The transportation sector generates the largest share of greenhouse gas emissions in the United States, primarily from burning fossil fuels for cars, trucks, ships, trains and planes.
To combat this, the passenger vehicle industry is seeing explosive growth in electrified powertrains. Congressional incentives to build in North America are driving new manufacturing facilities and charging infrastructure.
Electric powertrains offer several operational advantages over traditional powertrains, but they also present several unique challenges, notably a steep sticker price and what’s known as range anxiety — concern that an EV will run out of power before reaching its destination or a suitable charging point.
But what about heavy-duty vehicles? These large trucks and heavy equipment offer perhaps even greater carbon reduction opportunities while facing the same challenges in price and range, but at a larger scale.
Consider that about 28,000 large mine hauling trucks around the world consume over six billion gallons of diesel every year. Together, these mining trucks emit 68 million tons of carbon dioxide (CO2) annually, roughly equaling the total greenhouse gas footprint of Finland or New Zealand. A single truck could burn 250,000 gallons of fuel per year and could not only produce more than 2,400 tons of CO2 — compared to about 1,500 Prius hybrids — but also emit pollutants such as NOx and ultrafine particulates.
Market pressures are driving the heavy machinery industry, which includes rail and marine applications, toward net-zero emissions goals. Consumer product companies have set goals to reach zero emissions by 2050, which is cascading expectations to the entire supply chain, including the raw materials market. Regulatory and financial sectors are driving investor-led initiatives to characterize and support corporate actions to combat climate change, so investors know they are supporting greenhouse gas reductions. For example, the Securities and Exchange Commission has launched a task force to regulate the standardization of climate-related disclosures.
Southwest Research Institute has more than 40 years of experience developing clean emissions strategies for diesel engines, mainly pursuing technology to allow vehicles to meet regulatory goals. Today, market forces are driving new initiatives, and regulatory entities have enlisted SwRI to evaluate the availability and readiness of technology to meet those demands.
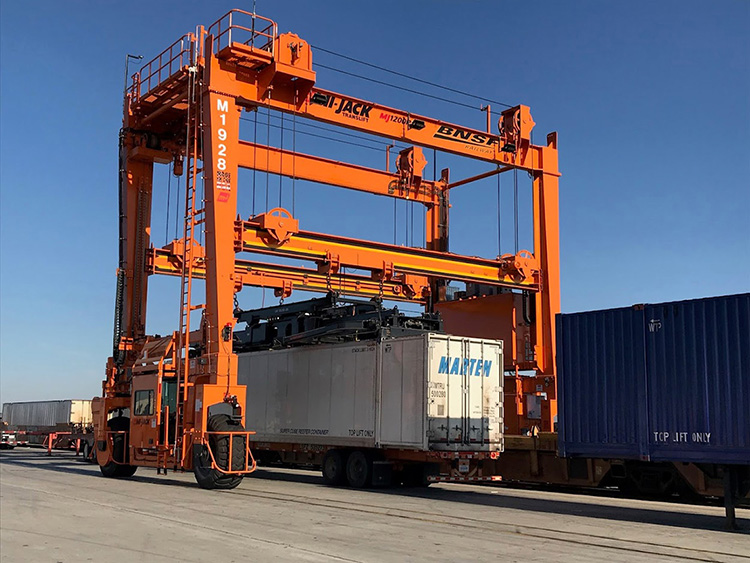
SwRI teams compared electrified cargo-handling equipment, such as this hybrid-electric gantry crane, to their diesel-hydraulic counterparts for CARB’s near-zero freight initiative.
Cargo Handlers
SwRI worked on the California Air Resources Board Zero and Near-Zero Emission Freight Facility program at BNSF San Bernadino Intermodal Railyard. Over six months, the team studied the electrification of drayage trucks, forklifts, gantry cranes and locomotives, evaluating them side-by-side with their diesel engine counterpart, to determine how effectively they moved freight.
DETAIL
Data loggers are electronic devices that automatically monitor and record operational parameters over time, allowing conditions to be measured, documented, analyzed and validated. Sensors detect information, which is stored on a computer for analysis.
SwRI used data loggers to monitor a battery-electric locomotive, a hybrid crane, an electric side pick cargo handler and an electric Class 8 drayage truck, as well as their conventional diesel-powered counterparts. Data collected included energy consumption, refueling/recharging times, peak electricity rates and missions for the diesel-powered equipment. At the project’s peak, 10 dataloggers generated almost one million rows of data each day. SwRI’s data analytics software then distilled relevant information to help a commercial client optimize their electrification plans for cargo-handling equipment in California.
