Background
Improved valvetrain processes including Variable Valve Actuation (VVA) and Miller Cycle valve events are key to enabling the design improvements necessary to meet the future engine efficiency requirements being imposed by greenhouse gas (GHG) regulations. There is now increasing interest in the application of VVA to heavy duty (HD) engines, with several major Tier 1 suppliers recently having announced VVA systems aimed at this sector, and this is a subject that clients are increasingly asking SwRI’s opinion on. While this topic has previously been investigated as part of several client projects and the CHEDE program, this project aimed to update and extend this work with a more flexible VVA profile and updated engine specifications including electrical EGR pumps and state of the art high efficiency turbos.
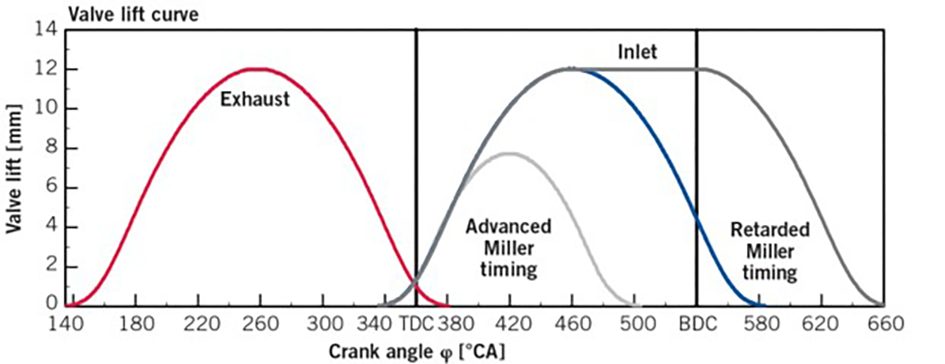
Figure 1: Inlet Valvetrain VVA-Miller Timing
Approach
Engine simulations were performed in GT-Power with a series of models featuring two different turbo configurations and inlet only VVA-Miller setups. The models were run at up to six steady state conditions, depending on configuration, that reflected the most highly used vehicle operating conditions from typical drive cycles. The results were used to determine the success of applying VVA-Miller to the HD engine. A target of 5% BSFC improvement was chosen along with increased BMEP levels. An important aspect of the modelling was to ensure that the models ran at comparable conditions, such as EGR and AFR levels, but particularly turbo efficiency levels to isolate the impact of the VVA-Miller valve events without the added gains from turbo efficiency differences. Cylinder de-activation (CDA) for exhaust thermal management and split exhaust manifold layouts for EGR control and reduced PMEP levels were also studied.
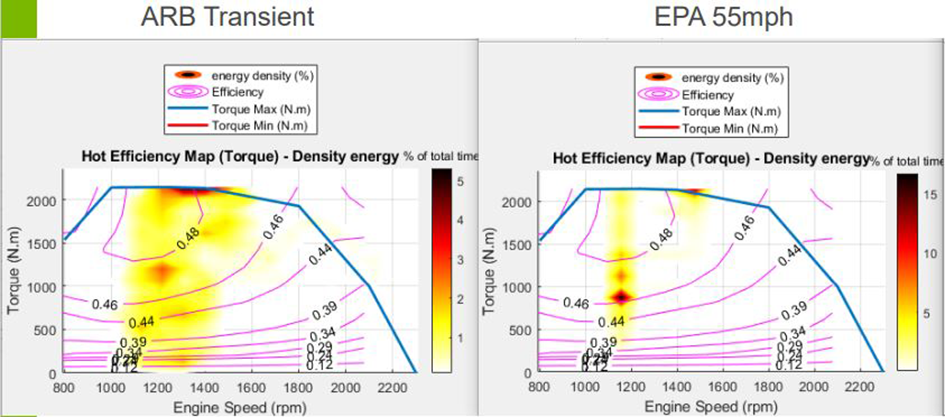
Figure 2: Operating Condition Heat Maps (supplied by ANL)
Accomplishments
The results of the study indicated that the VVA-Miller combination does have potential to both improve BSFC and increase BMEP levels. For the single turbo configuration, a maximum improvement of 4.4% BSFC was predicted with a corresponding +20% BMEP increase. For the two-stage turbo configuration, a maximum improvement of 5.1% BSFC was predicted with a corresponding +25% BMEP increase. Both these engine configurations featured increase compression ratio in conjunction with a 250-bar cylinder pressure limit and high efficiency turbos. For the thermal management study, where the single turbo model was operated at 1000rpm @ 300Nm, an increase in turbine outlet temperature of +76°C was predicted in addition to a 4% BSFC improvement. This aspect of the work will be further investigated to understand how such systems will be applicable to the CARB 2027 and EPA2027 regulations due out later this year which are expected to push for thermal management improvements at mid-low load operating conditions of up to 8bar BMEP, where traditional CDA techniques typically have a significant BSFC penalty. The project also highlighted the VVA operating range required to achieve these benefits.
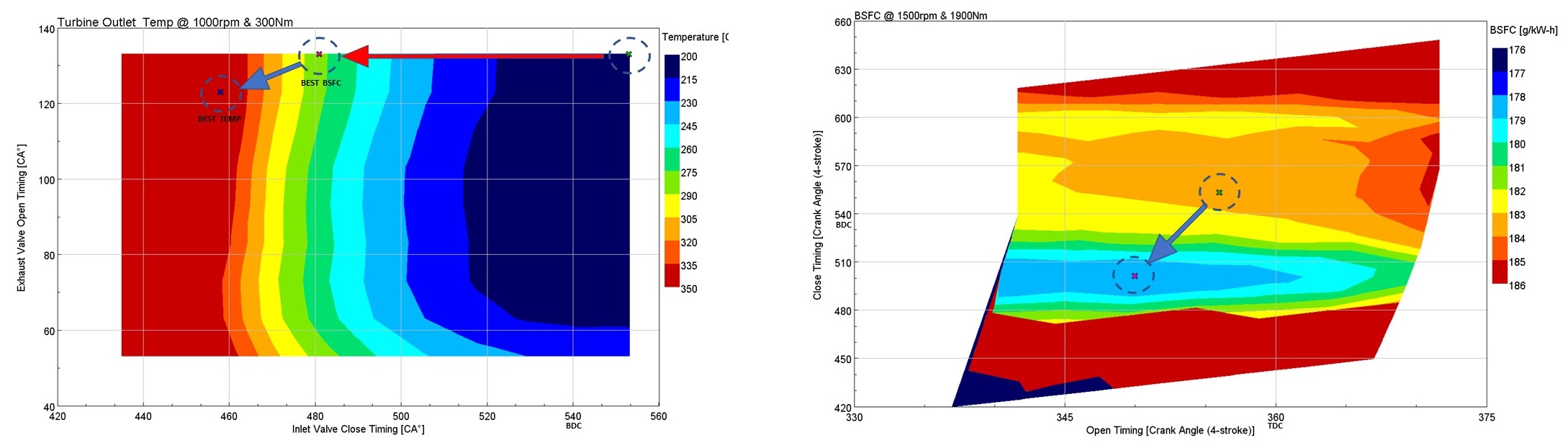
Figure 3a & 3b: Results of Study – Single Turbo & Thermal Management