Background
An internally cooled radial turbine will be needed within the next five years to keep up with the trend in the power generation industry to increase both the efficiency and the modularity of power production. Specifically, a cooled radial turbine will be needed for supercritical CO2 (sCO2) power cycles, power cycles utilizing oxy-combustion, and conventional generation systems. Internally cooled radial turbines have been successfully designed, manufactured, and tested in the past. However, conventional manufacturing methods are difficult to apply to a radial impeller in a cost-effective manner. The conventional manufacturing method is an investment cast process using a ceramic core to create internal passages. This approach has been developed for axial gas turbines and is a low-risk manufacturing approach for axial blades. For radial impellers, however, the impeller blades and hub are typically manufactured from a single piece of material. Therefore, if one blade casting has an error, the entire part must be thrown away. By including ceramic cores in the casting process of an entire radial impeller, there is a risk of core misalignment or wall breakout for any of the cores in the casting.
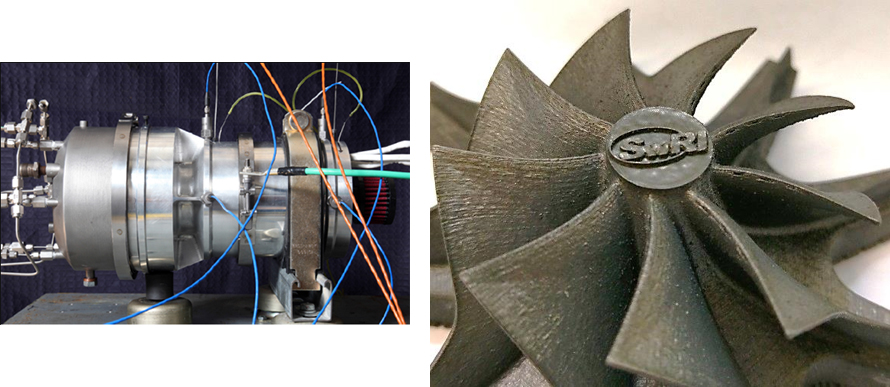
Figure 1: (Left) A 12.5 kW gas turbine generator designed and built at SwRI is being used to test the cooled radial impeller.
Figure 2: (Right) SwRI can successfully design, build, and test internally cooled impellers.
Accomplishments
The project successfully demonstrated that SwRI can design, build, and test internally cooled impellers (Figure 2). Lessons were learned during the impeller manufacturing process to help guide the schedule of post-processing.
