Additive manufacturing (AM) of metals is an advanced 3D printing process that offers unique and exciting capabilities for producing metal parts and components. While many traditional methods of fabrication selectively remove materials to produce a part, AM involves the selective “addition” of material, often in a layer-by-layer manner, to build or “grow” a part. AM revolutionizes the design space, allowing the fabrication of complex parts that are difficult, if not impossible, to produce using conventional machining and fabrication methods.
Currently, the metals AM marketplace exceeds $4 billion, and it is expected to reach $30 billion by 2025. AM is infiltrating a range of industries and applications, including the oil and gas, automotive, power generation, biomedical, aerospace and space industries.
In 2018, Southwest Research Institute added its first additive manufacturing capability for metals — a selective laser melting (SLM) machine to support Metal Additive Manufacturing Services. SLM is a novel AM process that involves dividing a computer-based rendering of the component geometry into a series of horizontal slices. Each slice represents an individual layer of the part, which is built using a fine metallic powder distributed across the build area. Software then drives a laser that selectively melts and fuses regions of the powder to the previous layer. The process is repeated, building up a three-dimensional component layer-by-layer.
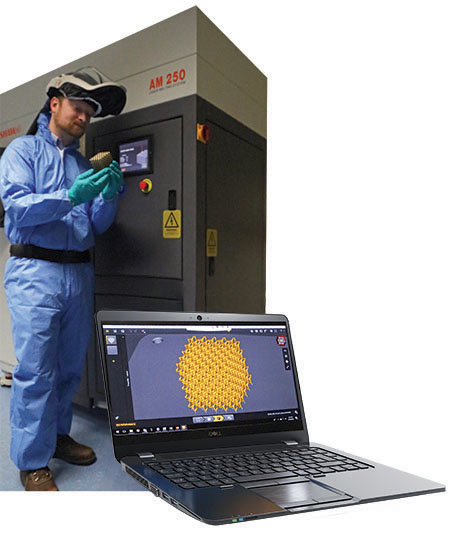
SwRI has added its first additive manufacturing capability for metals with a selective laser melting machine. AM revolutionizes the design space, fabricating complex parts that are difficult, if not impossible, to produce using conventional methods.
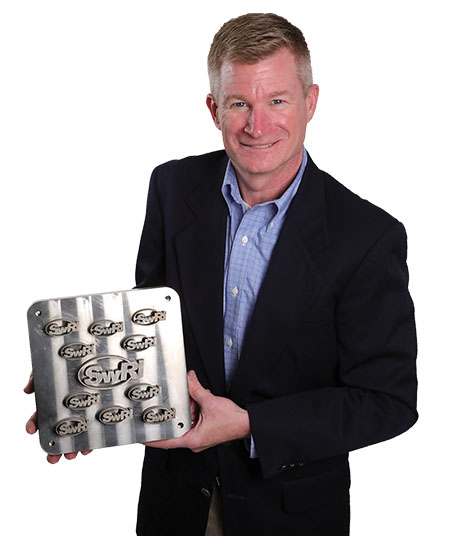
Dr. Carl Popelar, a staff engineer and one of the leaders of the MAKERS program, shows a demonstration build of the SwRI logo. Thin slices of the intricate logo (top of page) can be machined off the titanium build plate.
While AM has distinct advantages in creating parts with complex configurations, adoption of AM parts is hindered by the qualification of high-consequence parts fabricated using the new and unproven process. Unlike conventional subtractive fabrication processes where the properties of the excised part are those of a well-characterized wrought material, the AM build process produces both the part and the material simultaneously. As such, the part and material are inextricably related to the AM build process. Full realization of these advantages requires AM processes that reliably create parts with proper geometric form while at the same time producing material with appropriate performance properties.
Research and development are critical to understanding and ensuring that AM parts and their material properties meet both form and functional performance requirements. Because AM could impact many research areas across SwRI, materials engineers proposed a Metals Additive Kickoff Emphasizing Research Synergy focused internal research program. MAKERS was launched to advance the collective understanding of this emerging technology and foster collaboration Institute-wide.
