’s obsolete, so what are you going to do about that? How do you give them a reliable system? We’re working a project right now for a foreign air force where we’re trying to design a system that they’ll use for 20 years, and it’s full of electronics. So the age issue is a big one.
Bessee: We’ve got the same thing on engines. You’ve got engines from the 1980s and ‘90s that don’t have the newer technologies used now, such as electronic control modules. And today you’ve got high-pressure common rail fuel-injection systems. You’ve got to take care of antiquated engines and have the lubricants work in those, but also work in these newer engines.
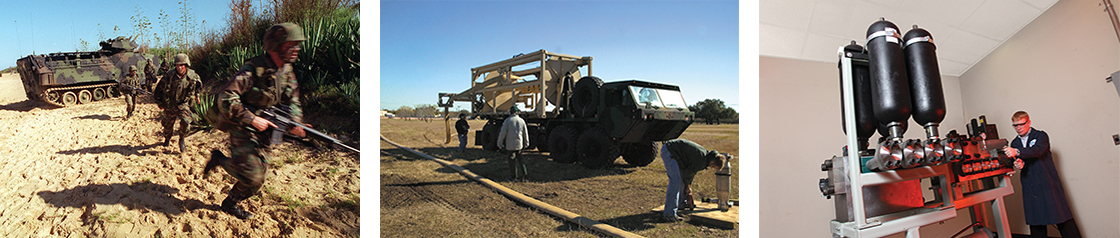
TT: How do you ensure that legacy systems meet modern standards of reliability?
Kluger: One of the most important things we do is to assure commanders and warfighters that the products they’re using in the field have absolute reliability. Toward that end, we build test stands that aggressively test components and systems that are no longer supported by the manufacturer. But the most important thing is that the warfighter should have absolute confidence that when a vehicle is used in the field it can work to that absolute upper limit, of the capability for which it was designed. Building these test stands is extremely challenging because they involve a multitude of disciplines such as mechanical, electrical, pneumatic, hydraulic, instrumentation and data acquisition and controls. The challenge is making it all fit within the dynamics of a repair depot. Beyond that, we also build test stands for the engineering centers that develop the next generation of vehicles.
Bessee: Another area is these alternative fuels that are coming into use. We have bio-diesels for the diesel area, and now there are bio-aviation fuels. We need to capitalize on alternative fuels and on reducing the dependence on foreign oil, but we’ve got to make sure that they will work in diesel engines when they were really designed for aviation. For example, bio-aviation fuels don’t even measure a cetane number, yet they’ll be put into a compression-ignition engine, for which a fuel quality evaluation requires a cetane number. We have to accommodate those two standards somehow, because we have to verify these new fuels will operate in a transport, combat or earth-moving vehicle.
Griffin: We’re also being asked to carry some of these devices much longer than they were originally planned for. The airframes that we’re flying — the A-10 and T-38, for example — were tested to a certain expected lifetime. Now they’re trying to go longer, sometimes by a factor of two or even more. We end up doing design engineering, trying to work up pieces and fixes so these older systems can continue to function. We have to build test stands that to some degree are replications of what they had to build when the system was originally accepted, to carry the design life to these extra lengths. And it’s not trivial.
Stange: There are big challenges behind a lot of the things we do. The A-10, when it was originally built, was strictly an analog aircraft. It had very few onboard digital avionics systems, other than the instrumentation, which is easy to change out. We’ve taken it into the next decade, where now everything is digital. Taking those older airframes into what’s considered the Digital Age is always a challenge. With the A-10 specifically, we’ve gone from basically no displays to color displays in the cockpit with satellite imagery. That means the pilot can get information back from other aircraft so he understands what’s going on on the battlefield. If he needs to, he can call in support without even having to talk to anybody.
Ogden: Also, we’ve been working with the Air Force on jet engines. They have engines that have been around for decades, just like these other things we’ve been talking about. Adding sensors to those legacy systems is very expensive, so we’ve been working on statistical analysis of the data that comes off their existing systems. We’re using what they already have to get a better idea of what the condition of their system is. This is part of our nSPCT™ program. Condition-based maintenance technology is one of our thrusts.
