Background
Simultaneous demands for improved efficiency, reduced emissions, and reduced weight have pushed many engine components (specifically cylinder heads) up against the limits of design, materials, and manufacturing capabilities. Additive manufacturing (AM) offers the potential of new design approaches to these issues. However, complex parts such as cylinder heads produced to date via AM have failed to demonstrate the technology benefits, have shown minimal emphasis on part functionality, and are typically made from aluminum which is not suitable for heavy duty applications.
The primary objective of the research was to investigate and apply a unique technology to powertrain applications in addressing conflicting constraints of a cylinder head: to greatly advance load capability, reduce thermal mass, control heat transfer, and optimize function. This work helps propel SwRI and Powertrain Engineering to a leading role in demonstrating and optimizing AM technology in engines.
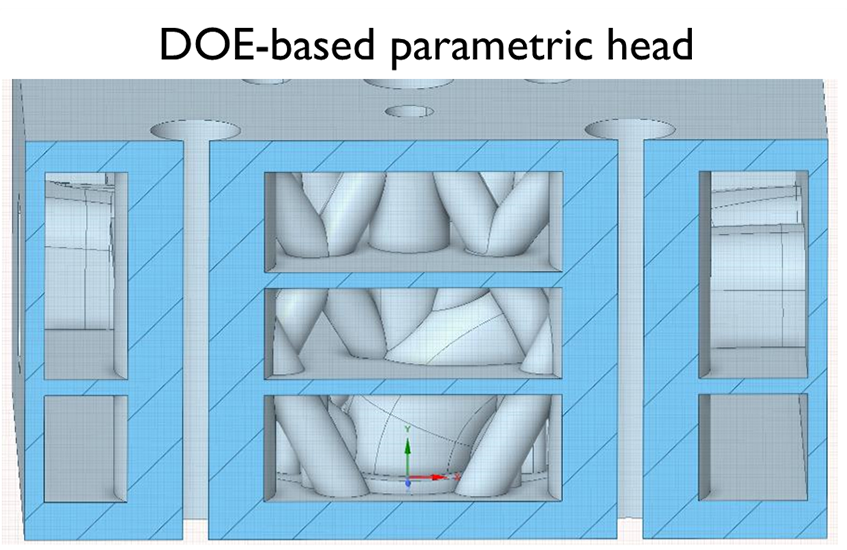
Figure 1: A DOE-based analysis allows engineers to quickly assess effects and interactions of different base designs.
Approach
This project aimed to design an advanced cylinder head for ultra-high PCP capability by exploring two design paths: DOE and Topology Optimization. Each path first explored the structural requirements of the cylinder head, including combustion seal deflection and stress response to pressure loading via FEA. Cooling features were then evaluated though iterations of cooling flow CFD analysis.
The first path was an engineering-driven design based on parametric DOE design analysis. Using 2D and 3D feature approximations, top-ranking designs that work to prevent fire deck deflection were modeled in a basic 3D head geometry consisting only of ports, head bolt bosses, and mid deck features. In total, 10 design features were investigated for their effects on deflection (and therefore stress) using a Resolution V fractional factorial design to reduce the DOE down to a manageable 128 models. These models were analyzed in a structural FEA solution, and a final selection of the best design features were integrated into an initial cylinder head design.
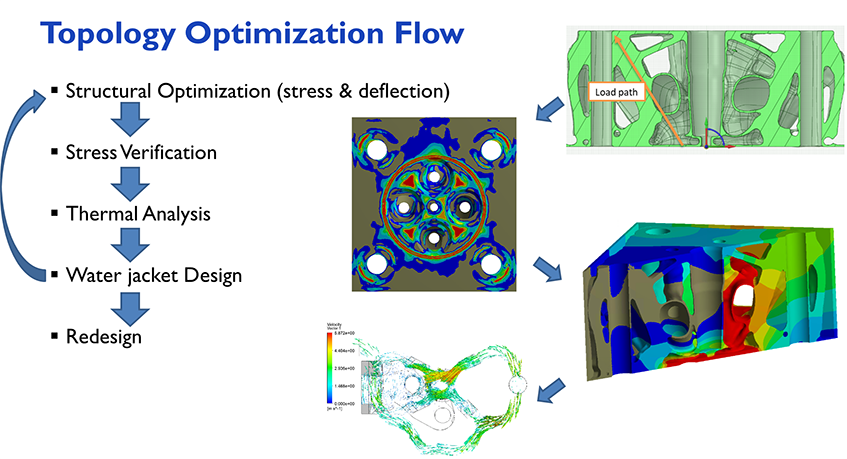
Figure 2: The IR produced a topology optimization work flow which will be used in future projects that utilize AM, but can also be used to better understand load paths for traditional manufacturing.
The second path is a topology optimization approach with Design for AM tools. A solidified cylinder head (with ports and head bolt holes removed) was constrained in FEA using assembly and cylinder pressure boundary conditions, and an initial structural solution was obtained. Iterative and parallel topology optimization runs focused on deflection and stress constraints relative to the goal of material minimization. Design refinement was accomplished primarily through smoothing and shrinkwrapping via mesh processing tools.
Accomplishments
DOE simulations revealed different features were most influential in preventing cylinder head fire deck deflection when AM-based features are available compared using sand cast-only features in the design. A topology optimization path was introduced and refined that allowed input of several important cylinder head parameters such as component stress, fire deck deflection, and head bolt load. To date, thermal requirements cannot be combined into a single-case structural optimization.
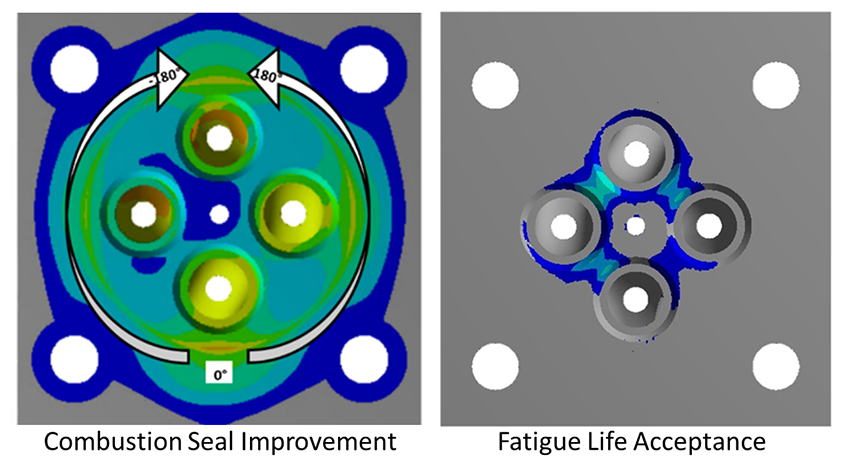
Figure 3: Results of the study include a single cylinder head design that satisfies major use criteria – sealing the combustion chamber and providing durability.
Surface roughness is a strong influencer of crack propagation and fatigue strength, and uncertainties in printed materials can affect cylinder head strength. Background research and AM specimen data were evaluated to determine surface roughness characteristics for a steel AM component. The sensitivity was studied in a thermo-mechanical FEA and fatigue assessment. Results show that features made possible through AM techniques can allow the design of a donor cylinder head to be improved from 230 bar peak cylinder pressure to 300 bar and beyond, an increase of at least 30%. The research did not include scope to determine the maximum possible pressure the cylinder head could withstand, which will exceed the 300-bar assessment of this work.