Out of 22 concepts across multiple disciplines, the MAKERS advisory committee recommended 11 be developed into formal proposals, with the plan to fund five projects. In the end, the proposals proved so compelling that the advisory committee requested $1.4 million in internal research funding to support seven projects.
The projects were selected to advance SwRI knowledge in key aspects of metals AM and develop new capabilities to strengthen understanding of the AM process. The selected projects strategically spanned key elements of metals AM, from thermal load assessments to mechanical and corrosion characterization to nondestructive evaluation. Keep reading for a snapshot of each project, and consider the promises, challenges and advances of AM.
Questions about the MAKERS program? Contact Carl Popelar or call +1 210 522 4213.
1. Cooling Complex Castings
Industry Problem
The automotive engine industry faces conflicting development challenges driven by simultaneous requirements to reduce its carbon footprint while producing near-zero harmful exhaust emissions. Engines designed for increased power and reduced engine operating speed, weight and volume face increasing challenges for engine cooling and temperature control.
The most critical regions for engine temperature control are the cylinder head surface exposed to the combustion chamber and the upper cylinder wall. Today, coolant is delivered to these regions through channels produced with conventional casting and/or machining techniques, which limit the design options and mechanisms available to enhance heat transfer. Heat flux at any location is limited by the combination of available coolant velocity while avoiding surface temperatures so hot that all liquid in the vicinity vaporizes.
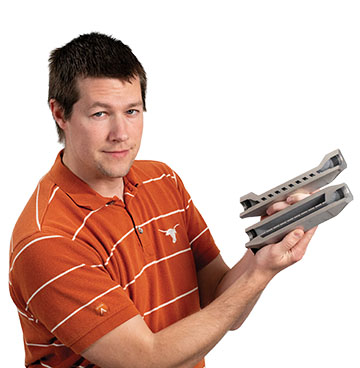
Matthew Hoffmeyer, a powertrain engineer, shows cross sections of two AM-produced cooling passages with complex internal geometries designed to enhance heat transfer in automotive engines.
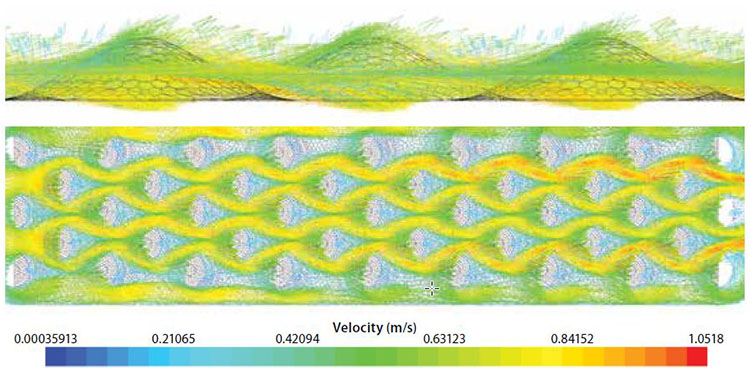
Dimpled geometry inside engine cooling jackets improved heat transfer by increasing local velocities and mixing. These figures show how the dimples create high-velocity flows weaving between the dimples.
SwRI Approach
Through the MAKERS program, SwRI engineers studied possible AM approaches to enhance heat transfer and minimize coolant pumping work. The team created five alternative cooling jacket geometries using AM in otherwise identical test scenarios and compared their performance to a rectangular baseline coolant passage. The team also developed new fluid flow models that can be scaled up and applied to simulations on entire cylinder head water jackets to improve analysis of existing water jacket designs while ensuring that new designs that incorporate complex features will be modeled accurately. The 3D modeling also provided insights into the mechanistic sources of the increased heat transfer. More complex internal features lead to more turbulent, higher velocity flows that generate higher heat transfer coefficients and increased mixing of the fluid, which causes it to absorb more heat.