Important features of the geometry were understood in this project, such as minimum resolution and the curvature of build surfaces. For example, turbulated channels as small as 0.50 mm could generally be built with similar resolution to 1.0 mm features (Figure 3). The importance of surface orientation was also demonstrated through building square passages that aligned with the build plane, compared to orienting the squares so that the edges were 45° from the build plane.
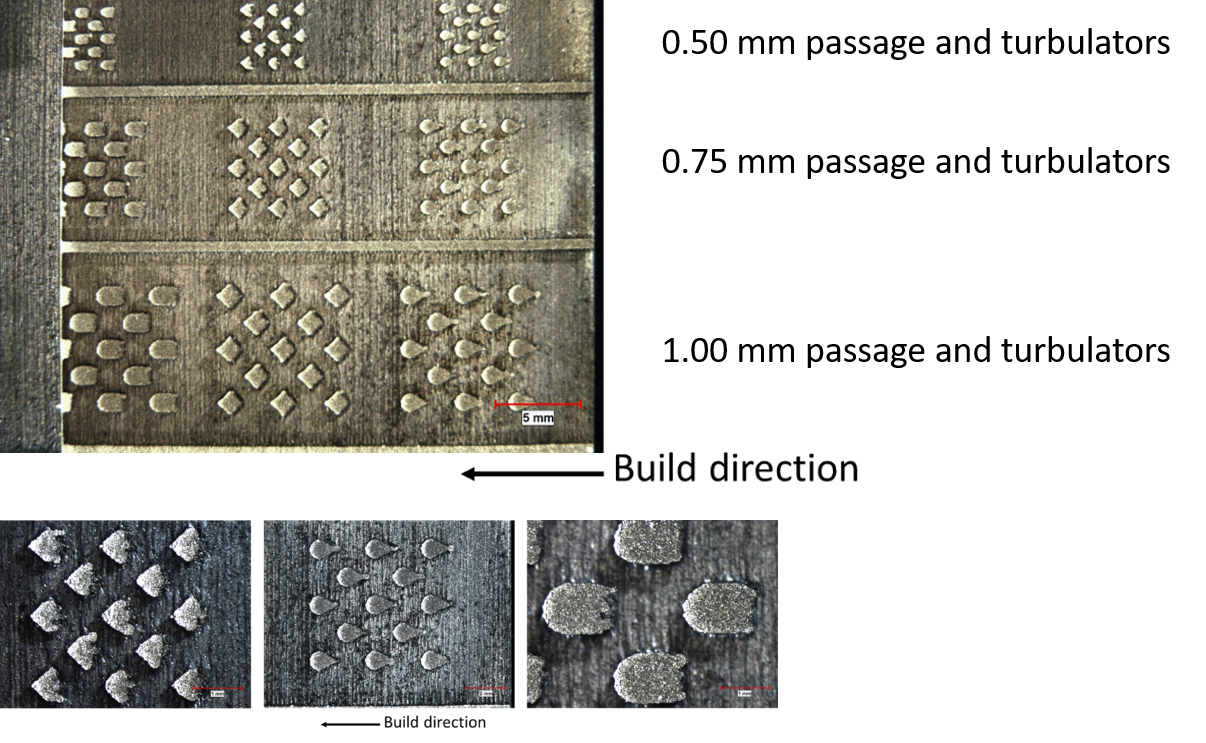
Figure 3: Generally, internal passage features as small as 0.50 mm are found to be built with similar resolution to 1.00 mm features.
The material properties of the AM material were found to be within 10% of a wrought material of the same alloy. Material tests were conducted after applying hot-isostatic-pressure (HIP) and heat treatment processes following ASTM F3055-14a and ASM 5663N, respectively. Additional testing is needed to conclude if the build orientation, thickness, or post-processing technique has an effect on the tensile properties of the material.
The cooling passages in the impeller were validated to show that the impeller results in a cooling effectiveness of 0.30, which is within the range estimated by the design model (Figure 4). Considering the simple cooling geometry used in the impeller, there is much room for improvement in future builds. For example, film cooling and internal turbulators can be used to enhance heat transfer. Future studies may also investigate the effect of build parameters on surface roughness to reduce pressure drop through the passages.
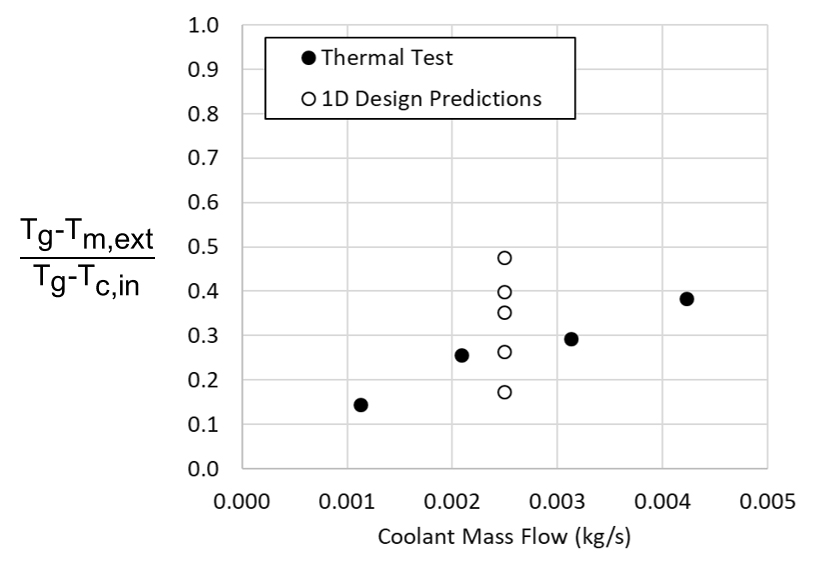
Figure 4: Measurements confirmed that the cooling effectiveness of the as-built impeller is within the range expected from one-dimensional (1D) predictions.