Background
In the United States, the transportation sector is responsible for the consumption of 28 percent of the total energy produced every year. Based on 2004 data, ground vehicles (automobiles, light trucks, and other heavy-duty vehicles) consume 77 percent of all oil used in all modes of transportation in the U.S. In order to double the fuel efficiency of new vehicles in the U.S. by 2030, the focus has shifted towards aerodynamic vehicle design optimization. Large freight transport trucks and trailers (class 8 tractor-trailers) account for roughly 15 percent of all petroleum consumption in the U.S., or about 1.8 million barrels per day.
The potential for fuel and cost savings is huge: a 12 percent reduction in fuel use across the national fleet would save 3.3 billion gallons of diesel per year and prevent 28 million tons of CO2 emissions. One way to reduce greenhouse gas emissions is to design more fuel-efficient freight vehicles. In general, there are two interconnected, yet independent, approaches to reduce fuel consumption. The first approach addresses engine design, incorporating features such as engine downsizing and powertrain integration to improve efficiency. The second approach addresses design of the vehicle’s body to improve efficiency.
Improved aerodynamic design could substantially reduce both form (pressure) and skin friction drag on the vehicle, reducing the amount of fuel required to propel the vehicle. In reality, a freight vehicle is expected to operate over a wider range of speeds. One way to achieve fuel efficiency over a wider range of operating conditions is to implement active or passive flow control (PFC) surfaces on the vehicle body.
Active Flow Control (AFC) is being touted as an effective method to develop the technology of flow manipulation in many high-speed flow applications, including air vehicles. The potential benefits of AFC include improved performance and environmental compliance. In an effort to comply with stringent environmental regulations, current research efforts are focusing on AFC devices to suppress aerodynamic drag. AFC can result in a 9 to 16 percent reduction in the computed drag coefficient (depending on the flow Reynolds number). A 15 percent reduction in drag is equivalent to about 5 percent in fuel savings.
Approach
The broad objective of the proposal was to design and evaluate AFC strategies to reduce aerodynamic drag and improve the fuel efficiency of trucks using computational fluid dynamics (CFD) numerical simulations using ANSYS Fluent. The objectives of this study were achieved by simulating several representative benchmark problems with and without suppression. The suppression device is modeled using a suitable boundary condition in the main flow field. The project objectives were accomplished through the following steps:
- Identifying the basic aerodynamic drag generation mechanism in heavy-duty vehicles undergoing high-speed flows
- Modeling of actuators through boundary conditions
- Investigating the effects of the flow actuator in suppressing aerodynamic drag
The figures presented below represent CFD simulations of baseline and AFC case for an Ahmed body. This study examines the use of active flow control devices at the rear of the 25-deg Ahmed model to reduce drag by controlling an unsteady wake. Representative figures are shown for pressure contours for the baseline case and velocity vectors for the baseline as well as the AFC case. Table 1 shows the reduction in Cd for both steady and unsteady blowing AFC. AFC achieves significant reduction in Cd values over the baseline simulations.
