Submitted by Victoria Wahlen on Fri, 06/10/2022
Whether you are adding another piece of automation to your factory floor or debating whether bringing automation into your operation is right for your business, there is a lot to consider. From new equipment to reorganizing floor space for the new set-up, you will have a laundry list of tasks to complete before your newly automated system is ready to use. One of the most important items on that list will be safety. How do you ensure this system is safe for those working around it? What additional items should be on the shopping list to aid in safety? What do you base your safety decisions around?
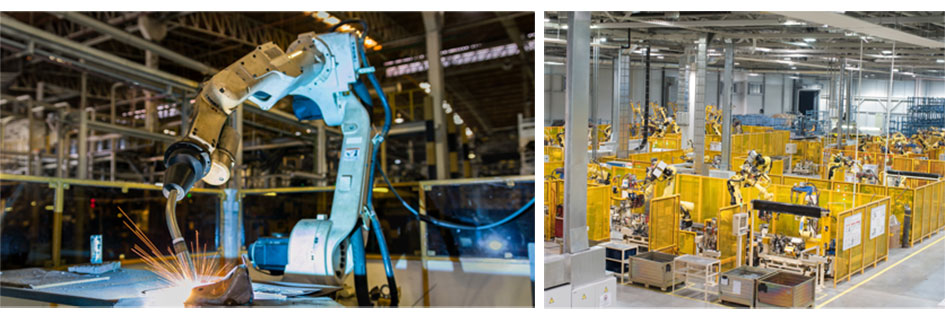
An industrial robot, left, welds a part while operating inside a “fenced” safety enclosure. Human operators stay outside such enclosures during robot operations. Several robots, right, perform a series of functions while fenced.
Let’s start with the basics. There are two main bodies that develop rules to govern the wide array of safety in automated robotic and manufacturing systems—ISO and RIA. ISO is the International Organization for Standardization, which is widely accepted worldwide, while the Robotics Industries Association (RIA) is primarily accepted in the United States. While the RIA recently converged with other organizations to become A3, the Association of Advancing Automation, A3 continues to refer to “RIA” for robotic safety standards.
Guide to Robotic Safety Standards
The ISO and A3/RIA organizations collaborate with other standard organizations, including International Electrotechnical Commission (IEC), National Electrical Code (NEC) and Underwriters Laboratories (UL), to appropriately reference the correct documentation and provide people with the safest guidance in the implementation of automated and robotic systems. When deciding whether to use RIA or ISO standards, the recommendation on which to follow really depends on where your company is headquartered geographically and where the system is going to be installed; both these organizations produce standards with a common goal of keeping people safe. At Southwest Research Institute, we tend to utilize both standards as we design and deploy our systems to ensure we are following a more “universal” set of guidelines. In the end, the importance lies in making a choice and utilizing its guidance to implement a safe system. A quick beginner’s reference guide for common application areas and applicable standards is listed below:
Automation and Robot Standards
RIA 15.06, ISO 10218-1, and ISO 10218-2 for Robotic System Safety
RIA 15.08 for Mobile Robots for Industrial Applications
Operational Safety Standards
IEC 60204 for Electrical Equipment Machinery Safety
ISO 13849 for Machinery Safety with regards to Control Systems
Performing a Robot Risk Assessment
If you are relatively new to navigating the world of safety standards, it can seem a little overwhelming at first. There are so many things to consider and so many ways to implement a safe solution. When considering safety for an entire system, safety experts tend to turn to something called a risk assessment. A risk assessment is a technique used to identify hazards associated with tasks that personnel would encounter for a given system and mitigate those risks.

Illuminated “Emergency Stop” buttons allow an operator to deactivate a robot in case of an unsafe condition. A light stack, right, features safety lights to alert operators of machine status.
To conduct a risk assessment, gather a representative group of people that will be working with the equipment—from maintenance to safety to process engineers. This group will brainstorm all potential tasks associated with the new system, the potential risk(s) of each task and determine a risk rating for each given task hazard. During the first iteration, tasks and hazards are based on the system with no safeguarding. Risk levels range from negligible to very high and are based on the potential injury severity, exposure, and avoidance possibility of each hazard. Depending on the risk rating of each hazard, risk reduction measures are determined and implemented into the system. This brainstorming process is then repeated, but this time, the system is analyzed with the newly implemented safeguards. Any risk severities that are still medium, high, or very high should continue to be reevaluated for more intense safeguarding, substitution, or elimination methods to reduce the risks to low or negligible. For more information and specifics, refer to RIA TR R15.306.
To define and mitigate risks, SwRI commonly implements the aforementioned risk assessment technique for systems before deployment at a client’s site. On one of our recent projects featuring mobile robotic surface processing, the danger for personnel while the robot is in operation is significant. To ensure a human could not get near the robot while in action, multiple layers of ESTOP conditions were implemented, including installing light curtains along the robot’s arms, laser safety scanners around the mobile base, and interlocks on the doors to close off the robot operational area from personnel. Warning signage and lighting was also implemented. This effectively reduced the risks of the robot to humans during processing, and some of these measures can be seen in the image of the robot and airplane.