Kluger: One of the services SwRI provides is filling in where a lot of the original equipment manufacturers have stepped away. Taking test stands as an example, you’re talking about systems that are 20, 30, 40 years old. Repair depots are faced with a tremendous challenge: first, their equipment may have been modified over the years without being properly documented, or the original documentation may not even exist. What SwRI does, is to provide mechanical, electrical and software engineers who can replicate these systems and their functionality. There are tremendous challenges associated with doing this: for example, you have to understand power flows, the component function being replaced which many times no longer exists and you have to provide equivalent functionality. We retrace electrical circuits and determine voltage, currents, capacitance, inductance and impedance values. We work to understand what the original design intent was for the system, while simultaneously meeting the requirements of very complex, unusual and demanding systems. In addition, we address the operating speeds and elevated power levels associated with military equipment. So there’s a technical challenge in meeting those operational requirements.
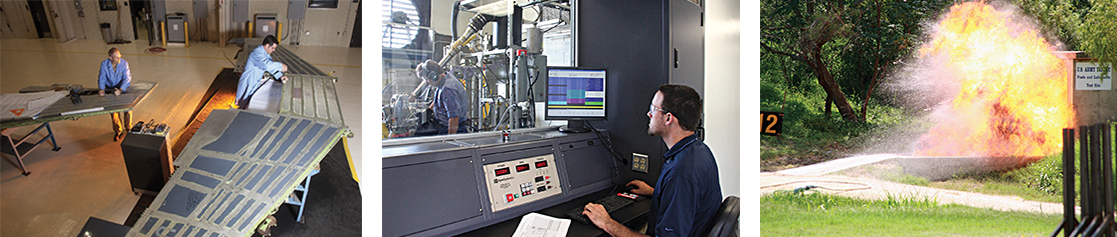
TT: If anyone has a particularly rewarding project that their group was involved in, talk a little about that.
Bessee: In the Army Lab, there are several of them. David (Ogden) and I had one, RIFTS, for Rapidly Installed Fluid Transfer System, which was a great idea. [Editor’s note: RIFTS was a reel-type, flexible pipeline, including pumps and leak-detection equipment that could transfer fuel from a rear-area supply depot and refuel combat vehicles near the front.] It was needed — it’s still needed — but the military sponsor had to drop it due to the war effort and lack of funding. There is one example where we are stretching the technologies, stretching the capabilities, by coming up with new materials.
Stange: The A-10 is one of those pieces of equipment taken from a ‘70s to ‘60s-era technology base that is still being used on the battlefield in today’s environment. One challenge we faced in mechanical and electrical engineering was to install a capability called “Precision Engagement,” to bring into the field something that pilots could use to help the Army on the ground. When I talked to pilots who had flown the aircraft on the battlefield, both prior to Precision Engagement and today, they said that prior to Precision Engagement they’d be flying at night and the Army would say, "Hey, I need help, we are under attack." And the pilot would say, "I can’t see where my enemy is, other than tracer rounds, and if the enemy is not shooting at you, I can’t shoot." Precision Engagement infrared technology came along and changed that, and added various new displays in the cockpit that Dave (Ogden) alluded to. Now, pilots can view the battlefield at night. Another technology that came along was the moving map. This application allows the pilots to see their location on a map display driven by GPS positioning.
A pilot whom I have known for quite a few years told me about an event that took place on a cloudy day. The A-10s were flying above the clouds at about 22,000 feet. They couldn’t see anything below them, so they loitered for three hours or so in their patrol area. Before heading back to base they started getting calls from troops that were under attack while trying to move through a canyon about 20,000 feet below them. The pilots couldn’t see to get down there. They had two choices: Trust what the aircraft moving map told them about their position, or else fly all the way back to base, go low-level to get beneath the clouds and then go into the canyon and find the troops, which would have taken about 40 minutes. They chose to trust the technology, and they came down through the clouds knowing where the troops were in relation to the enemies from the location on the moving-map coordinates. The pilot had his targeting pod ready, so he could evaluate the situation. He was able to start his gun run before he even got out of the cloud base, and was able to save the troops. It gives me a good feeling and I am very proud that SwRI has this level of engineering experience to have a direct impact on that type of ability.
Kluger: One of our reverse-engineering projects has been particularly gratifying because it was urgently needed by our military client while also being greatly challenging from a technical standpoint. The project involved a transmission valve body test stand. It consisted of an extensive grouping of hydraulic circuitry, mechanical movements, and control functions for which no documentation existed. This was a critical component within the military maintenance depots. It was even more challenging because much of the pass/fail test information was interdependent and buried deeply within software. We were able to overcome these problems and replicate the test stand for our client. It took a combination of capabilities and skillsets that reside here at SwRI, such as well-defined engineering problem-solving skills, multidisciplinary project teams, and creative thinking along with a foundation and understanding of equipment and systems.