Recharge time is also a critical operational constraint for cargo handling equipment because most of these systems operate 24/7. Having to take systems offline and move to charging stations affects freight efficiency.
Mining Electrification
The challenge is the same for electrifying equipment for mining operations, on a much larger scale. Mining trucks and locomotives are propelled by electric traction motors. SwRI is studying the effectiveness of replacing the diesel engine coupled to a generator to provide electricity via batteries. The mining industry is increasing its investment in high-efficiency energy conversion and electrification, realizing more efficient operations burn less fuel and produce fewer emissions. Companies are analyzing different value propositions and what types of electrification make sense, creating a net benefit to the operations.
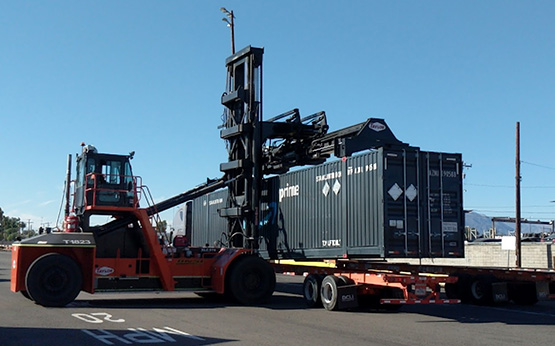
SwRI used dataloggers to monitor this electric side pick cargo handler. The project collected almost a million rows of data each day for analysis to help a commercial client optimize its electrification plans for freight equipment.
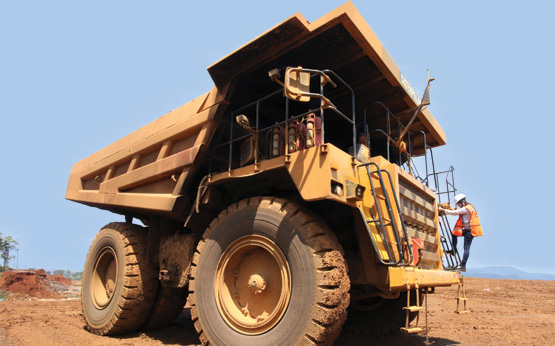
Courtesy of CC by SA 4.0/Mirwanto Muda
Mine hauling trucks are enormous, measuring up to 65 feet long and weighing about 500 tons, some 260 times heavier than a passenger car.
The usage, lifecycle and safety requirements of mining trucks are very different from passenger cars based on size alone. The scale of these vehicles to the typical EV creates very different operational demands. The largest dump trucks are over 65 feet long and can haul 450 tons of materials in a load at a fuel efficiency of 5.5 gallons of diesel per mile. They weigh 500 tons, some 260 times heavier than a passenger car.
The failure mode of a piece of equipment that costs more than $5 million is also quite different than the failure profile of a passenger car, which focuses on passenger safety over preserving the capital equipment investment.
Enabling Technologies
To recoup the significant capital costs for mining equipment, operations must run 24 hours a day. SwRI is studying the various business models addressing how to cost-effectively electrify these monster trucks. For instance, downtime for recharging results in a 70% efficiency penalty. However, swapping out batteries results in a value proposition better than its diesel engine counterpart.
Future solutions under evaluation include the integration of “trolley” lines. When delivering raw ore to a locomotive or a ship, mining vehicles traverse a regular route, offering the possibility of charging batteries dynamically as they haul materials. Installing electric charging lines into the infrastructure allows an enterprise to increase these value propositions by continuously operating 24/7 through dynamic charging, eliminating downtime and range anxiety.
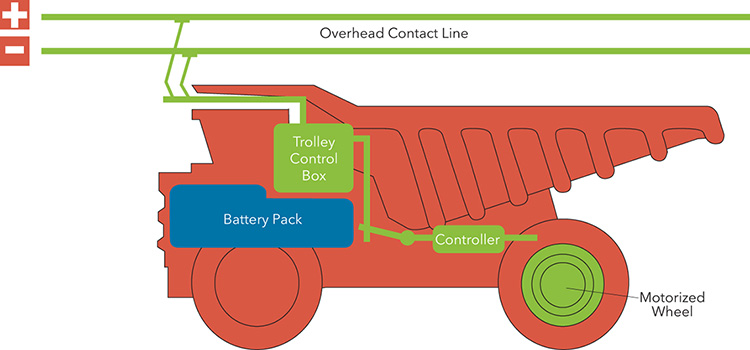
To electrify giant mining machinery, SwRI considered adding trolley lines to selected segments of the delivery route to charge onboard battery packs while trucks are in service, allowing the haulers to operate 24/7.