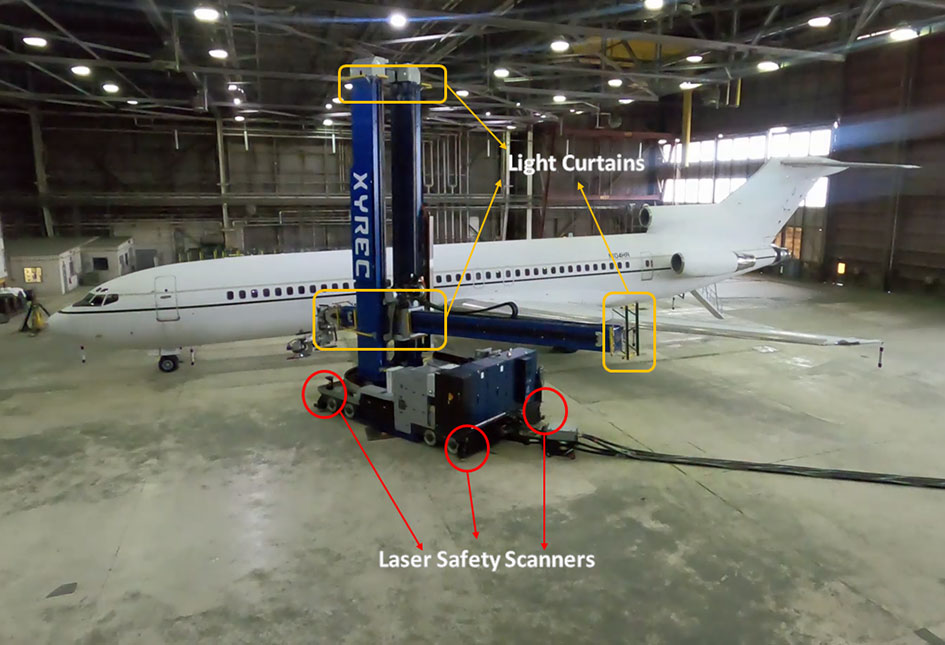
The image above depicts how SwRI implemented safety devices with multiple layers of ESTOP conditions, including light curtains, laser safety scanners and door interlocks.
On another mobile robot application, a similar safety system was deployed with laser safety scanners at the robot’s base and a restricted operational area. The main difference was the use of bumper switches instead of light curtains along the robot arm as seen below. Based on the risk assessment and task hazards, this was an appropriate choice.
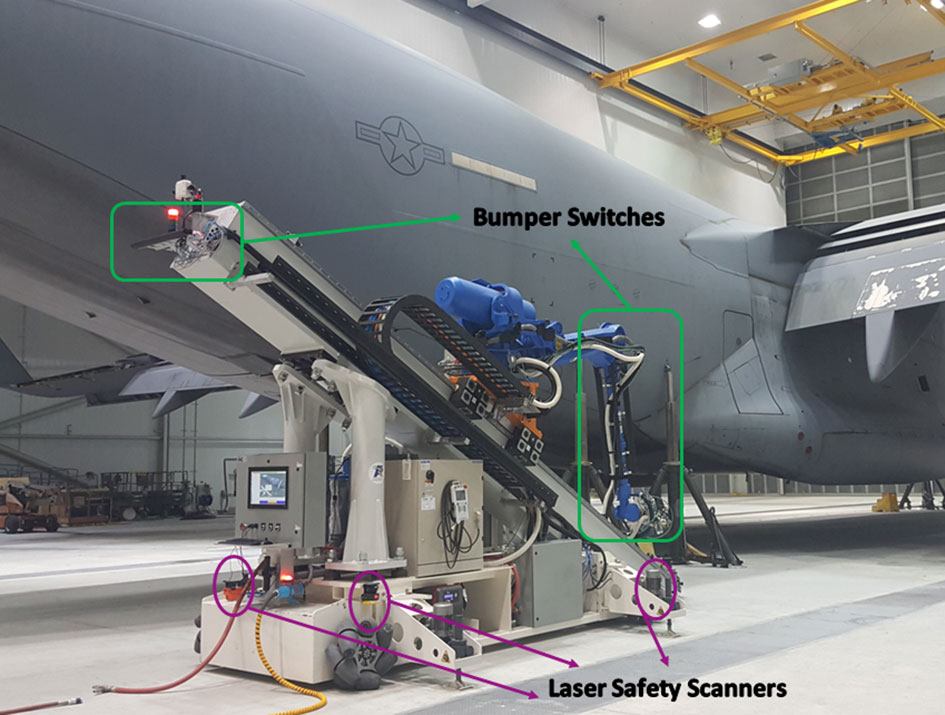
A comparable safety system with laser safety scanners and bumper switches.
Whether you are setting up your first automated system or your hundredth, analyzing the safety of each system is a critical step in this process and different for every machine and application. In a world driving towards more and more automation, keeping people safe is still the top priority.
For more information, please visit Intelligent Manufacturing & Process Solutions or contact Victoria Wahlen.