Background
The focus of this work is to maximize net fuel economy and greenhouse gas improvement by considering lean-burn operation with Dedicated-Exhaust Gas Recirculation (D-EGR™). D-EGR leverages in-cylinder fuel reforming to generate exhaust gas recirculation (EGR) that is high in H2 and CO. The reformate-rich EGR enables the engine to operate with 25 percent or greater EGR, even while lean. The high dilution from both EGR and air decreases combustion temperatures, and thus engine-out NOx. Although significant NOx reduction is expected, lean aftertreatment is still required to meet emissions regulations. The objective of the project is to quantify the net fuel economy improvement with a D-EGR enabled lean-burn versus a current production, non-EGR lean-burn strategy. Greenhouse gas regulations are becoming more stringent and it is imperative that the automotive industry keep pace with these regulations. Lean-burn gasoline combustion is an attractive strategy to improve thermal efficiency and reduce CO2 emissions. Widespread use of this strategy is limited by the aftertreatment required for NOx reduction to meet criteria pollutant emissions regulations, specifically NOx. Three-way catalysts, common on stoichiometric engines, require periodic and frequent rich operation to reduce NOx, so they are not feasible for a lean-burn strategy. Thus, lean-burn engines use alternative NOx-reduction aftertreatment, which can require frequent regeneration with excess fuel. The fuel consumption penalty associated with regeneration offsets some of the greenhouse gas improvement from lean-burn combustion.
Approach
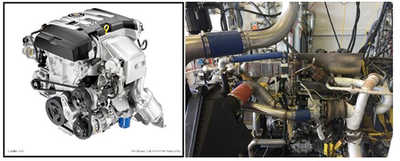
A GM 2.0 L LHU engine (Figure 1) is operated, configured for D-EGR operation, to achieve conditions for optimal fuel economy and the lowest engine-out emissions. Also, the engine-out gas stream composition is analyzed for the next phase of the project. In the next phase, the gas stream composition data from Phase 1 will be utilized to create a representative gas mix. The Universal Synthetic Gas Reactor (USGR®) system testing will include light-off tests to understand the effectiveness of the LNT and the LNT + SCR for NOx conversion and hydrocarbon reduction. Finally, strategies for opportunistic purge of the emission control system based on the USGR results will be developed for the next phase. In the final phase, vehicle simulation over three standard drive cycles — FTP-75, WLTC, and HWFET — will be conducted. The optimum aftertreatment system determined will be evaluated on the GM engine.
Accomplishments
We are in the process of completing Phase 1 of the project. The lean calibrations have been completed and we are conducting regeneration points on the GM engine. The engine has better efficiency when operated lean and the engine-out emissions are not significantly different from the baseline. There are low load operating points that provide minimal benefit to engine efficiency and, as expected, provide an excellent opportunity to regenerate the lean NOx trap catalyst. The results generated thus far are promising to smoothly transition into Phase 2 wherein we will test the aftertreatment system using USGR.