Results
This project has demonstrated that complex geometries can double heat transfer without increasing the pumping work. Using these features within engine cooling systems can achieve higher rates of heat transfer in localized spots, such as the cylinder head fire deck, potentially allowing for more efficient cooling strategies. More effective heat transfer could improve overall engine efficiency by requiring smaller water pumps.
The team also considered using AM to construct a portion of the component, to integrate the AM enhanced cooling section into a larger, conventionally cast component. This option is an important consideration recognizing that the size of engine components probably precludes producing the entire component using AM.
Questions about this project? Contact Matthew Hoffmeyer or call +1 210 522 4538.
2. Internally Cooled Turbine
By Grant Musgrove, January Smith, Ellen Smith, Steve White, Charles Krouse and Nathan Andrews
Industry Problem
In the next five years, the utility industry will need internally cooled radial turbines for next-generation, distributed power generation. A cooled radial turbine is necessary for high-efficiency supercritical carbon dioxide (sCO2), direct-fired oxy-combustion and conventional power cycles. While the industry has developed cost-effective techniques for producing internally cooled axial turbines, producing radial counterparts using conventional manufacturing methods is cost-prohibitive.
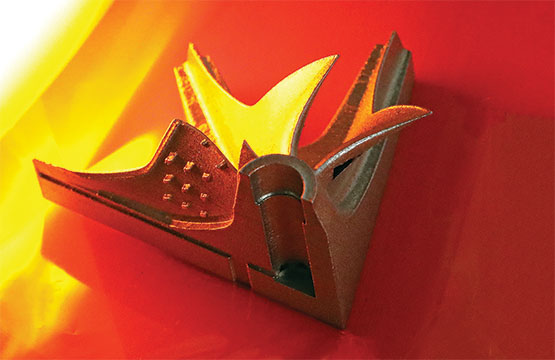
The cooled turbine is sectioned to show a small, internal cooling passage has been successfully manufactured into the turbine arm. Internal cooling channels reduce the operational temperatures by 415° F.
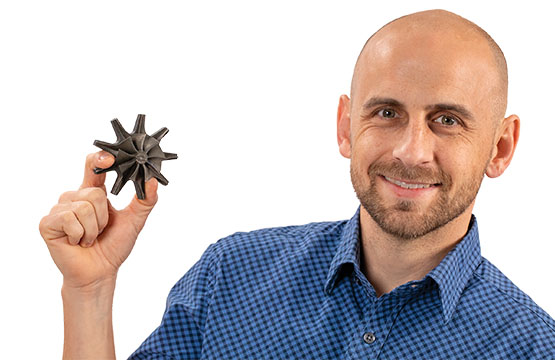
Grant Musgrove, manager of SwRI’s Propulsion and Energy Section, led a MAKERS project that successfully demonstrated the ability to design, build and test internally cooled, AM-produced turbines.
SwRI Approach
DETAIL
A radial turbine is a rotating mechanical device that extracts energy from a fluid flow.
This project used the SLM-AM process to build a radial turbine with small, internal cooling passages, allowing it to operate at higher cycle temperatures for improved cycle efficiency. SwRI designed, built and tested internally cooled turbines to overcome conventional manufacturing challenges and reduce production risk. Like traditionally wrought components, the devices needed post-processing by hot-isostatic-pressure (HIP) and heat treatment. Over the course of the project, the team learned to overcome challenges in SLM production and post-processing.
Results
The team produced both cooled and uncooled solid turbines using AM. The internally cooled turbine has a diameter of 3.3 inches and rotates at 118,000 rpm for this project. Testing indicated that the properties of the AM material were within 10% of a wrought material of the same alloy and that the cooled turbine decreased temperatures by over 400° F. For the demonstration project, engineers designed simple cooling geometries, allowing ample room for improvement in future builds. For example, engineers could use film cooling and internal turbulators to enhance heat transfer to operate at even higher cycle temperatures. Future studies may also investigate the effect of build parameters on surface roughness to reduce pressure drop through the passages.