Battery Testing
Engineers consider critical situations on a massive scale, including unique usage, lifecycle and safety requirements. Electric batteries for heavy-duty machinery must meet rigorous demands and extreme safety requirements to enable sustainable operations. Key operational and lifecycle parameters include 15 times the power and 20 times the energy requirement of passenger car applications. Mining trucks encounter comparatively much greater mechanical abuse, shock and vibration than a typical passenger vehicle experiences during a drive to work.
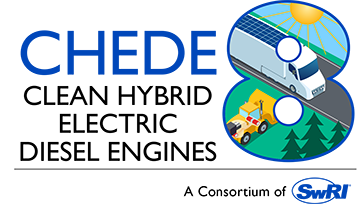
For more than 28 years, SwRI has led the industry’s longest running diesel research consortium, the Clean Hybrid Electric Diesel Engine (CHEDE-8). The joint industry program pursues the world’s most efficient powertrain solutions to meet the needs of the industry 10-plus years into the future. The current program includes a focus on hybrid heavy-duty diesel engines and developing technologies to exceed future fuel economy and emissions regulations through electrified powertrains. Off-road and vocational applications offer significant opportunities to maximize the use of high-power density engines with highly efficient motor and battery systems.
Researchers analyzed electrical abuse associated with large power demands and the thermal profile created while delivering megawatts of power over many hours. When heat builds, thermal stresses can lead to battery failures. SwRI is using internal research funding to understand these critical failure modes, developing techniques to simulate and physically test thermal, structural and crash failures.
SwRI has invested a tremendous amount of capital in its battery test laboratory. The facility can simulate multiple environments, altitudes, and shake and vibration scenarios. To address battery safety, engineers have designed tests to evaluate different materials between the cells, evaluating both the structural and energy propagation effects through the pack, as well as how heat propagates between cells. If a battery cell fails, it’s important to develop techniques to limit the impact on the rest of the vehicle.
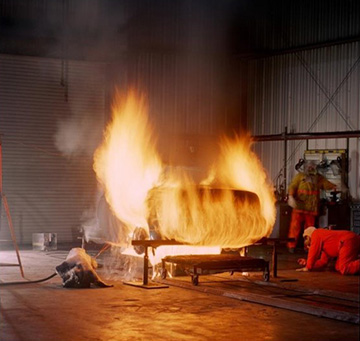
Fire specialists expose fully charged electric vehicle batteries to gasoline pool fires.
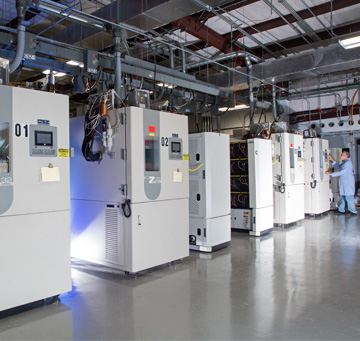
Comprehensive test facilities allow all battery mechanical, electrical, thermal and performance testing to be conducted in-house at a single location.
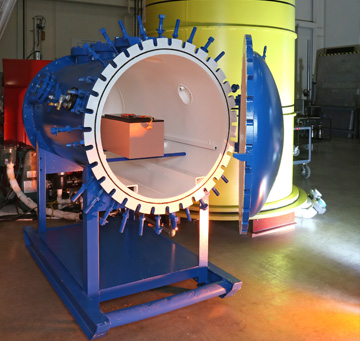
SwRI battery test facilities include altitude chambers.