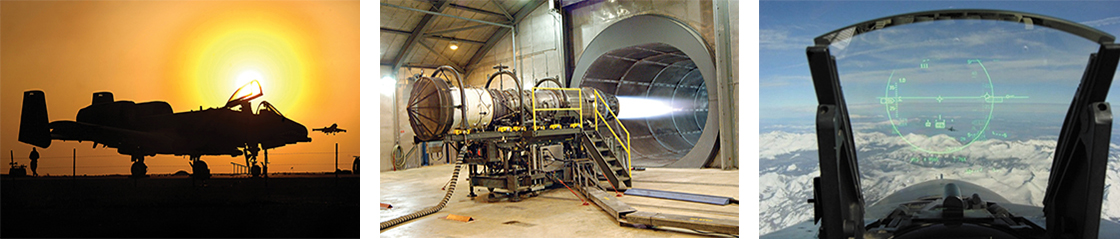
TT: What about SwRI’s collaborative, multidisciplinary efforts?
Griffin: The diversity of this place can really bail you out in situations that you didn’t calculate. You can run into materials that surprise you, or materials not normally used in the systems you’re working with. But chances are somebody here at SwRI has been working with it, and if you ask them they can tell you some basic characteristics and things to look for. You don’t have to go off the grounds. You can talk to a guy who, in five minutes, can save your project.
Bessee: A perfect example of that is that Dave's (Ogden’s) group has a large B-52 program at Tinker AFB. They’re doing all the hardware, design and fixing for everything they have up there. So when we need to know simple things related to B-52s, like what hydraulic oil do we use, where do we get it, we may not know anything about it. But that division deals with it every day. It’s just a matter of knowing what resources we have, and going to the right people.
Ogden: We’ve been able to tap people from all of the other divisions at one time or another. We’re able to use the invested capital and the expertise those guys have, so we don’t have to invest in our own. When we did our multivariate statistical research program and developed our nSPCT analysis tool, we used Dr. Robert Mason, who is a nationally recognized expert in those kinds of statistics. We were able to take some of the technology he’s been working with, automate it and create something that’s useful in our business area.
Bessee: We’ve even gone and looked at new technologies. One of the big things in the chemistry world is called 2DGC/MS, or two-dimensional gas-chromatography/mass-spectrometry. It’s brand-new technology, and it requires very expensive equipment. We were looking at buying it for our use, and then we found out the chemistry group already had one. We assumed they were fully utilizing it for pharmaceutical testing and found out we could use it for our purposes. We acquired the software and a removable hard drive, and now we ask them to run tests for us and give us the analysis. We drop it in the hard drive, and our chemists go in and reduce all the data. We’re still the experts, and we didn’t have to pay $400,000 for a piece of equipment, then have two of them sitting around partially utilized — now it’s being efficiently utilized. We’ve got the capability of leveraging the other division’s knowledge of chemistry, and the 2DGC/MS. It expands the Institute’s capabilities.
Kluger: We’ve done a couple of multidivisional projects between the fuels and lubricants research and aerospace groups such as helicopter component repair studies where we looked at depot processes and recommended how their work flows and process equipment could be improved... Some of these transmissions can be six or eight feet high and four or five feet in diameter, passing hundreds of thousands of foot-pounds of torque through them. We were trying to see how repair depots could improve their repair processes, including the materials they were using in order to improve their throughput times and costs in order to deliver a better product to the warfighter.
Ogden: Another new technology we’re working on is replacing the testing technology they’ve been using to test helicopter jet engines at an Army depot. We’re taking out a water-brake system, which had an MTBF (mean time between failure) of about 100 to 200 hours. They spend about $1 million a year to keep their water brakes running. We’re putting in an electric dynamometer using a high-speed, 2.5-megawatt motor as the load. It’s a good example of new technology, and this is the first application of its kind for a motor of that size and speed.
We’re putting in four right now, and they plan to build brand-new test cells over the next decade that this technology would transition over to. Plus, there are other potential customers around the world — other military depots, and also commercial applications.
Questions about this article? Contact Technology Today Editor SwRI Solutions.