Questions about this project? Contact Grant Musgrove or call +1 210 522 6517.
3. AM Space Bonding
By James Noll, Kenneth Domingue and John Roberts
Industry Problem
Space science instruments are typically assembled from metallic and ceramic parts. These dissimilar materials can be bonded into a hermetic assembly by brazing. Brazing is a metal-joining process that fuses two or more metal items by melting and inserting a filler metal into the joint. The filler typically has a lower melting point than the adjoining metals, or in this case, a metal coating on a ceramic subcomponent. One of the challenges in brazing metals to ceramics is managing joint interface stresses arising from mismatched thermal expansion between metals and ceramics during the brazing process.
SwRI Approach
The team is considering using AM bonding for a family of spaceflight mass spectrometers. The latest instrument, slated to fly on NASA’s Europa Clipper mission, uses a bolted construction to attach and align numerous ceramic-metal joints. The instrument’s hard vacuum operations environment requires a separate vacuum cover assembly. The novel ceramic-to-metal bonding method is directly applicable to the next generation of spaceflight instruments, for example, by allowing a mass spectrometer to serve as its own vacuum chamber, which could significantly reduce the instrument’s mass.
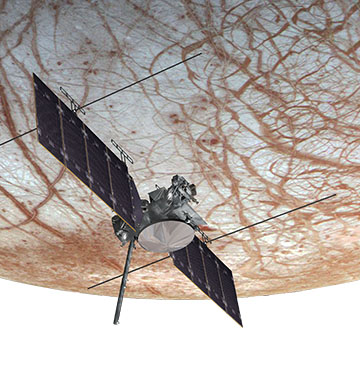
The team explored using AM bonding for a mass spectrometer slated to fly on NASA’s Europa Clipper mission.
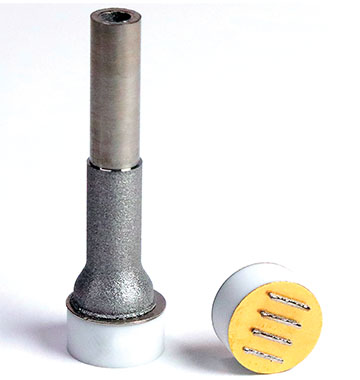
Through the MAKERS program, the team explored different materials and AM techniques for fusing ceramic and metal components. They used AM to affix a titanium tube to a nickelplated ceramic puck (left), studying how different footing designs and plating thicknesses affected the overall integrity of the bond. They also evaluated how AM titanium adhered to a goldplated ceramic puck (right).
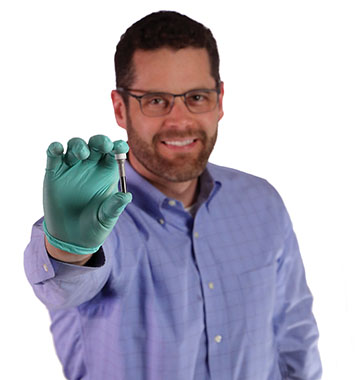
James Noll, a principal engineer in the Space Science and Engineering Division, shows the titanium tube described at left.
For the MAKERS program, engineers explored AM technology as an alternative to brazing to bond metals and ceramics for space and other high-vacuum applications. Using AM, SwRI fabricated and tested specimens and assemblies of increasing complexity to evaluate the leak tightness and structural integrity of joints as well as vacuum outgassing and quantification of virtual leaks. Engineers also investigated any issues with adapting AM parts for space applications.
Results
The team tried different parameters in design, materials, tools and coatings, making incremental improvements during the process. They eventually were able to create a metal-ceramic bond, but it lacked the necessary structural integrity. The research showed promise, however, for future applications for spaceflight instruments with additional process changes. For example, heating the build plate or thickening metals plating on the ceramic part could improve joint integrity.
Questions about this project? Contact James Noll or call +1 210 522 6389.