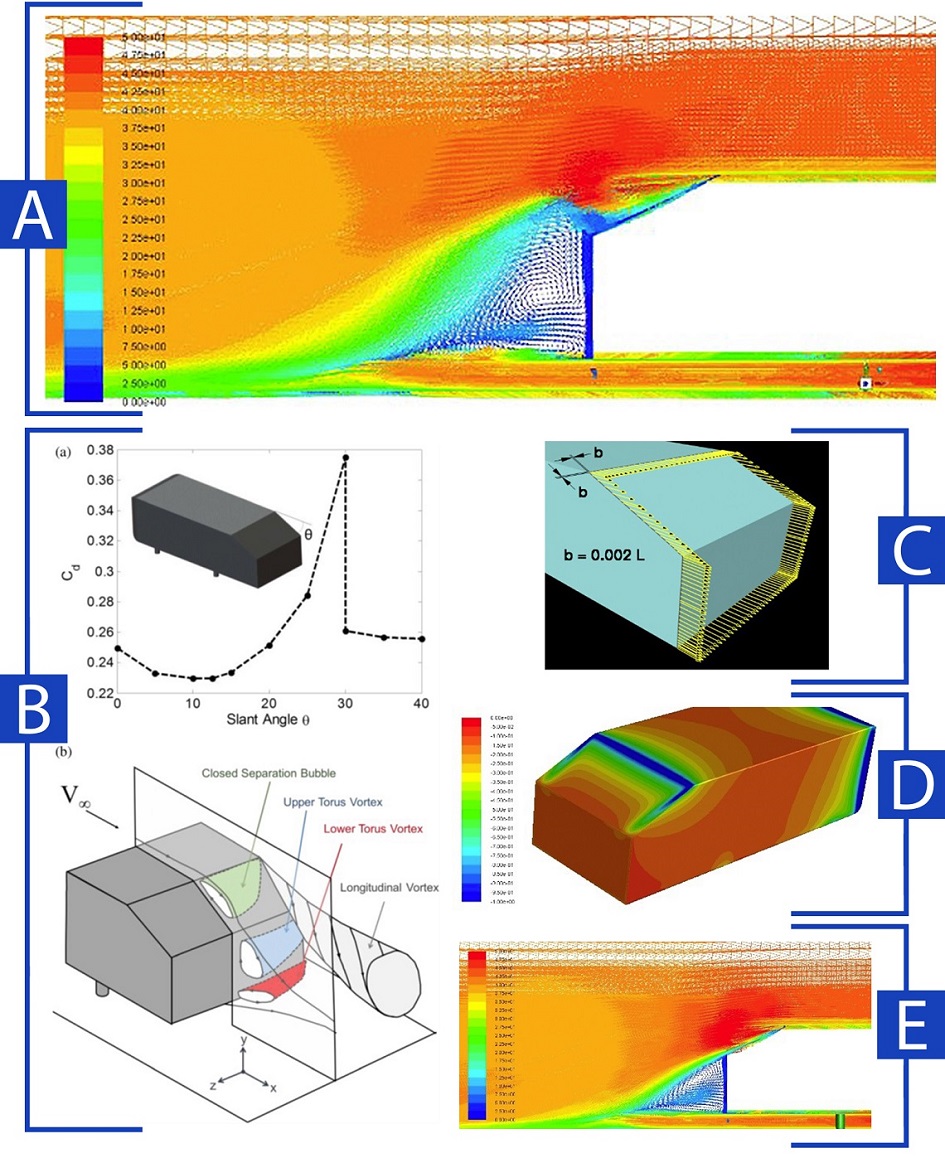
TABLE 1. BASELINE VERSUS AFC CD FOR AHMED BODY AFC.
Velocity | Computed Cd (Baseline) | Computed Cd (AFC steady blowing) | % Decrease | Computed Cd (AFC unsteady blowing) | % Decrease |
---|---|---|---|---|---|
40 m/s | 0.295 | 0.2745 | 7.4 | 0.273 | 8 |
Accomplishments
A computational method for active flow control (AFC) and efficient aerodynamic simulations over trucks have been developed and validated in the internal research and development project. The methods have been applied to three geometries and the effective reduction in aerodynamic drag through this AFC method has been quantified in this project. The broad objective of the proposal was to design and evaluate AFC strategies to reduce aerodynamic drag and improve the fuel efficiency of trucks using computational fluid dynamics (CFD) numerical simulations. The objectives of this study were achieved by simulating several representative benchmark problems with and without suppression.
The suppression device is modeled using a suitable boundary condition in the main flow field. Both steady and unsteady injection resulted in reduction of aerodynamic drag. Important lessons were learned from these simulations related to computational grid and turbulence models that will be applied in future simulations of such flows. The effectiveness of AFC mechanisms in lowering aerodynamic drag has been explored and quantified in the proposed research. This project was the first step towards developing the institute capability in external body aerodynamics and flow control research for automobiles.