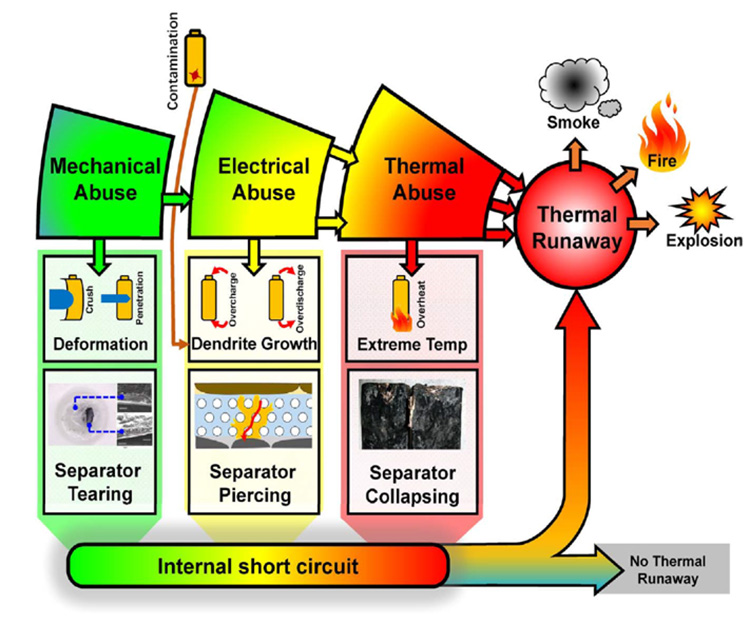
SwRI has developed test setups to evaluate and characterize mechanical, electrical and thermal abuse for battery technology.
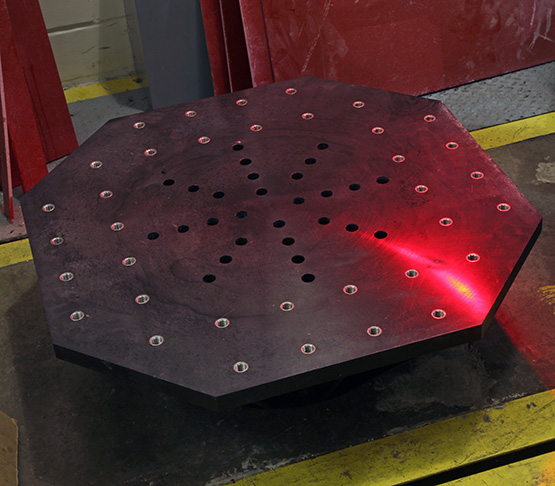
Shaker tables allow SwRI to assess the exceptional vibration that batteries for large mining vehicles would experience.

SwRI developed equipment to crush test whole battery packs (pictured) as well as fixtures to crush test individual cells.
In SwRI’s fire technology facilities, a complete vehicle battery pack can be immersed in flames to identify its point of failure. Structural deformation, such as could occur in a crash, can be simulated at crush test facilities for individual cells and full packs. SwRI ballistics experts evaluate battery response to projectiles impinging the pack and how to mitigate damage in these scenarios. Electromagnetic interference and compatibility are evaluated in SwRI anechoic chambers.
SwRI’s multidisciplinary expertise brings fresh perspectives and a range of capabilities to develop innovative EV solutions. The Institute remains committed to helping the heavy equipment industry find creative, cost-effective techniques to reduce fuel usage, while generating fewer exhaust emissions.
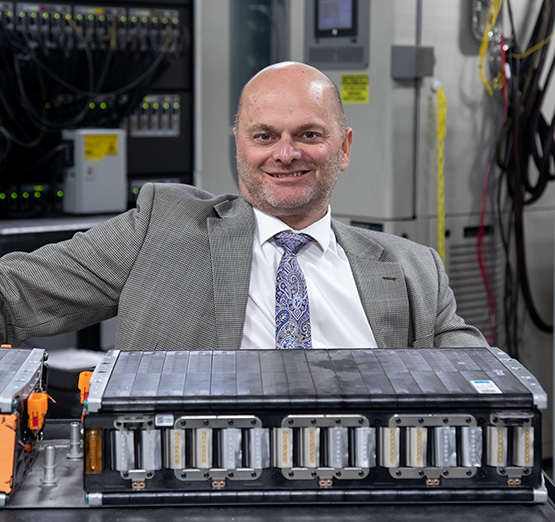
ABOUT THE AUTHOR
Chris Hennessy directs the Powertrain Design and Development Department. He has over 25 years of experience in research, advanced concepts, development, validation and certification of powertrain systems for the light- and heavy-duty markets.
Questions about this story or Powertrain Design, Analysis & Simulation? Contact Chris Hennessy at +1 210 522 3079.