4. Platelet Powder
By Dr. Vicky Poenitzsch, John Macha, Dr. Carl Popelar and Dr. Kent Coulter
Industry Problem
The quality of the products made by SLM-AM is influenced by many factors, including the properties of metal powders that serve as the raw materials. The shape, size distribution, grain size, impurities, density, surface chemistry and roughness of the particles affect the composition and configuration of a final component. SwRI engineers are concerned that existing material sources will not meet the needs of future applications.
SwRI Approach
In this project, engineers investigated novel approaches for developing the next generation of AM source materials. Specifically, the team used a vacuum roll coating process to create engineered metal platelets. Engineers customized materials to increase powder density, layer and/or coat particles, control size and shape morphology, and tailor properties including surface textures and chemistries. The team characterized the structural and chemical properties of commercial powders and the prototype SwRI platelets using scanning electron microscopy, energy-dispersive X-ray spectroscopy and laser light diffraction to measure particle size distribution.
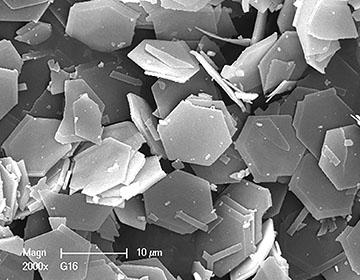
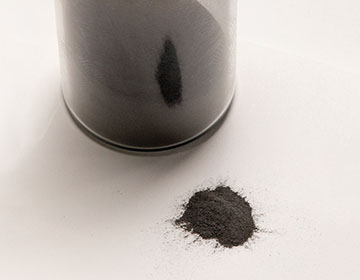
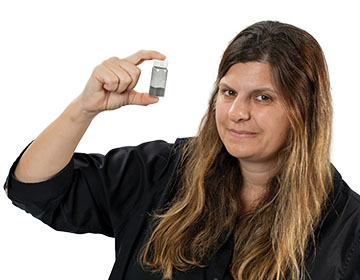
Dr. Vicky Poenitzsch, a manager specializing in thin films technology, investigated developing the next generation of AM metal powders that could play a role in solving today’s quality issues. Using a vacuum roll coating process as the source material for SLM-AM metal parts production, her team synthesized these titanium alloy 10-micron hexagonal platelets.
Results
The team synthesized titanium alloy 10-micron hexagonal platelets using a vacuum roll coating process. The goal was to manufacture SLM-AM parts using the engineered platelets and control SLM-AM parts made with commercially available powder to compare the structural, corrosion and mechanical properties of the parts. SLM-AM experiments and builds with the engineered platelets using manual powder distribution and standard build parameters revealed successful platelet powder fusion. However, powder dampness caused by the aqueous release method used to remove the platelets from the substrate resulted in poor flowability that inhibited the manufacture of SLM-AM test parts.
To address this issue, the team is considering changing to an organic release technique to remove the platelets from the roll. They are also considering improved post-processing steps to dry the powders. Otherwise, the project showed promise and has already resulted in a patent application and two conference presentations.
Questions about this project? Contact Dr. Vicky Poenitzsch or call +1 210 522 3755.
5. Qualifying AM Parts
By Dr. Adam Cobb, Dr. Jay Fisher, Albert Parvin, Dr. Teodor Dogaru, Dr. Carl Popelar and John Macha
Industry Problem
Using AM in fatigue-critical applications — where cyclic loading can cause progressive localized structural damage — is tricky. Nondestructive evaluation (NDE) techniques evaluate conventionally manufactured fatigue-critical components both during fabrication and throughout their service life but are not directly applicable for AM components. Because AM produces the component and the material concurrently, the properties of materials cannot be qualified in advance, and the AM process can produce flaws such as porosity, lack of fusion, warping and delamination. Additionally, the surface finish of AM components is significantly rougher than conventionally manufactured components, which can not only affect fatigue life but also reduce NDE performance.
SwRI Approach
SwRI investigated the performance of two NDE techniques on AM materials, eddy current testing (ECT) as a function of surface roughness and precision ultrasonic testing (UT) measurements to understand microstructural properties. Initially, the team produced AM test coupons with various surface and microstructural characteristics.
