Background
Two complementary programs have been undertaken to determine the real-world conditions that stress a fluid in an electric or hybrid-electric vehicle (EV/HEV) and determine what a “failed” fluid looks like at the end of its life. With this data, further developments can be made through funded projects or an industry consortium to develop EV/HEV fluid-specific controlled test methods to enable the industry to develop the best fluids for this market. Secondary objectives of this project are focused on improving our ability to operate EV/HEV powertrains both on a mileage accumulation dynamometer (MAD), as well as on a stand-alone test stand.
Approach
The project involves heavily instrumenting the test vehicles and performing durability testing. The gearboxes have been instrumented for coolant and oil temperatures and pressures, and the motor stators and stator jackets have been instrumented for surface temperature. The high-voltage direct current (DC), twelve-volt DC, and multi-phase alternating current (AC) electrical systems have been instrumented for current, voltage, and power where applicable. A high-precision power analyzer is being used to quantify electric power in the drivetrain. Additionally, three to five hundred controller area network (CAN) channels are monitored and recorded, including battery string voltages, battery temperatures, actuator positions, and other vehicle sensor data. The vehicles have been driven on a test track to construct a realistic drive cycle which is expected, and confirmed by the sensor data, to stress the drivetrain fluid and which is now run on the MADs. The vehicles will be operated on the MADs for one-hundred thousand miles while being monitored to determine an eventual failure point and mechanism. During mileage accumulation, data is recorded from the vehicles’ communication buses to enable operation of the vehicles’ inverters on a standalone test stand. Fluid samples are taken regularly, and using a series of non-consuming oil analyses, fluid quality is being tracked throughout the program. Overall vehicle efficiency is quantified at the beginning of the program using federal test procedure (FTP) and highway drive cycles. This will be repeated at the end of the program after a fresh fluid change, allowing the change in efficiency due to the fluid degradation to be quantified separately.
The two vehicles initially selected for this effort were a 2020 Chevy Bolt (08-R6033) and a 2021 Toyota RAV4 Prime Hybrid (08-R6172). The Bolt provided an opportunity to explore fluid degradation in a high-power density full electric vehicle. This program used DC fast charging between discharge cycles, allowing the team to quantify the effect of repeated high intensity charging on the battery and coolants. After the Bolt suffered a premature transmission failure, the team elected to restart the program using a more modern EV: a 2022 Hyundai Ioniq5. The RAV4 Prime is a plug-in hybrid vehicle and is equipped with Toyota’s latest hybrid 4WD architecture and controls. The powertrain is much more complicated than the Bolt or Ioniq5, with a 4-cyclinder engine, a front powersplit transaxle with two internal electric motors, and an electric rear axle. Multiple sumps, fluid types, and sources of tractive power give rise to additional constraints around the program design but also provide additional dimensions in which to explore fluid and vehicle degradation.
Accomplishments
The Chevy Bolt was purchased and instrumented. Traffic on the CAN bus was also collected, analyzed, and decoded, enabling data recording from this source in addition to the discrete instrumentation. Preliminary data was taken on the test track and on a chassis dyno, and this data was used to design a unique drive cycle which incorporates a standardized drive cycle modified to increase severity, recharging phases using regenerative braking, and steady-state conditions to allow baselines to be tracked throughout the program. The vehicle had completed approximately 43,000 of the planned 100,000 miles of testing before suffering a transmission failure. A post-mortem analysis revealed the severe regenerative braking duty to be a major contributing factor, so the revised program using the Hyundai Ioniq5 will be modified accordingly.
The RAV4 Prime has been purchased, disassembled, and instrumented. Similar to the Bolt, data on the CAN bus has also been collected, analyzed, and decoded. Exploratory teardown, photography, and rating of the two gearboxes is complete, the start-of-test efficiency evaluation has been performed, and the mileage accumulation will begin soon.
The Ioniq 5 has been purchased and instrumented and the CAN bus messages have been analyzed and decoded. After instrumentation shakedown and calibration, this vehicle will begin its start-of-test efficiency evaluation soon.
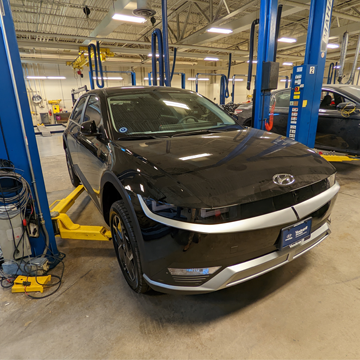
Figure 1: Hyundai Ioniq5 in D08 Fleet Lab
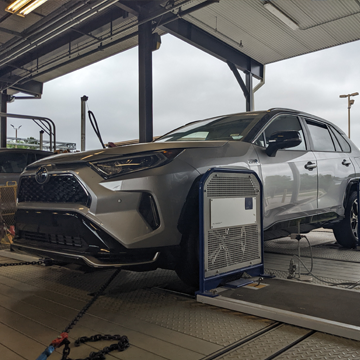
Figure 2: Toyota RAV4 Prime Hybrid Under Test at D08 4WD MAD
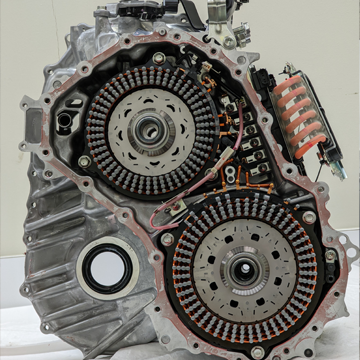
Figure 3: Exposed motor stator “hairpins”, rotors, and 6-phase electrical connections of RAV4 front drive unit.