To craft innovations in 2019 and beyond, Southwest Research Institute maintains extensive fabrication facilities and capabilities to create the custom components and fixtures needed for our science and applied engineering programs, from deep sea to deep space. Our master machinists and craftspeople create everything from micro-sized parts to large integrated systems using materials such as titanium, alloys and ceramics. State-of-the-art fabrication equipment includes computer-aided design (CAD) and computer numerical controlled (CNC) turning, milling and machining devices, as well as 3D printers capable of creating complex plastic and metal parts.
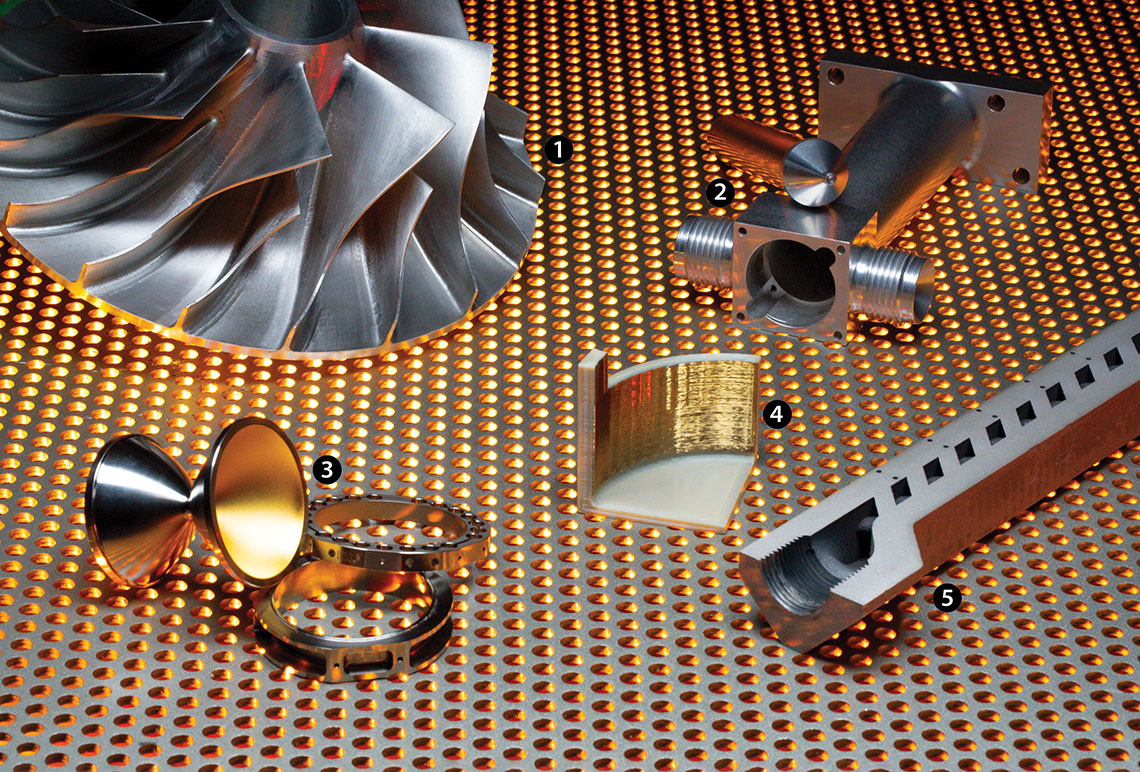
SwRI’s main machine shop created this small-scale impeller to evaluate how inlet flows associated with pipe elbows affect the performance of centrifugal compressors such as those found in natural gas compressor stations.
For decades, SwRI has developed and fabricated hundreds of shipboard direction-finding antennas for the U.S. Navy and allies. These complex, rugged devices are built from precise components fabricated in SwRI’s main machine shop from aluminum alloys.
SwRI’s model shop made these reflectron ring electrodes and shaped ion buncher, parts of SwRI’s novel MASPEX instrument. The state-of-the-art mass spectrometer will fly on NASA’s Europa Clipper mission, collecting samples of the tenuous atmosphere around Jupiter’s moon Europa.
SwRI 3D printed this electrostatic analyzer component from a heat-resistant, high-strength resin. Using a magnetron sputtering technique, engineers then coated the component with gold, which allows the instrument to focus or “filter” the range of particles targeted for detection and measurement in space.
SwRI’s selective laser melting device produces complex metal components using additive manufacturing technology. The 3D printing device created novel liquid cooling jackets to investigate whether intricate internal geographies (shown in this cross section) could enhance cooling of modern internal combustion engines.