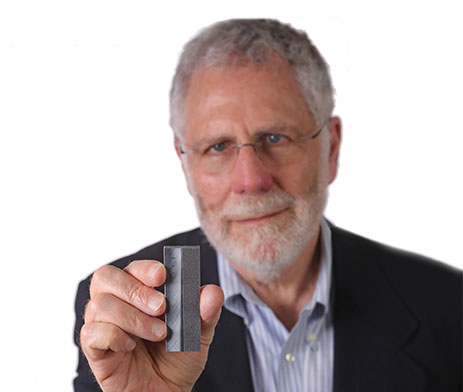
Dr. Jay Fisher, a program director in the Mechanical Engineering Division, was part of the MAKERS team investigating how to apply nondestructive evaluation techniques for AM materials and components.
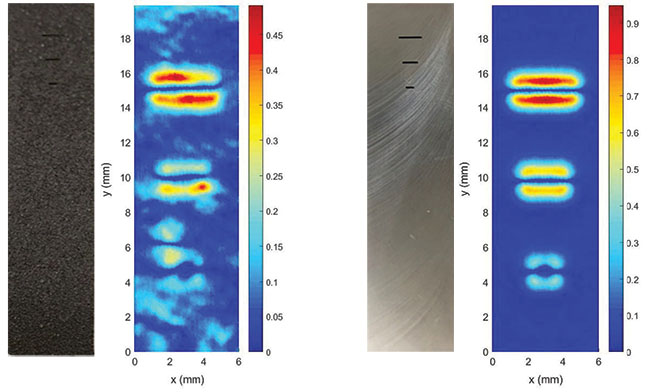
These AM coupons were machine smoothed on one side and notched on both sides to compare ECT data. As expected, AM surface roughness greatly reduced ECT performance by essentially creating a gap between the probe and the solid surface of the part.
To determine how surface roughness influenced ECT inspection, engineers added notches to test articles to use as reference features for detection. The team used established ECT procedures to assess the signal-to-noise ratio (SNR) to understand how roughness affected the data and determined that the main effect was to cause sensor liftoff during inspections. This gap reduced signal amplitudes overall but did not increase the ECT noise. Based on this result, the team developed a simple ECT probe lift-off signal model to correlate ECT performance to surface roughness.
DETAIL
A coupon is a small sample of the material under test that has been prepared in such a way that its failure mechanism will be representative of the larger production pieces.
The UT study sought to estimate material characteristics such as porosity using a combination of longitudinal and transverse acoustic wave velocity measurements. Engineers used a novel, SwRI-developed UT sensor and approach to measure acoustic wave speeds precisely. The team then developed a multimodal regression model to accurately estimate material porosity. Furthermore, using the combination measurements allowed engineers to compute the elastic properties of the material accurately.
Results
Through the MAKERS program, SwRI determined how AM production of parts affects both UT and ECT NDE techniques necessary to qualify components for fatigue critical applications. The intellectual property developed for the ultrasonic measurement technique positions the Institute to support the AM industry both by manufacturing NDE systems for production use and by providing qualification services for AM service providers.
Questions about this project? Contact Dr. Jay Fisher or call +1 210 522 2028.
6. AM Modeling
By Dr. James Sobotka, Matthew Kirby, Dr. Shengyen Li, David Wieland and Isaac Grothe
Industry Problem
Predicting the strength and durability of components produced with AM processes is a complex problem. The layer-by-layer deposition of material during AM produces residual stresses severe enough to distort components. Furthermore, the AM process introduces nonhomogeneous microstructures that alter material properties typical of corresponding wrought condition. Potentially, these and other qualities may be tailored in the AM process based on performance requirements.
SwRI Approach
To understand how to meet performance goals, SwRI needed to predict them accurately, which requires a credible AM process model.
Through MAKERS, SwRI developed a viable, computationally tractable, AM process framework to compute thermal profiles, residual stress, distortion, microstructure and material properties. Targeted to Ti-6Al-4V material and SwRI’s powder-bed fusion machine, the model can be extended to other AM alloys and similar powder-bed fusion systems. Predictions from this framework have been validated against SwRI-built sample “coupons” (made to NIST specs) and have been demonstrated using a real-world application, a redesigned T-38 dorsal cover.
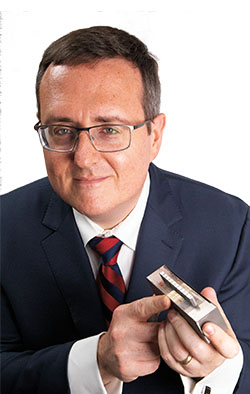
Dr. James Sobotka, a specialist in computational materials, developed a computational model to predict the material properties, strength and durability of components produced with AM processes. It has been validated against open-literature coupons and a demonstration using a real-world application.
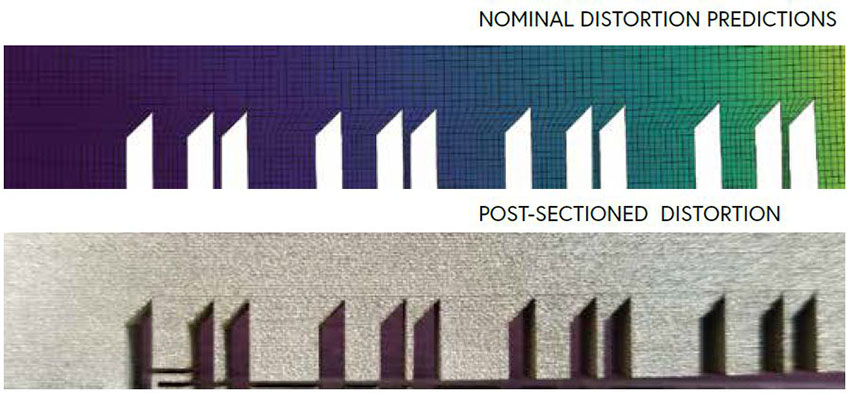
Engineers built a coupon specimen using SwRI’s AM machine, sliced its “legs” off the build plate and then measured specimen distortion. Distortion measurements show good agreement with predictions made with the AM process modeling framework.
The AM process framework represents a foundational building block needed to support process-structure-property performance work and provides a platform for future integrated computational materials engineering studies. Predicting residual stress could reduce the cost of AM builds and the number of failed builds due to part distortion and cracking. Predicting grain size will help to demonstrate “equivalent or better” yield stress properties.
Results
Potential applications for the model include supporting sustainment efforts on the large fleet of aging aircraft owned by the U.S. Air Force. Replacement parts for damaged structural components can be hard to find because an original manufacturer is out of business or fabrication processes are no longer available. This sustainment problem may be mitigated by using AM processes to quickly produce one-off components. However, these components must meet high quality standards for flight applications, efforts that can be accelerated and optimized by tractable computational models of the AM process.
Questions about this project? Contact Dr. James Sobotka or call +1 210 522 6417.
7. Springing Back into Shape
By Cole Buss, Nathan Weyandt and Dr. Carl Popelar
Industry Problem
Nickel titanium, or nitinol, has unique shape memory and elasticity properties attractive for applications ranging from biomedical to aerospace components. The material deforms at one temperature, then recovers its original shape upon heating above a “transformation temperature.” The material exhibits enormous elasticity, some 10 to 30 times that of ordinary metal. However, it is expensive, difficult to manufacture and challenging to machine and form into complex shapes.
SwRI Approach
SwRI engineers were curious about using additive manufacturing to print shape memory alloy (SMA) components from nitinol. Initial research focused on developing parameters using SLM to create components from NiTi powder to overcome challenges associated with standard nitinol materials.
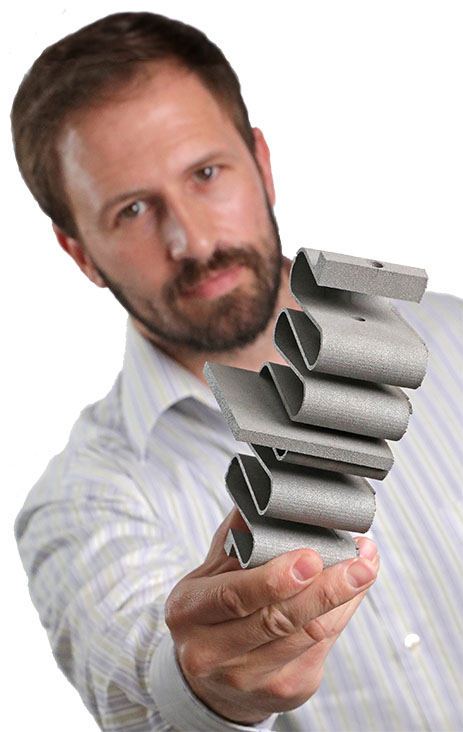
Cole Buss, a senior research engineer in the Applied Power Division, was part of a team investigating using AM to produce innovative nitinol shape memory actuators.
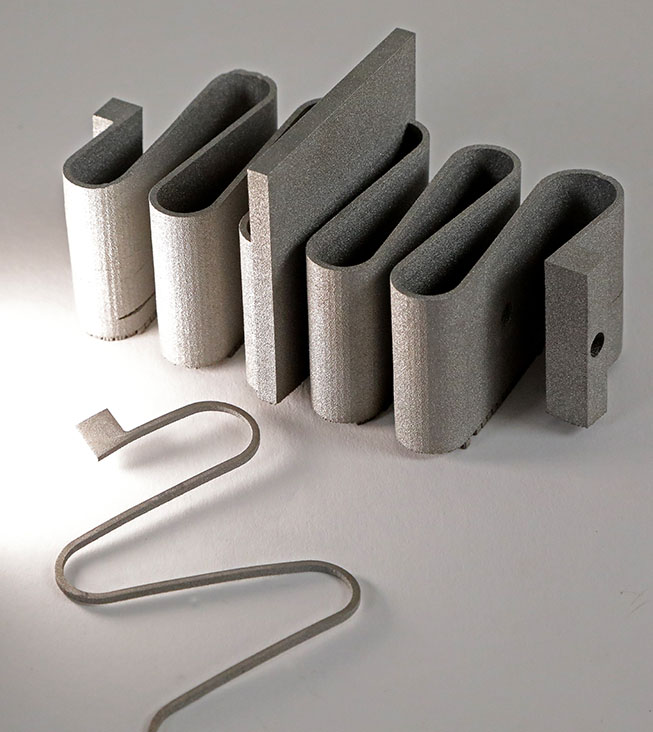
The dual-spring assemblies experienced cracking and delamination in the AM build process. However, these results, even with flaws, may be adequate for some applications. Shape memory testing of the partial bent plate was successful.
DETAIL
Nitinol is a nickel titanium shape memory alloy with a name derived from its composition — Ni and Ti — and its place of discovery, the Naval Ordnance Laboratory (NOL).
Small-scale test builds helped establish build parameters for shape memory springs using NiTi powder, with initial failures paving the way for more promising results. Engineers tested the tensile specimens to investigate the mechanical and shape memory properties of the printed NiTi materials and compared them to NiTi specimens fabricated from stock material. The AM specimen performed somewhat favorably, although the process requires more development and evaluation.
Results
While using AM from NiTi proved challenging, the project illustrated the complexity possible with the AM process while reducing waste material and tooling costs of traditional fabrication. Using stock material to fabricate something of similar size and complexity would be prohibitively expensive. This research is helping establish SwRI as a leader in nitinol technology, a growing enterprise that remains underdeveloped due to manufacturing and cost limitations.
Questions about this project? Contact Cole Buss or call +1 210 522 2390.